The Basics
What is a CNC machine?
CNC (Computer Numerical Control) Machining is a subtractive machining technology that entails both milling and turning. The process uses physical contact to remove material from a solid block of material (known as the blank or workpiece ), using a range of cutting tools.
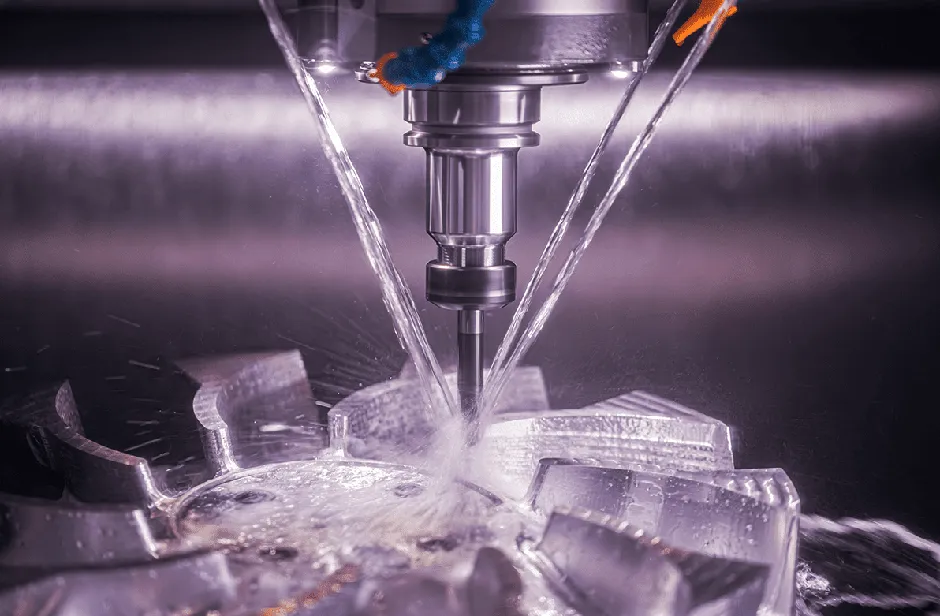
The CNC machining process is a digital manufacturing technology that produces parts with excellent physical properties directly from a CAD (computer aided design) file. This high level of industrial automation makes CNC machining suitable for a one-off part and mid-volume production. A wide range of materials can be CNC machined including, metals, plastics, wood, glass, foam and composites.
The basic process can be simplified into three main steps. First, a 3D model of the design is created using CAD software. Then the CAD file is converted into a CNC programme (G Code) and the machine is set up. Finally, the machine autonomously removes material from the workpiece to form the custom-designed part.
If you are curious to see the price difference between materials and surface finishes in CNC machining, we recommend reading through our how much does CNC machining cost article.
What are the different types of CNC machining?d
Intro into the types of CNC machines here and add a flow diagram showing how the methods are related to one another.
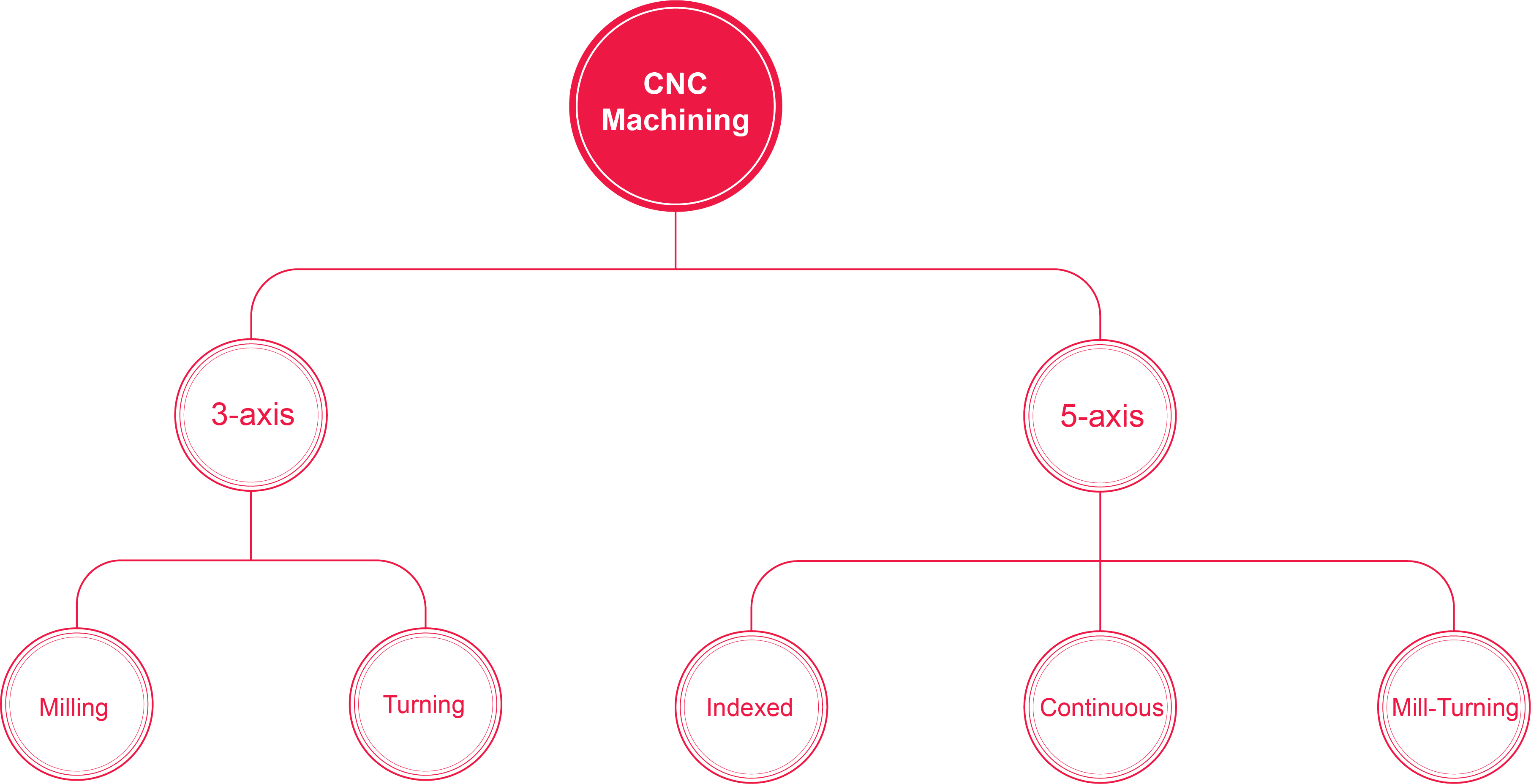
What are 3-axis CNC machines?
There are two main types of 3-axis machining; CNC milling and CNC turning. These two methods allow the machine tool to move in three linear axes relative to a fixed workpiece. CNC Milling and CNC Turning remove material from a fixed workplace using different cutting techniques.
CNC Milling
