The Basics
What is aluminium extrusion?
Aluminium extrusion is a process that is widely used in the manufacturing industry to create parts with a uniform cross-sectional profile. Aluminium is utilised due to its ductility, mechanical strength and cost-effectiveness. You can find out more about our Custom Aluminium Extrusion services here.
How does aluminium extrusion work?
Aluminium is forced through a die (a specialised tool used to shape material) that has been designed and manufactured to create the desired cross-section. Extrusion can be performed at high temperatures (350°C+) to reduce work hardening or at room temperature to improve surface finish and strength.
What are custom aluminium extrusions used for?
Aluminium extrusion is widely used in manufacturing to create parts with a constant cross-section. Aluminium extrusions are often used for:
- Industrial applications
- Architecture and Construction
- Automotive
- Signage and Lighting
{{cta-banner}}
What is the aluminium extrusion process?
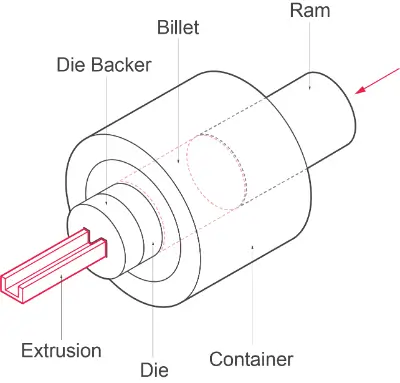
Aluminium extrusion as an end-to-end process is composed of the following steps:
- The die is first manufactured from tool steel, typically using CNC machining and/or Electrical Discharge Milling.
- A billet of aluminium alloy is heated. The normal temperature range will be 420°C-500°C.
- The billet is loaded into the extrusion machine with lubricant to reduce friction in the process.
- A high-pressure ram forces the aluminium billet through the machine towards the die.
- Nitrogen is introduced and allowed to flow through the die sections creating an inert atmosphere. This increases the lifespan of the die.
- The extruded aluminium exits the die in the required shape and passes onto a runout table, followed by a cooling table.
- Once cooled, the extrusion is then cut to the required length, typically this is achieved through a sawing process. However, at Get It Made we choose to use wire EDM to ensure a clean cut.
- Finally, the extrusions undergo any further processing or finishing if required.
What are the advantages of Custom Aluminium Extrusions?
✅ Complex cross-sectional parts
The main advantage of Aluminium extrusions is the ability to manufacture very complex cross-sections in varying lengths that are typically too difficult or impossible to produce via alternative manufacturing methods.
✅ Low to high-volume production
Once the die has been manufactured there is flexibility with order volume, both low and high volume extrusions can be produced economically. Uniquely, we have no Minimum Order Quantity for the amount of extrusion needed. Whether you need a mass production or simply a one-off custom extrusion, Get It Made has the capability and flexibility to deliver for your project.
✅ Tailor the mechanical performance
The strength of aluminium extrusions can be tailored by adjusting the wall thickness and internal structural profile of the extrusion. This means the strength can be concentrated precisely where it is needed without adding unnecessary extra material.
✅ Low-cost parts manufactured fast
Extruding is a very efficient process as parts can be manufactured continuously, making the cost per unit much lower compared to alternative manufacturing methods. Once the die has been manufactured, parts can be produced in a matter of days ready to be delivered, making extruding excellent for getting parts produced on demand.
✅ Excellent strength to weight ratio
Aluminium extrusions are lightweight (1/3 the weight of steel) and have a great strength to weight ratio. This makes them a popular choice for applications in the aerospace industry where weight reduction is a priority.
What are the disadvantages of Custom Aluminium Extrusions?
❌ Initial start-up costs
Although often not that high, there is an initial startup cost of manufacturing the extrusion die. However, this cost is quickly offset by the low cost of producing aluminium extrusions.
❌ Design constraints
Due to the nature of the extrusion process parts have to have a uniform cross-section. There are also some other design considerations that have to be taken into account, these will be covered in more depth in the Custom Aluminium Extrusion Design Guidelines section.
