Injection Moulding Case Study & Fast Chain
Learn how Get It Made were able to help take Fast Chain from a prototype to a mass-produced product using Injection Moulding.
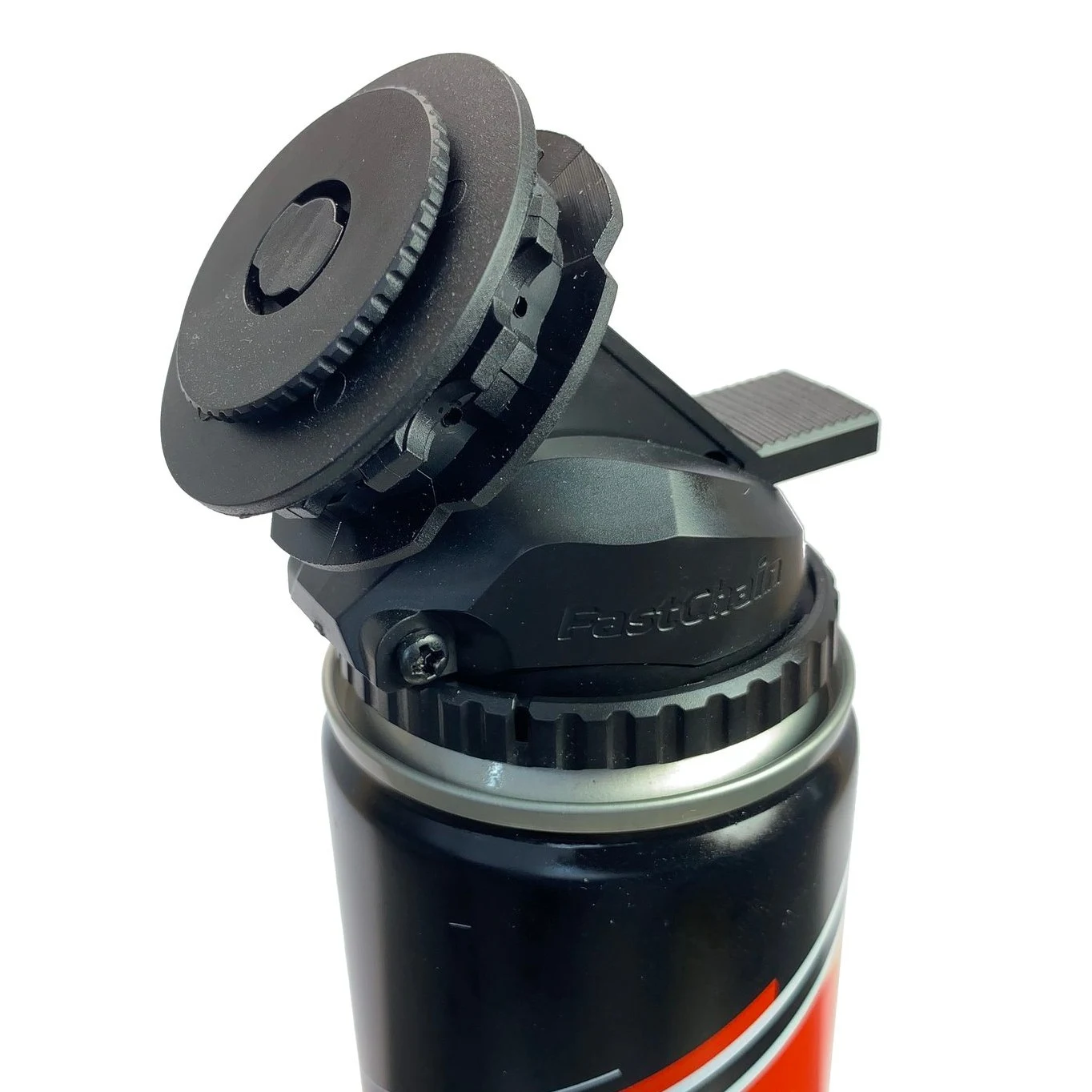
We were contacted by bike specialists ‘FastChain’ regarding a component that they believed could revolutionise the cycling industry. Using our Plastic Injection Moulding service, we were able to help take Fast Chain from a prototype to a mass-produced product, available to cyclists everywhere. Read on below for a case study on what the biggest challenges were, why Get It Made was the best option for this project, and any future work that may be on the horizon.