3-axis CNC Milling is a subtractive machining process that uses a cutting tool rotating at a high speed to remove material from a fixed workpiece. The tool is attached to a spindle and can move along three linear axes.
CNC milling is the most widely used of all CNC machining processes, as most simple geometries can be produced to a high accuracy using the method. Added with the relative ease of set-up and operation, the start-up machining costs are low. However, 3-axis CNC milling has limitations when geometries become more complex. As there are only three axes to work with, there may be areas the cutting tools will not be able to reach. Therefore, there are some design restrictions for 3-axis CNC milling; these will be covered later on in the design guidelines section.
Our beginner's guide on CNC Milling can help you with any specific questions you may have about the process. In a nutshell, it is a popular choice for producing industrial products and parts.
CNC Turning (CNC Lathes)
CNC turning is a subtractive machining process in which the workpiece is held in a chuck and rotated, while the tool is fed into the workpiece to remove material. The tool is programmed to trace the outer and inner shapes of the part to create the desired geometry. The tool does not rotate and moves around the workpiece radially and lengthwise.
CNC turning can produce parts at a much greater speed and thus the manufacturing costs are lower compared to CNC milling. The increased machining speed also makes larger volume production feasible. However, the main limitation of CNC turning is that it is only suitable for geometries with rotational symmetry. To overcome this design constraint CNC milling is often used as a secondary machining step to create additional features. These two processes can be streamlined into one by using a 5-axis machine.