Custom Aluminium Extrusions design guidelines
In order to keep costs low and part quality high, engineers and designers should consider the design of their parts carefully, following the tips listed below.
Uniform wall thickness
Keeping the wall thickness consistent ensures a more efficient extrusion, as this will reduce production time and create a cost-efficient product. Varying thicknesses can be achieved but it will add time and complexity to the overall process. Although increasing part cost, by varying the wall thickness you can adjust the mechanical performance of your extrusion in specific locations. It is important to keep in mind that during cooling, variation in wall thickness will result in uneven part cooling, causing potential deformation.
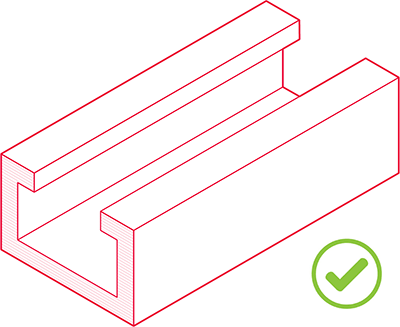
Geometry
When designing a part, try to use simple geometric patterns since the more complex a shape is, the more difficult it will be to force material through an extruder. Having symmetry in the design is also highly recommended, as this decreases peak die stress as the forces are evening distributed. Furthermore try to avoid cavities in your design as cavities significantly increase the die complexity, cost and lead time.
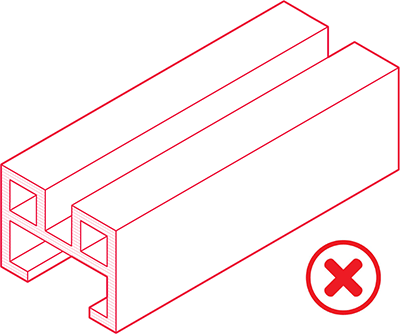
Corners
Adding radii to sharp corners simplifies the extrusion process, since sharp internal and external corners are very difficult to achieve, sometimes requiring additional machining. Corners without radii can slow down production and increase the risk of imperfections. In short, rounded corners will make it easier for the part to be extruded. We recommend adding a radius of 0.5mm to 1mm on all sharp corners.
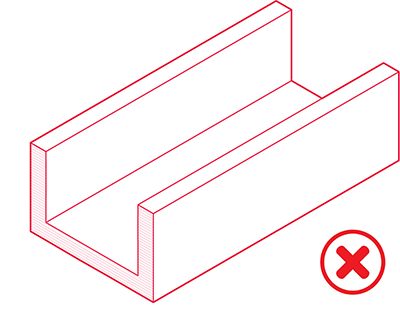
Occasionally, however, there are times when a corner interfaces with another part and you might therefore need a sharp corner. In these instances, we recommend adding a dogbone style corner, as shown in the image below on the right. This essentially removes a small circle of material from the corner to allow the mating part to interface correctly with the extrusion. We recommend a circle with a minimum radius of 0.5mm.
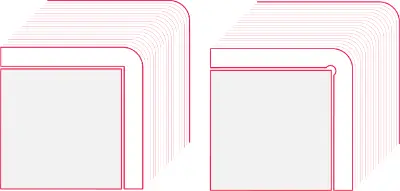
Features such as sharp tips should also be avoided. To generalise, extrusion manufacturers often refer to using soft lines (i.e. no sharp or excessively tight features).
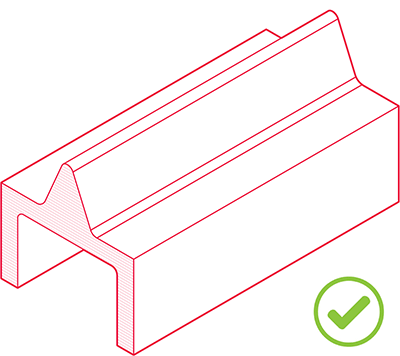
Channel ratios
With profiles that have channels (sometimes called pockets or tongues), a basic rule applies in which the ratio between the height and width of the channel should approximately be 3:1, to ensure the die strength is not compromised. The higher the channel ratio, the more difficult it will be to extrude the part.