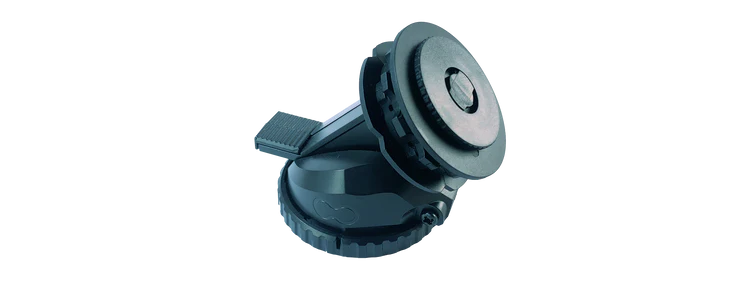
The idea of the product, and the reasoning behind its creation, is simple, as outlined by company founder Paul Lancefield:
“I have been creating prototype cycling technology solutions for a number of years. I mountain and road bike, and due to severe time constraints, my bike was always dirty. Somehow, my cycling friends always managed to keep their bikes clean. I have focussed on bike cleaning products and technology. One of the most important aspects of bike maintenance and performance relates to maintaining the chain and keeping it lubricated. But this can be difficult without taking the chain off the bike - which most people don’t want to do. The first device I created related to a button-activated steam cleaning “wand” where water mixed with a degreaser in a steam generator is fed through a sprocket similar to that found of Fast Chain, for cleaning the oil off a chain.
After creating a prototype of this device, I created a second prototype of a simpler device attached to an aerosol can (which has become FastChain) for re-lubricating the chain. When I first tested this device, I found the holes were too large, and the lubricant was applied faster than intended. But I found this had the secondary unexpected effect of cleaning the chain between the links as well as lubricating it and later realised this is because the propellant in Aerosol cans acts as an extremely effective solvent. So the device is simpler than a steam cleaner and cleans and lubricates all at once. So you could say, in part, the genesis of FastChain was the reapplication of a novel idea through a happy accident.”
Despite having a vision of the product, Paul was not an experienced designer, and as such his designs were not 100% optimised. Therefore, we had a lot of feedback and design suggestions to make the part more efficient and make the final product better suited to its desired purpose. This ability to ensure greater efficiency of the part being manufactured illustrates the expertise offered by our Project Managers and manufacturing partners.
“This was my first time working on a product from design to manufacture in large quantities. With Get It Made’s help, I feel the process has gone very well. It did take much longer than I expected. However, this is due to the considerable degree of work, attention to detail and patience provided by Get It Made, demonstrating real value.”
This project was manufactured using Plastic Injection Moulding. After ensuring the efficiency of the design and tooling was completed, we undertook T1 and T2 moulding trials to make sure that all parts were ready for customer approval. Due to Get It Made’s capabilities, we were able to mould the parts in high quantities, which amassed an initial order of 5,000 parts. Assembled and packed. Paul was already accustomed to this expertise, having enjoyed success on a previous project, in which CNC machining was employed.
“I had previously used Get It Made to obtain CNC parts for one of my earlier cycling-related prototype products. Though this was a much smaller job, I found working with the team so easy, and I got a glimpse into their tendency to ensure the right inputs are available to assure job quality as distinct from watching the clock or letting the customer make mistakes.”