Find out more about Get it Made’s CNC Turning services here.
{{cta-banner}}
How does a 5-axis CNC machine work?
5-Axis CNC Machining or multi-axis machining is an incredibly versatile machining process that adds two degrees of freedom to either a CNC milling or CNC turning machine. The extra two degrees of freedom come from the ability to rotate the workpiece, the tool head or both in addition to the three linear axes of movement. This introduces the A,B,C axes which rotate around the X,Y,Z respectively.
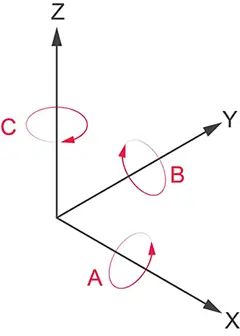
The additional degrees of freedom allow for greater tool accessibility which enables more complex geometries to be machined. There is also the added benefit of single-setup machining, sometimes known as 'Done-in-One' which increases efficiency by reducing machining time.
There are three main types of multi-axis CNC machines: 5-axis indexed CNC milling, 5-axis continuous CNC milling and 5-axis milling/turning machining centres.
What is 5-axis indexed CNC milling?
5-axis indexed milling, or 3 + 2 machining, works by rotating the workpiece around the B and C axis to the required position. The workpiece then remains stationary while the tool makes the desired cuts moving about its three linear axes. When changing the cutting location, the B and C axis will re-orientate the workpiece and then remain stationary again for that cutting location. This machining method is also known as 3+2 CNC milling since the additional two degrees of freedom do not work simultaneously with the three linear axes of the tool.
The main advantage of this method is that it eliminates the need to manually reposition the workpiece. This reduces the manufacturing time and increases the accuracy of CNC parts with complex geometries compared to using 3-axis milling.
What is 5-axis continuous CNC milling?
5-axis continuous CNC milling machines are similar to 5-axis indexed CNC milling machines, however, the workpiece can continuously rotate around the B and C axes during machining operations.
Between them, the workpiece and cutting tool can move along five different axes simultaneously, enabling complex features to be machined. Smooth contoured surfaces, like those found on a turbine blade, can be produced to a very high accuracy making this method popular in the aerospace industry. The combination of expensive machinery and the need for high-level machinists increases the cost of this method significantly.
What is a milling-turning centre?
Milling-turning centres known as Mill-Turn machines are as the name suggests a combination of CNC milling and CNC turning machines. The workpiece can be rotated at a high speed on a rotation axis for CNC turning operations, then subsequently rotated and held at a precise angle for CNC milling operations.
Mill-Turn machines provide manufacturers with a combination of the increased productivity of CNC turning with the design flexibility of CNC milling. These multi-functional CNC machines are ideal for parts that require multiple machining operations. Machining in one complete cycle results in faster part production and increased accuracy as there is no need for additional setups. Due to the increased efficiency of CNC turning, parts can be produced at a much lower cost than other 5-axis machines.
CNC machining summary
- 3-axis CNC milling is the best option if your part has a relatively simple geometry, as it provides excellent accuracy at a low cost.
- CNC turning is perfectly suited for parts with rotational symmetry, it can provide tight tolerances and a low cost per unit.
- 5-axis index CNC machining is suitable for more complex parts; greater part accuracy and production speed can be achieved as only one setup is needed.
- 5-axis continuous CNC machining is best suited to parts that require smooth-contoured faces, however, this does come at a high cost.
- Mill-turn CNC machines can manufacture parts at a lower cost to other 5-axis machines if the part has some features with rotational symmetry.
CNC Processes
CNC Machining is more than just cutting materials; it's a symphony of coordinated manufacturing processes driven by digital instructions. At its core, the CNC process begins with a CAD model, which is then converted into a CNC program. This program guides the machine's movements with utmost precision. The material is then fixed onto the CNC machine, and the cutting or shaping process commences. Throughout the machining operation, continuous feedback ensures accuracy, while advanced tooling techniques optimise efficiency. The result? Parts that meet exact specifications, every time.