When using large radii at the channel’s opening, and a complete radius at the base of the channel, an increased ratio of 2:1 can be adopted.
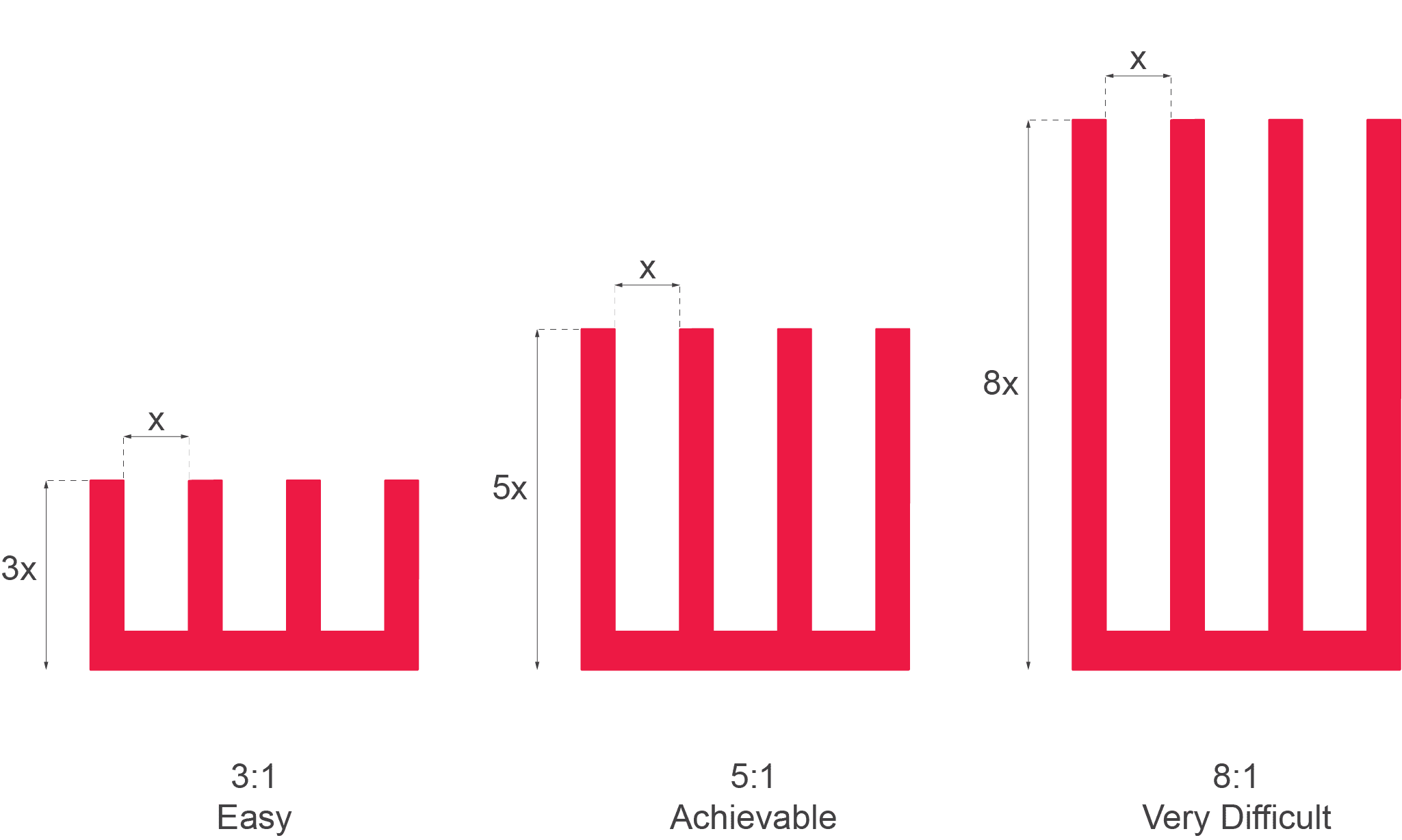
Minimum wall thickness
It is also critical to ensure the wall thickness is not too low. Insufficient wall thickness can cause issues during extrusion such as distortion, incomplete extrusion and increased tool wear.
