How much does Injection Moulding cost?
In general, injection moulding tooling can cost from £2k to £100k. Costs for moulded parts can range from a few pence to a hundreds of pounds each.
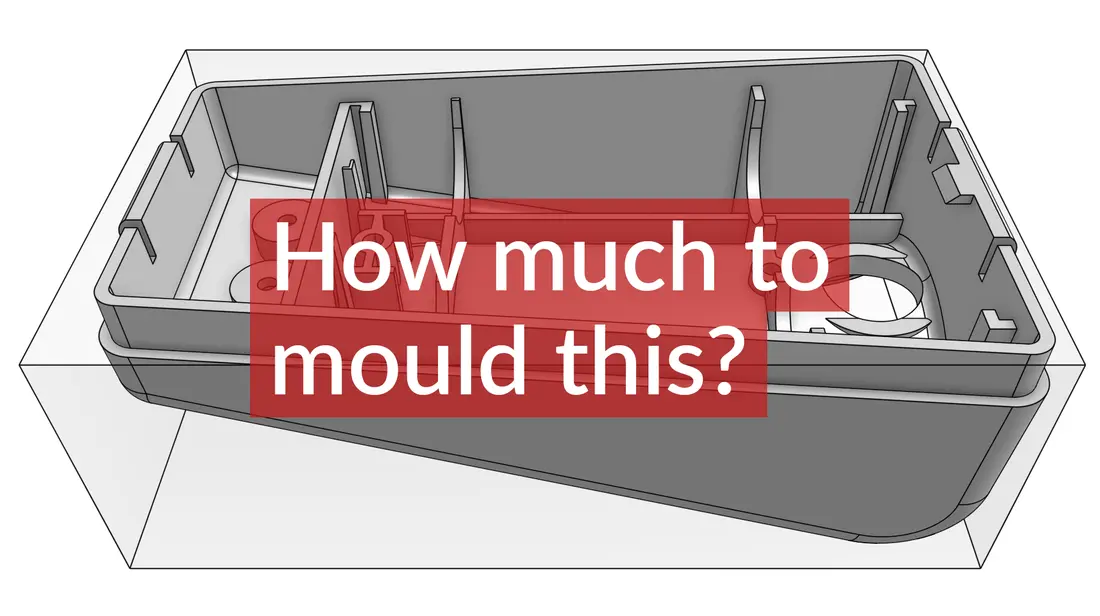
Introduction
Injection moulding is a manufacturing process often used to produce high volumes of plastic parts. This manufacturing process starts by creating and machining a mould with precision to form the part’s features. Then molten plastic resin is injected into the metal mould cavity. The plastic moulded parts subsequently cool and are ejected from the mould cavity.
If you want to know more about the injection moulding process, read our Injection Moulding Guide.
Tooling is often a key part of the economics in plastic injection moulding, this is because it is a large up-front investment. And this cost needs to be amortised into expected part volume, over a number of years. If injection moulding isn't suitable, it is very possible 3D Printing or CNC Machining could be a better option. Depending on the parts' features, the machining of a complex mould will require more time and expense, increasing the upfront costs of the project. This is the main reason why injection moulding is mainly used for high volumes.
However, once you have the moulding tool, the plastic moulded parts will have a very low unit cost. And the tooling is usually CNC machined from a high quality steel, allowing more than one production run using the same tool, so it will last many years.
It is essential that the design of the injection moulded parts are carefully reviewed before production. Removing unnecessary features from the parts will make the tooling easier to machine. Read our Injection Moulding Design Guide to optimise your parts and get a better price for your project.
In this article Get It Made simulated the production for two different parts, a very simple small part, and a more complex larger part. You can see how prices vary between different common injection moulding materials and part quantities moulded.
Request your free injection moulding quote today and one of our engineers will personally review your project within 24 hours. They will then help fine-tune your project to make sure you get the best possible price and lead time for your injection moulding project.
Read our other pricing guides for CNC Machining, Aluminium Extrusions and Aluminium Die-casting parts.
{{cta-banner}}
Plastic Injection Moulding costs, simple part
.webp)
Below is a cost comparison between Nylon, ABS and Polycarbonate (PC) for a simple injection moulded part. The table/graph also compares how the number of parts ordered affects the price and lead time.
For Nylon, going from quantity of 500x to 5000x has a 88% total cost per part saving for a simple injection moulded part. For volumes around 500x and below, it can often be cheaper to CNC machine or 3D Print the parts depending on the design. This is because the high tooling costs are spread over a smaller number of parts, making each part more expensive. Going from 5000x to 50,000x sees an additional cost saving of 9%. This demonstrates how increasing the part quantity significantly reduces part cost for smaller volume orders. However, as the order quantity increases, the reduction in unit price becomes less but still significant.
When comparing the three materials, the data shows that ABS is the cheapest material to manufacture with, and polycarbonate is the most expensive. The lead time only increases by a few days going from 500x to 50,000x. This is because the bulk of the lead time for an injection moulding project is manufacturing the mould and sampling. Once the mould produces parts to specification, part production is very fast.
If you want to know more about materials options for your injection moulding project, read our article about choosing the right Injection Moulding material.
Plastic Injection Moulding costs, complex part
.webp)
Below is a cost comparison between Nylon, ABS and Polycarbonate (PC) for a complex injection moulded part. There is also a comparison of how the price and lead time change according to the number of parts ordered.
The data shows a slightly different trend for a larger, more complex injection moulded part than the simple/smaller one analysed above. There is a saving of 79% going from 500x to 5000x in nylon and a further 12% going up to 50,000x. This shows that there are still substantial cost savings in manufacturing into the high thousands for larger, more complex parts. The price for 500x is comparable to 3D Printing as the tooling cost is a relatively smaller proportion of the unit cost than the small/simple injection moulded part.
The data again indicates that ABS is the most cost-effective to manufacture in out of the three materials, while polycarbonate is the most expensive. With an increase in quantity from 500x to 50,000x, the lead time only increases by a few days. This is primarily because most of the lead time in an injection moulding project is manufacturing the mould and sampling. Once the mould successfully produces parts to the desired specifications, the parts can be produced rapidly.
Read our article to find cost reduction tips for Injection Moulding projects.
Summary
- ABS is the cheapest material to mould in, but the price difference is negligible when moulding in higher quantities. Therefore, performance and aesthetics should be the main factors in material selection.
- Depending on the design, CNC machining or 3D printing can be a more cost-effective option for producing parts in volumes of around 500x or less.
- The increase in lead time from 500x to 50,000x is only a few days, so it is recommended to produce as many parts as possible per project using moulding to maximise the cost benefits fully.
- Injection moulding is a highly cost-efficient method for manufacturing plastic parts, particularly when producing thousands of parts at a time.
Ready to see how much your part costs to manufacture? Request a free Injection moulding quote today, and one of our engineers will review your project within 24 hours.
Check our Resources section to find all the information you need for designing and manufacturing.