CNC Machine Tools
CNC machines can utilise a wide range of cutting tools from end mills to tapping mills, making them highly versatile machines. Gaining an understanding of what cutting tools are available and how they can be put to use will help you design parts that are better suited to CNC machining. This section will cover some of the most commonly used cutting tools and what they are used for.
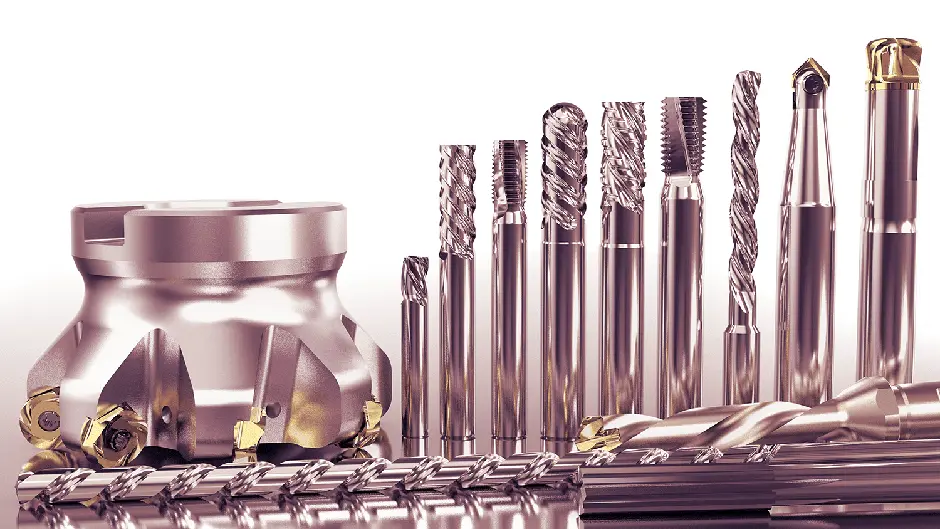
Flat End Mill - A flat end CNC mill tool is used for roughing and cutting 2D features such as engravings into a part.
Bull Nose End Mill - The flat base cutter with rounded edges make this tool suitable for machining cavities that require a radius at the bottom of the wall. This tool is often used for roughing as the corner radius is less prone to breakage.
Ball Nose End Mill - The ball-shaped cutter has a hemispherical end which makes it ideal for machining high quality three-dimensional contoured surfaces.
Roughing End Mill - This type of end mill has serrated teeth so that the tool can quickly remove large amounts of material. This tool cuts with less precision than a standard end mill and leaves a rough finish on the part
Face Mills - This circular milling tool has a flat end with multiple carbide cutters and is often used at the start of the machining process to create a flat face onto the workpiece. The multiple cutters mean material removal is fast while leaving an ultra-clean surface.
Drills and Reamers - Drills are the most cost-effective way to produce round holes in a workpiece. For non-standard hole sizes, a Reamer tool can be used to enlarge a drilled hole to a very specific size and tolerance.
Taps and Thread Mills - Taps are the most commonly used tool for creating threads however, with a CNC machine a thread mill can be used to cut internal or external threads. Thread mills are better suited for hard materials that can be difficult to penetrate with a tapping tool
What are the advantages of CNC machining?
✅ Accuracy, Precision, Repeatability
CNC machining is a highly accurate and repeatable process. Tight tolerances of ±0.02 and ±0.01 can be achieved for CNC milling and CNC turning respectively. As the machining process is automated, parts can repeatedly be produced accurately. More information on tolerances can be found in our geometric dimensioning and tolerancing page.
✅ Fast production speeds
CNC machining is an automated process that can work continuously without a break. This means parts can be produced with minimal human input, increasing productivity and efficiency. Typically parts can be manufactured in a matter of days ready to be delivered, making CNC machining excellent for getting parts produced on demand.
✅ Consistent material properties
CNC machining uses physical contact to remove material from a solid block of material, rather than thermally transforming (such as injection moulding). This means all desirable mechanical properties are retained. The only material requirement is that the part is adequately strong to be held and machined.