The minimum wall thickness for aluminium extrusion depends on several factors, however, the most notable factors are the cross-sectional shape and size and the aluminium alloy chosen. The graph below indicates the recommended wall thicknesses for several common profiles based upon the circumscribing circle.
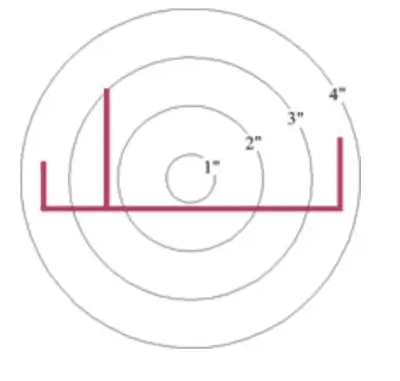
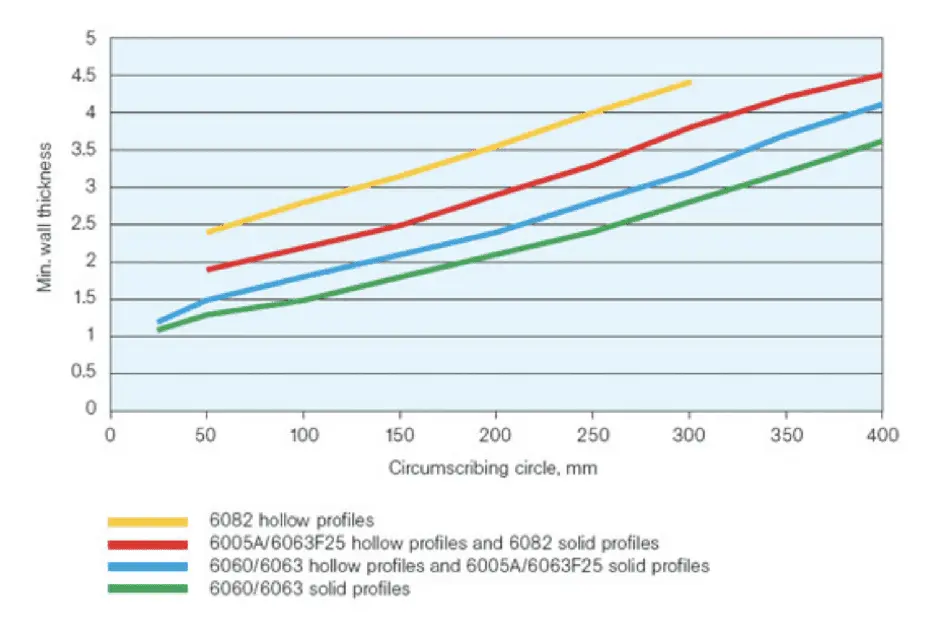
Visual surfaces
It is recommended to make essential visual surfaces known to the manufacturer, so the part can be created with minimal visual imperfections. Do also consider adding a pattern to these surfaces, as this has the advantage of hiding potential imperfections during the machining and handling of the part.