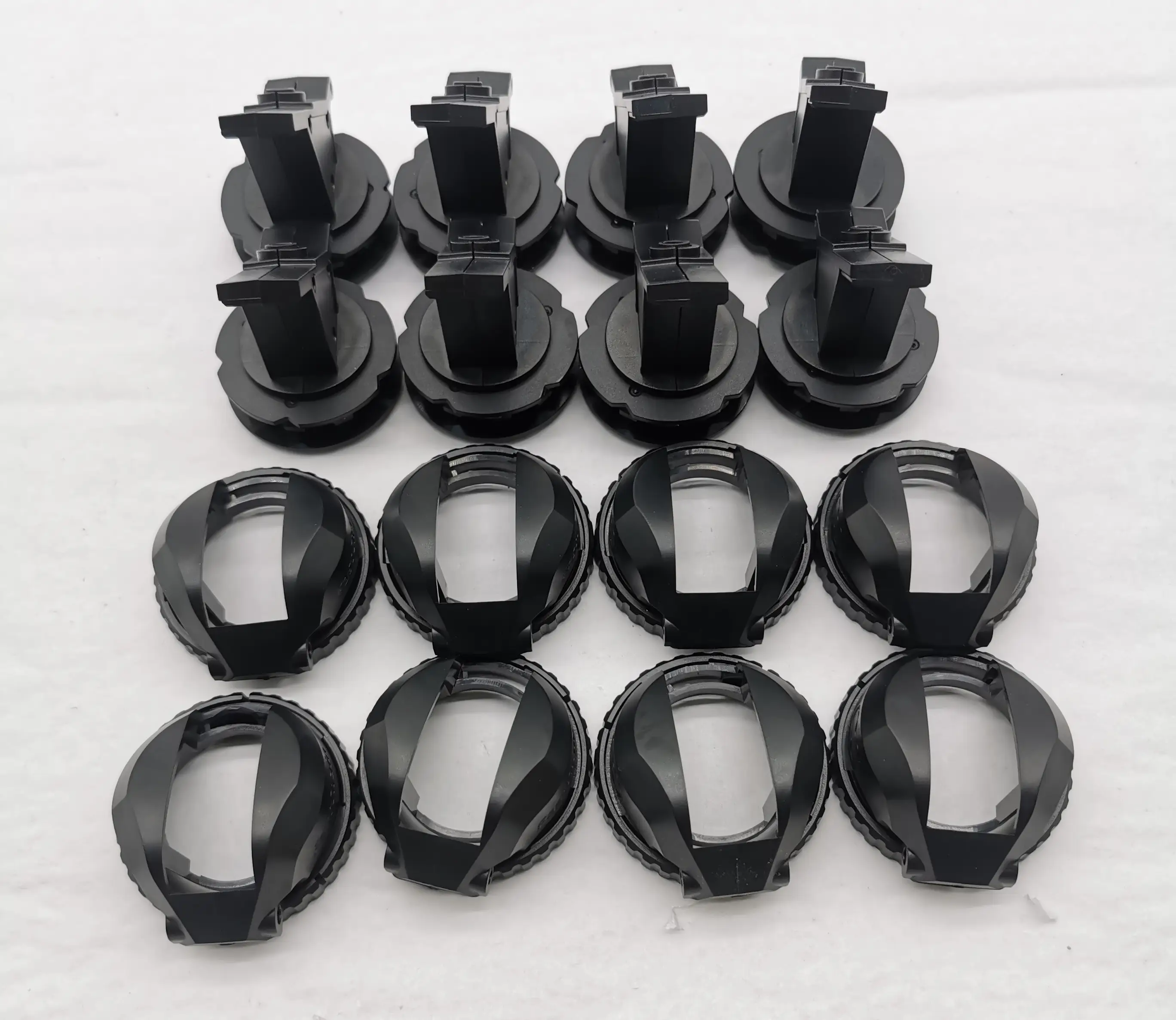
In addition to our manufacturing expertise, we take great pride in the customer service and excellent communication we provide to our clients. We believe all are vital to the success of any project. All aspects of good service are vital in the eventual success of this product. Paul illustrated this further when asked about his experience of working with Get It Made compared to our competitors, and whether he would recommend us to others.
“Definitely. I already have! Very good all the way through. I was not getting the same level of patience or the sense of care, I the customer - who is new to manufacturing - might be about to make a mistake. So I felt a sense of responsibility and care.”
After the success of this project, we asked FastChains founder Paul Lancefield whether there were any further ideas or concepts in the pipeline for innovating the cycling world even further:
“I have several projects in the works, however, these are currently paused while I focus all on marketing FastChain!”
For anyone looking to purchase any products on sale, visit Fast Chain.
When it comes to Injection Moulding, We offer expert advice on how to economically tool and mould parts. For example, we can suggest which parts could be moulded together in the same tool. If you need help with a project you are working on and want to speak to one of our dedicated Project Managers, visit Get It Made and get a Plastic Injection Moulding quote today.
Learn more about our Metal Injection Moulding service as well, should this suit your need.