✅ Can scale from custom, one-off parts up to mid-volume production
Using CNC machining can be the most economically viable option to produce one-off designs or for rapid prototyping as no custom tooling is needed. In particular, when working with metals CNC machining is the most cost-efficient process for producing custom designs.
What are the disadvantages of CNC Machining?
❌ Limited tool access creates design restrictions
As CNC machining is a subtractive manufacturing process that removes material from a solid blank, the tool needs to access all necessary machining surfaces. Features such as undercuts and internal geometries cannot be machined due to restricted tool access. Furthermore, CNC machining cannot cut sharp internal corners, you can find out how to resolve this issue in our CNC machining square corners article.
❌ Complex geometries are expensive
Parts with geometric complexities come at an increased cost as they often require the use of more expensive multi-axis CNC machinery or manual repositioning of the part. See the section below on cost reduction tips to help keep part costs at a minimum.
❌ Tighter tolerances increase the cost
Machining tighter tolerances add additional costs as special measurement tools and slower machining speeds are needed. Generally, the softer the material is, the harder it is to machine a specific tolerance due to the material flexing when machining.
❌ Initial start-up costs are relatively expensive
A trained professional is needed to perform the part setup, CNC programming and tool choice which is a fixed cost. By manufacturing multiple parts at the same time the fixed cost can be shared, making each individual part more economical. The initial costs are still much lower than processes that require the preparation of custom tooling (injection moulding or investment casting).
CNC Machining Design Guidelines
This section will outline some of the key design considerations that will help improve the manufacturability of your part, resulting in higher quality parts at a more competitive price.
Sharp internal corners
You can find out more on alternative methods to solve the sharp internal corner problem here, CNC Machining Square Corners.
Undercuts and internal features
Minimum wall thickness
Cavity depth
Hole depth
If a deep small diameter hole is required in your design, Electrical Discharge Machining can be used.
Tall features
CNC Machining Materials
When selecting a material it is important to consider the mechanical properties, surface finishing, manufacturability characteristics and cost. CNC machining can be performed on a wide range of materials. Get It Made offers multiple grades of metals, plastics and more, please see the list for a sample of the materials we work with below. If you require material that is not on this list, please do get in touch as it is likely we can source it for you.
Metals
Aluminium
Aluminium is a very versatile material that can be alloyed with a whole range of elements to create lots of interesting alloys. It is easily machined, has a great strength-to-weight ratio, is non-corrosive, non-magnetic and has good heat/electrical conductivity. Due to its versatility, its the most commonly used material for CNC machined components.
Stainless steel
Stainless steel is best known for its high tensile strength and thanks to its increased chromium content it has excellent corrosion resistance. It can be polished to a high-quality surface finish making it popular in the medical and food industry. We have an in-depth article that discusses the use of Stainless Steel in CNC machining.
Mild steel
Mild steel or low-carbon steel is the world's most common form of steel. It is an affordable, versatile material that has great mechanical properties, machinability and weldability. It is also magnetic due to the high amounts of ferrite and iron it contains. Mild steel can often be found in construction frames.
Alloy steel
This class of steel has been alloyed with several other elements to enhance various material properties such as strength, toughness, hardness, fatigue and wear resistance. Alloy steels can be found in a wide range of industries due to the many types of alloyed steel available.
Tool steel
At Get It Made, we often work with D2 steel which is a high-carbon, high chromium alloy steel that has extremely high hardness, toughness and resistance to wear/abrasion. It can be hardened with little distortion. As the name suggests the material is most commonly used to manufacture machine tooling (dies, stamps, moulds).
Titanium
Titanium is lightweight and has a very high tensile strength even at elevated temperatures. It is silver in colour and resistant to corrosion in seawater environments. Titanium can be alloyed with other elements to create strong, lightweight aerospace parts such a land gear. It is also biocompatible making it popular in the medical industry for implants.
Brass
Brass is one of the oldest metal alloys, compromised of copper and zinc. It is known for its decorative characteristics with a bright gold appearance. Other interesting properties are its low friction and corrosion resistance making it popular for musical instruments
Copper
Copper is commonly chosen for its high electrical and thermal conductivity, hence why it is often found in electrical equipment. It is also very ductile, highly resistant to corrosion and has antibacterial properties making it great for food preparation.