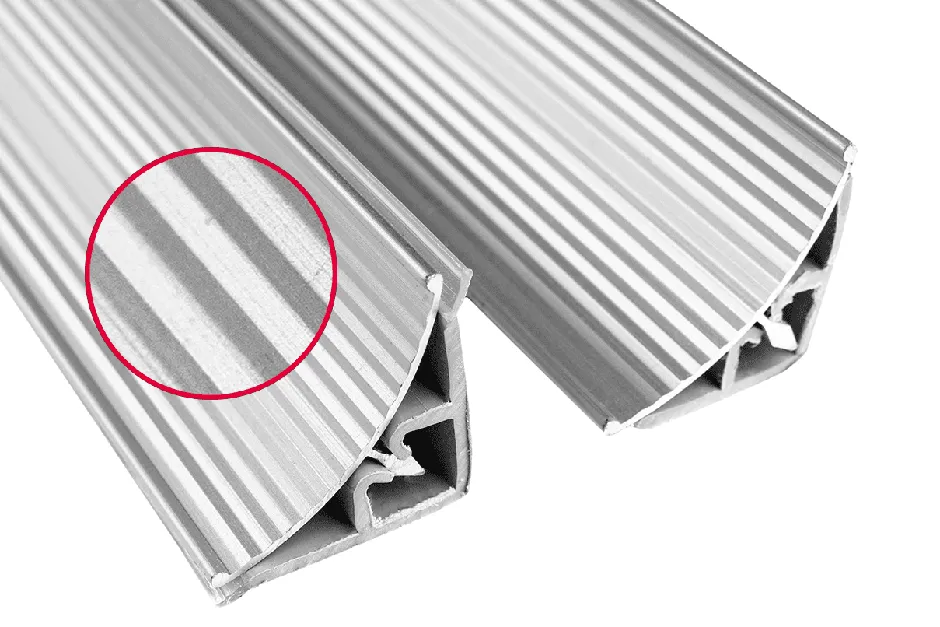
Aluminium Extrusion Grades
What grades of aluminium can be used for extrusion?
The common grades of aluminium used for extrusion at Get It Made are tabulated below. We recommend asking an experienced manufacturer such as ourselves if you are unsure as to the best grade for your project. Below we will compare a few different aluminium grades.
Al6063
This is the most popular aluminium extrusion grade, its fine grain structure allows for complex profiles to be extruded with a smooth surface suitable for anodising. It has good mechanical properties but parts requiring higher strength should use Al6082 or Al6061. It is typically used in architectural applications due to its ability to extrude intricate profiles. 6063A is a variation of 6063 with greater mechanical properties but still retains the smooth surface finish and anodising ability. This alloy is used in road transport, rail industry and more extreme sports equipment.
Al1050
This is a commercially pure grade and is popular in the electrical industry due to its excellent electrical conductivity, corrosion resistance and workability. Its moderate strength, high ductility and reflective finish make it a popular choice for manufacturing heat sinks. It can also be found in the food industry for containers due to its corrosion resistance properties.
Al6082
This is the highest strength 6000 series alloy with great corrosion resistance, often used for structural purposes. However, it is difficult to produce thin-walled, complex extrusions and leaves a less smooth surface finish compared to other 6000 series alloys. It is commonly used for high-stress applications such as bridges, trusses and cranes. This alloy should not be used for decorative extrusions.
Common defects with Aluminium Extrusions and how to avoid them
Warping
During the extrusion process, the aluminium billet is subject to tremendous forces and residual stresses can naturally develop. This can cause the parts to warp and is exacerbated if the part cools unevenly. Uneven part cooling is a result of inconsistent wall thickness and asymmetry within the design. Always ensure uniform wall thickness and symmetry within your design to reduce the risk of your extrusion warping.
Streaking
Streaking, sometimes known as 'die lines' are small continuous marks or grooves that run parallel to the direction of extrusion. These can be caused by changes in the metal flow during extrusion or poorly designed tooling. Streaking can be hard to control, however by using a ribbed/patterned surface, the appearance of streaking can be minimised.
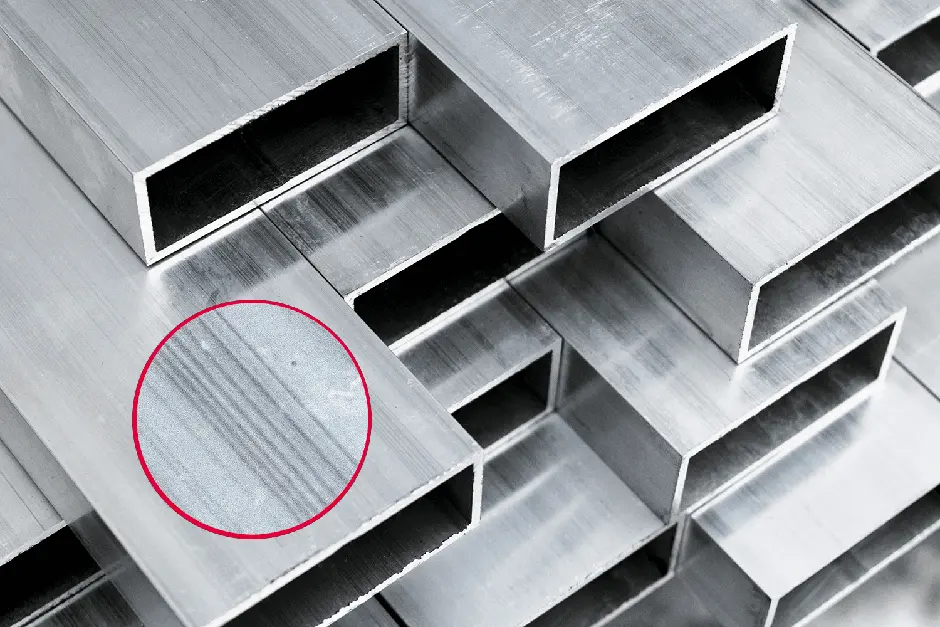
Cracking/Tearing
Cracks can occur in the extruded part if the extrusion settings and conditions are not correct. Cracks are formed due to excessive frictional stress between the metal and the tooling and typically form on the surface of the part. Cracks can occur due to the extrusion speed being too high or too variable, as well as the extrusion temperature being too high. Ensure you follow the aforementioned design guidelines and avoid features that could concentrate stress such as overly thin sections, overly high channel ratios. Make sure to also pick a reputable manufacturer such as Get It Made. With years of experience and strong attention to detail, we'll work with you to make sure your designs are best suited for aluminium extrusion.
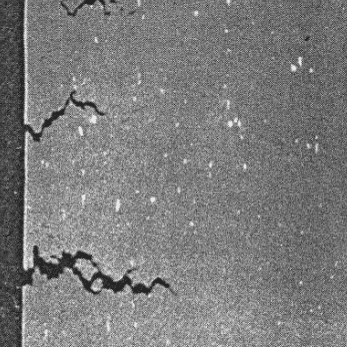
Blisters
Blisters can form when there is trapped air or other contaminants (such as lubricants) in the extrusion process. Once again, we recommend using a trustworthy reputable manufacturer to avoid such issues. By ensuring a high-quality material input and proper machine maintenance, blisters can be easily avoided in the aluminium extrusion process.
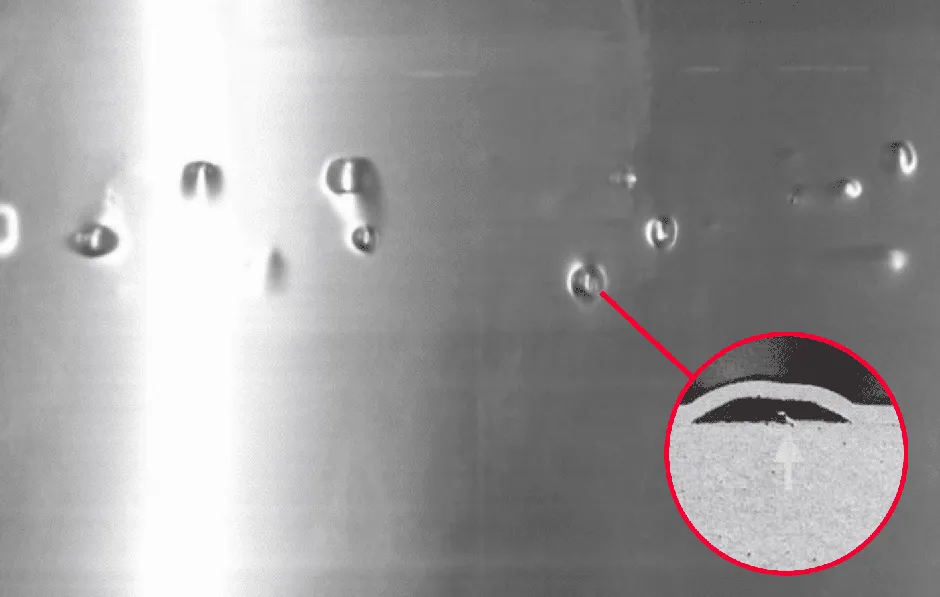
Cost reduction tips for Aluminium Extrusion
This section will outline some simple adjustments you can make to your designs to help reduce the overall part cost. There are three main areas that will significantly affect the cost of your part:
- Design - Complex parts result in increased machining time.