Plastics
ABS
Acrylonitrile Butadiene Styrene (ABS) has high tensile strength with excellent resistance to physical impacts and chemical corrosion. It has a nice glossy finish and is used in a broad range of industries from automotive components to LEGO bricks!
POM (Delrin or Acetal)
Polyoxymethylene (POM) is available in two different resins: copolymer (POM-C) and homopolymer (POM-H), POM-C has higher stiffness and POM-H is more ductile. They both have high tensile strength, rigidity, wear-resistance and great sliding properties. It also has excellent machinability and dimensional stability, make it suitable for complex moving components.
PEEK
Polyether ether ketone (PEEK) is a colourless high-performance thermoplastic with excellent strength to weight, high resistance to thermal degradation and hard-wearing. Coupled with its dimensional stability and machinability make it popular for the medical Industry. It is one of the few plastics that can be used in the aerospace industry.
PP
Polypropylene (PP) is a tough material with strong fatigue resistance, it can retain its shape after being deformed making it a good material for living hinges. Another key quality is its high resistance to electricity making it useful for household and industrial electronic components.
PC
Polycarbonate (PC) is a transparent thermoplastic with excellent strength, stiffness, toughness, dimensional and thermal stability, making it one of the most widely used thermoplastics. It can be used as a lighter, stronger alternative to standard glass.
HDPE
High-Density Polyethylene (HDPE) has great low-temperature impact resistance, excellent toughness and chemical resistance. It can also be easily recycled making it a popular material in multiple industries, from kitchenware to pipes used in construction.
Nylon
Nylon is a popular polymer with outstanding mechanical strength and wear performance while being lightweight, making it a great material for bearings and rollers. It also has good resistance to most chemicals however, it does have high moisture absorption affecting dimensional stability.
Surface Finishing
Surface finishing is the final step taken when manufacturing a CNC machined part. There is a wide range of post-processing techniques that can be used to improve the appearance and performance of a part. This section will outline some of the commonly used finishing options that offer unique benefits.
What is an As Machined Finish?
The raw finish left on a part that has been manufactured using CNC machining is called 'as machined'. The part will have small but visible machining lines from where the cutting tool has subtractively removed material but will still be smooth to touch. The average surface roughness on an 'as machined' part is Ra 3.2 (3.2 μm). Additional finishing cuts can be performed to reduce the surface roughness further but this will increase the part cost. This finish offers the best dimensional accuracy so designers looking for parts with tight tolerances should choose an as machined finish.
What is Bead Blasting?
Bead blasting is a reductive finish where a pressurised gun fires a stream of abrasive glass beads at the part to remove a thin layer of the surface. The process creates a consistent matte/satin surface finish on the part and is often used to remove tooling marks/imperfections. It is important to consider the thin layer of material removal if your part has features with tight tolerances.
Bead blasting is a manual process that requires a trained technician to perform. Different sizes and grades of beads can be used to vary the abrasiveness of the bead blasting.
What is Mirror Polishing?
Mirror polishing is a mechanical process that involves sanding down any imperfections using progressively finer abrasives, before polishing/buffing the part to give a shiny mirror-like surface. The finish is highly reflective, smooth and free of any scratches. Mirror polishing is often performed on materials such as stainless steel and Al7075, softer metals like Al6061 risk having their surface deformed when sanding down. The added benefit of mirror polishing is its resistance to corrosion. The highly smooth surface finish means corrosive particles cannot harbour scratches.
What is Electropolishing?
Electropolishing, also known as acid polishing, is an electrochemical process used to reduce the surface roughness of the material to give a smooth, shiny finish. The process works by passing a current through a workpiece submerged in a bath of electrolytes. This causes the peaks on the surface to oxidise and dissolve faster than the recesses, resulting in a smoothing of the surface. This process is commonly used in combination with anodising to give a shiny anodised finish to parts.
What is Electroetching?
Electroetching, also known as acid etching is an electrochemical process used to roughen the surface of the material to give a matte, textured finish. The process works in the opposite way to electropolishing, passing a current in the opposite direction through the workpiece submerged in a bath of electrolytes and a block of the same material. The metal is then dissolved from the block and deposited onto the workpiece, forming a rough surface. This process is commonly used in combination with anodising to give a 'super' matte finish to parts.