- Material - The cost of the bulk material and how easily it can be extruded.
- Quantity - Cost per unit reduces with an increase in quantity due to fixed setup costs.
Design
Uniform wall thickness
By keeping the wall thickness consistent the extrusion can be manufactured quickly with evening cooling, resulting in a more cost-efficient process. To further reduce machining costs, make sure to keep the minimum wall thickness above the suggested thickness highlight in the design guidelines above.
Simple profile
By having a simple extrusion profile you keep the manufacturing of the tool simple, the more complicated the tool, the more expensive. Despite solid extrusions using more material than hollow equivalents, often the die will be simpler and the profile easier to extrude. Making solid extrusions more economically viable in certain cases.
Add radii to sharp corners
By adding radii to the sharp corners in your extrusion profile you can reduce machining time, cost of your extrusions and likelihood imperfections. Consider using a dogbone style corner if you need to keep a square internal profile. Sharp corners are hard to extrude and can sometimes require post-processing to achieve.
3:1 Channel ratio
Try to keep close to the 3:1 ratio between the width and height of the channels in your extrusion profile. The greater the channel ratio the more difficult it will be to extrude the part, increasing machining time and cost.
Use standard holes
Standard holes sizes can be drilled quickly and accurately with drill bits. However, if you require a non-standardised hole CNC machining will need to be used, increasing the cost. It is also important to keep holes a suitable distance away from the edge of the part to avoid creating a problematic thin wall feature.
Tolerances
To manufacture holes, walls and threads to tight tolerances is an expensive process as it requires an iterative slow machining process, increasing machining time. Parts also require post-machining inspection using a micrometre or CMM, further adding to the cost. It is therefore advised to only add tolerances to critical features in your design. Soft materials or designs with thin features are tricky to machine to a tight tolerance due to the part/tool flexing/vibrating when machining.
Material
Two factors affect the cost of certain materials for extrusion, the raw material cost and the machinability. Raw material costs do fluctuate over time however we keep our material prices consistent so part costs remain fixed for repeated orders. Machinability refers to how easily the material can be machined/extruded. The better the machinability of material the quicker the machining time, resulting in reduced cost. 6000 series alloys are the most versatile and cheapest option for extrusions.
It is advised to select the lowest cost material that has the properties which meet your design requirements. If you are unsure about what material to select, submit a quote with us for a range of different materials to give you an idea of the price range.
Quantity
A larger overall length/quantity of aluminium extrusions will be benefit from economies of scale in terms of material and labour. Furthermore, by increasing the quantity, the fixed tooling costs can be absorbed across an increased number of parts.
Custom Aluminium Extrusion Cost Breakdown:
How much do custom aluminium extrusions cost?
Aluminium extrusion costs vary considerably based on the cross-sectional area, complexity, length and quantity of parts required. Aluminium extrusions costs can also be divided into two main categories: tooling costs and unit costs.
The best way to fully determine the costs of an aluminium extrusion project is to arrange a quote with a reputable company such as Get It Made.
Aluminium Extrusion Tooling Costs
Tooling costs include the cost of manufacturing of the steel die and is typically a fixed cost; independent of the number of parts required. Tooling costs often include the cost of designing the die itself which can be a time-consuming process. Tooling costs can vary depending on the circumscribing circle and features such as cavities and thin features can add complexity and increased costs.
Aluminium Extrusion Unit Costs
Unit costs involve the raw material and associated labour costs of producing the parts themselves. Unit costs may or may not include delivery and any taxes or duties if applicable. At Get It Made, our aluminium extrusion quotes typically include all costs, so there are no hidden surprises. Uniquely, we have no Minimum Order Quantity (MOQ) for the amount of extrusion needed. Whether you need a mass production or simply a one-off custom extrusion, Get It Made has the capability and flexibility to deliver for your project.