What is Anodising?
Anodising is an electrochemical finishing process that adds a natural oxide layer to the surface of the part. The anodic coating protects the part from corrosion and can be dyed in a variety of colours (At Get It Made we can anodise to any RAL number). The coating is electrically non-conductive so masking can be applied to areas that need to remain electrically conductive. Also, masking should be applied to features with critical dimensions such as threaded holes. Aluminium and titanium are the most commonly anodised materials. There are two types of anodising, Sulphuric anodising (Type II) and Hard anodising (Type III).
What is Type II Anodising?
Type II is the standard variation of anodising and is used to improve the aesthetics and provide effective corrosion resistance. However, it has limited wear resistance. Clear/un-dyes coatings typically have a thickness of 5-15 μm and coloured/dyed coatings 10-25 μm.
What is Type III Anodising?
Type III anodising also known as 'hard anodising' is similar to Type II but produces a thicker oxide layer, which increases corrosion and wear resistance. Type III anodising can also be coloured using dyes but the added thickness makes for a duller finish. A thickness of 20-80 μm can be achieved.
Tips for Designers
All parts that are anodised need to be held during processing. Holding points will not be anodised so it is advised to add instructions on your engineering drawing where contact marks are permissible. Contact marks can often be hidden in small and inconspicuous locations such as inside thru-holes.
When anodising the oxide coating ingresses into the material as well as growing on the surface. A good design guideline to follow is that 50% of the anodic coating is below the original surface and 50% is above. Therefore, a 12 μm coating would increase the part thickness by 6 μm.
What is Powder Coating?
Powder coating is similar to spray painting however a uniform powder similar to baking powder is used as opposed to wet paint. Parts are primed with a phosphating or chromating coating to improve their corrosion resistance. A process called electrostatic spray deposition is used to apply the powder coating to the part. This is where an electrostatic charge is applied to the powder particles, which are then sprayed and attracted to the part. The coating is strengthened by curing at a high temperature to solidify the bonding.
Powder coating provides a very durable and attractive finish that can be applied to any metal. Multiple layers of powder can be applied to create a thicker coating, with a maximum achievable thickness of 80 μm. Because powder coating doesn’t use any solvents and has little wastage it is an environmentally friendly option compared to liquid paints.
Cost Reduction Tips for CNC Machining
This section will outline some simple adjustments you can make to your designs to help reduce the overall part cost. There are three main areas that will significantly affect the cost of your part:
- Design - Complex parts result in increased machining time.
- Material - The cost of the bulk material and how easily it can be machined.
- Quantity - Cost per unit reduces with an increase in quantity due to fixed setup costs.
Design
Increase radius
The cutting tools used in CNC Machining have a circular cross-section and must also rotate in order to provide the cutting mechanism. This means the tool will naturally cut curved internal corners known as fillets. To reduce machining times, add the biggest possible fillets to your design which will allow a larger tool with a higher material removal rate to be used.
Avoid tall features and thin walls
Both tall features and thin walls are prone to vibration when CNC machining, which can result in warping or fracturing of the part. To minimise part vibration the cutting tool has to make multiple slow speed shallow cuts into the workpiece. This increases the machining time considerably which in turn increases the part cost.
Use standard holes
Standard holes sizes can be drilled quickly and accurately with drill bits. However, if you require a non-standardised hole CNC machining will need to be used, increasing the cost. It is also important to keep holes a suitable distance away from the edge of the part to avoid creating a problematic thin wall feature.
Blank size
The 'blank' is the stock block/rod of material that is loaded into the CNC machine ready to be machined. The size of the blank used depends on the bounding volume of the part, therefore, protruding features can have a large effect on the material costs and increase the bounding volume. Try to consider the size of the bounding volume when designing your parts to help minimise material costs.
Tolerances
To manufacture holes, walls and threads to tight tolerances is an expensive process as it requires an iterative slow machining process, increasing machining time. Parts also require post-machining inspection using a micrometre or CMM, further adding to the cost. It is therefore advised to only add tolerances to critical features in your design. Soft materials or designs with thin features are tricky to machine to a tight tolerance due to the part/tool flexing/vibrating when machining.