Bear in mind that the shipping costs for aluminium extrusion can be high due to the parts often being metres in length. Ask your manufacturer what is the most economical length they can ship and be prepared to use sea freight to reduce costs. For example at Get It Made, we recommend keeping the length of aluminium extrusion to 3m or less.
Getting Your Part Made
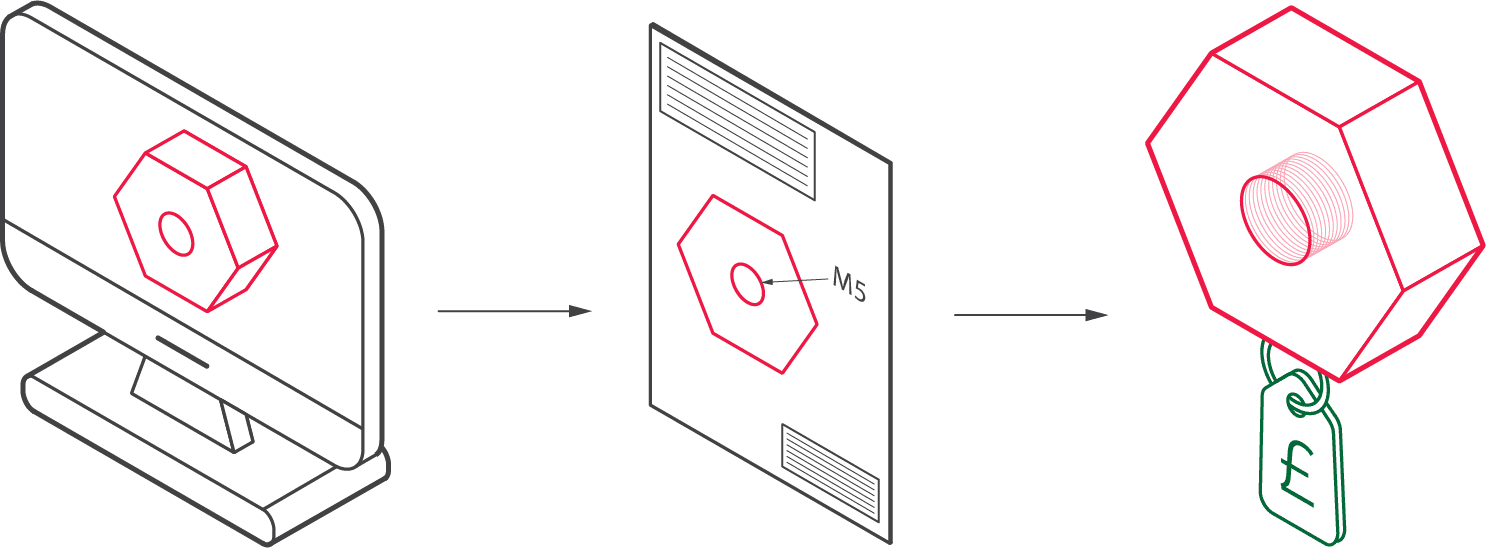
1) Design and export your CAD file
Use the Custom Aluminium Extrusions Design Guidelines to help design your parts ready for machining. Then please export your 3D CAD files to STEP, IGS or PARASOLID format. Unfortunately, we can only accept STL files for 3D printing projects. We cannot accept OBJ files as they do not correct geometric data for manufacturing.
2) Create an engineering drawing
We highly recommend sending a supporting PDF Engineering Drawings for each part. This is required when a part has: thread holes, critical dimensions, tolerances, specific finishing requirements. In some circumstances such as highlighting a threaded hole, we can accept an annotated screenshot. To understand learn how to specify threads, review our threads terminology page, and our metric thread chart.
3) Get a Quote in 24 hours
Request a free quote today and one of our engineers will personally review your project within 24 hours. They will then help fine-tune your project to make sure you get the best possible price and lead time for your custom aluminium extrusions!