Avoid adding embossed text
When it comes to adding text/logos engraving is preferred to embossing as it requires less material removal, saving time and money. A Sans Serif style font is recommended with a minimum point size of 20 and an engraving depth of 0.3 mm. There are multiple other ways of adding text on parts such as laser etching and silkscreening which can be cheaper alternatives.
For more information on how to reduce CNC machining costs, click to view our cost-reduction tips for CNC machining here.
Getting Your Part Made
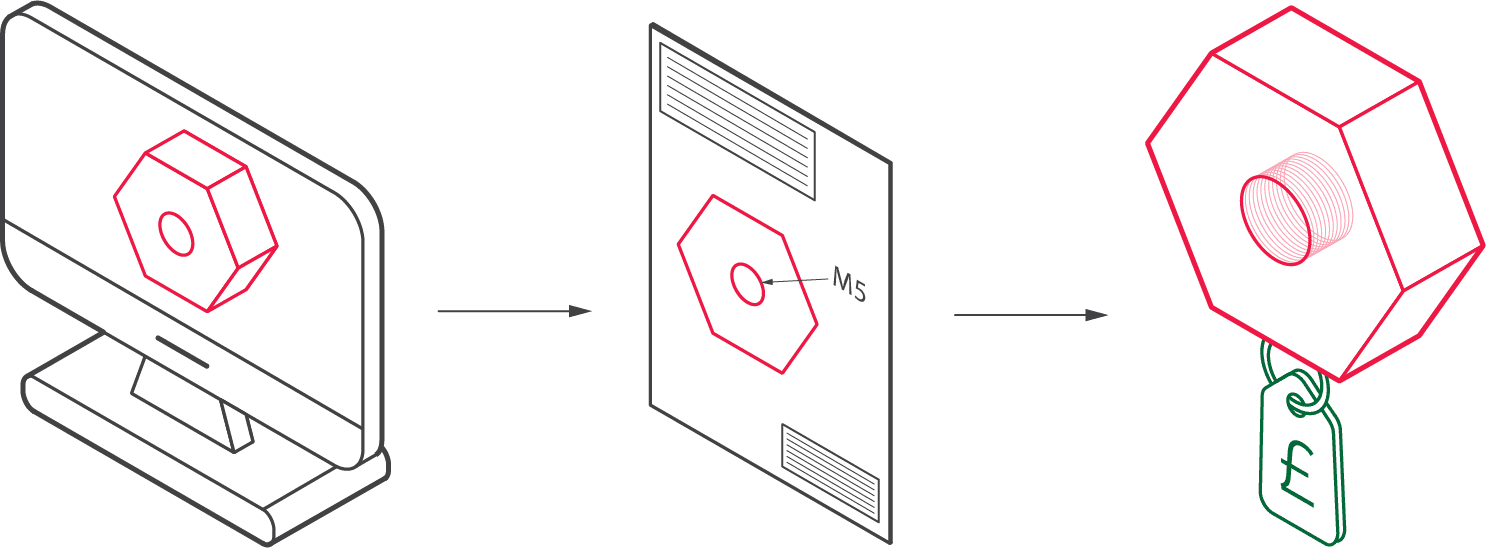
1) Design and export your CAD file
Use the CNC Machining Design Guidelines to help design your parts ready for machining. Then please export your 3D CAD files to STEP, IGS or PARASOLID format. Unfortunately, we can only accept STL files for 3D printing projects. We cannot accept OBJ files as they do not correct geometric data for manufacturing.
2) Create an engineering drawing
We highly recommend sending supporting PDF engineering drawings for each part. This is required when a part has: thread holes, critical dimensions, tolerances, specific finishing requirements. In some circumstances such as highlighting a threaded hole, we can accept an annotated screenshot. To find out more about thread holes, we highly advise looking through our threads terminology page, and our metric thread chart.
3) Get a Quote in 24 hours
If you would like to receive a free CNC machining quote from one of our engineers, please fill out a quote request form and we will review your project within 24 hours. They will then help fine-tune your project to make sure you get the best possible price and lead time for your CNC machined parts!