What is Ultrasonic Welding?
Explore the intricacies of ultrasonic welding, its varied methods, compatible materials, advantages and disadvantages, and its significant applications across industries in this informative guide.
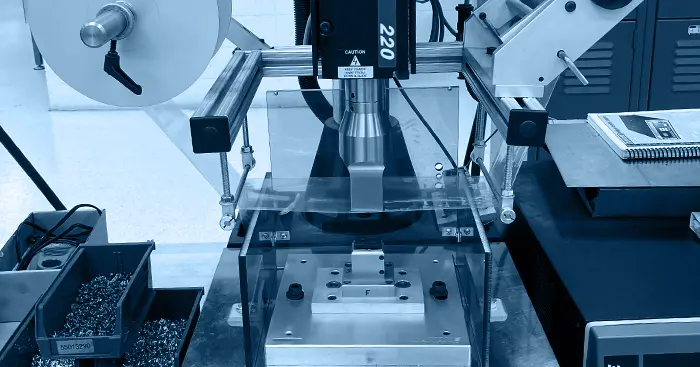
What is ultrasonic welding?
Ultrasonic welding works on the principle that two materials can be subjected to high-energy vibrations, generating frictional heat. The horn in the diagram is shaped to apply vibratory energy to selected joint areas. This heat plasticises the two workpieces, and when pressure is applied, the materials mix at the weld zone. When the vibrations stop, the combined material cools and solidifies to form a strong, homogenous bond. It is the cheapest and fastest plastic welding process, so engineers often favour it.
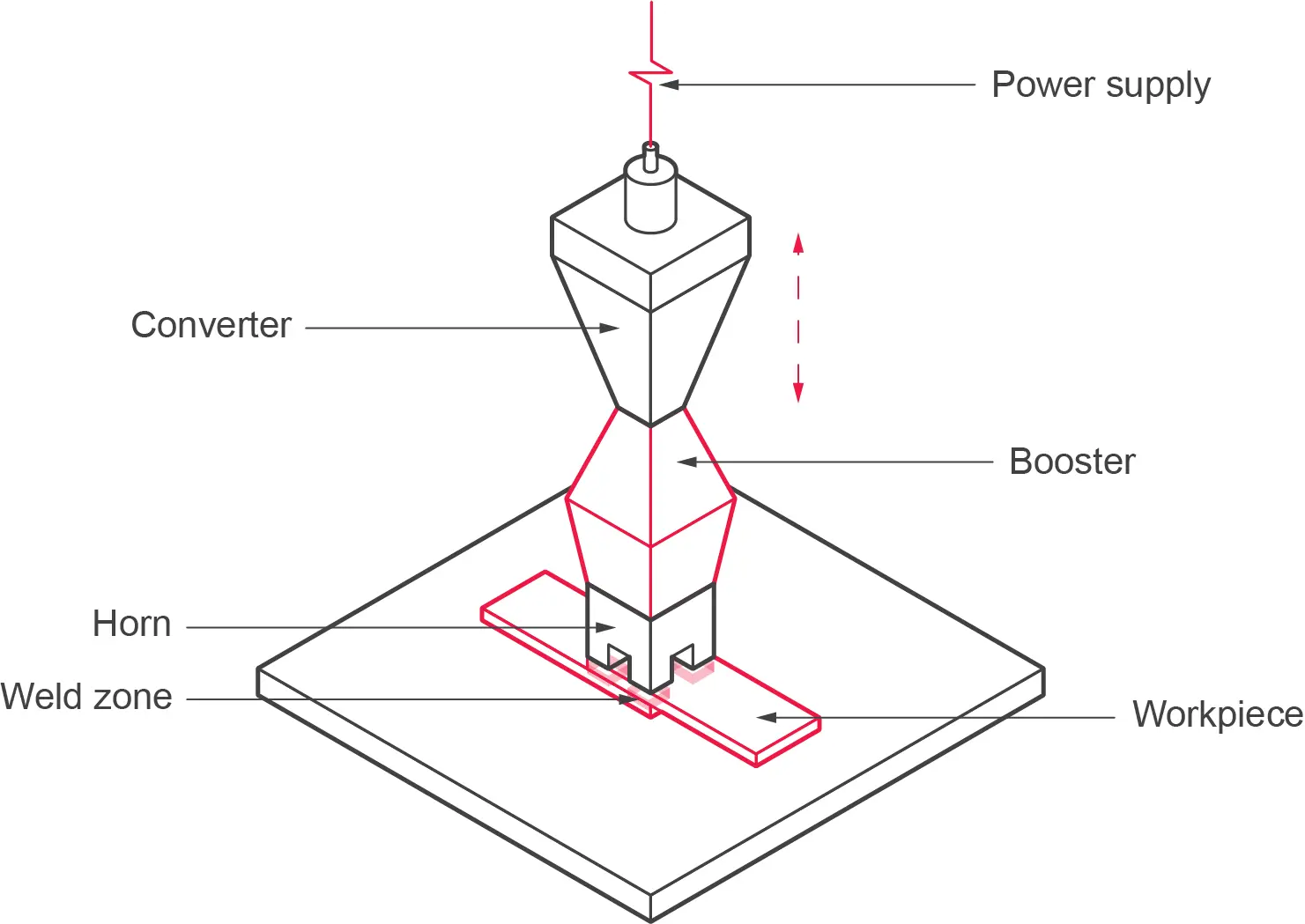
{{cta-banner}}
What is the ultrasonic welding process?
1) Initial assembly: Parts are secured within a specially designed fixture to ensure precise alignment during the welding process.
2) Engagement of horn: The horn interfaces with the upper part, exerting downward pressure towards the fixture with an electric press. This horn transmits the mechanical vibration to the parts.
3) Welding process: The horn initiates high-frequency vibrations (typically 20 kHz) that transmit mechanical energy to the components, generating heat at the interface and facilitating fusion.
4) Cooling phase: Post-welding, vibrations stop while the pressure is sustained, allowing the fused components to cool and form a durable bond.
5) Completion: Once the weld cools and solidifies, pressure is released and the horn retracted, freeing the newly welded component from the fixture.
Types of welds used in ultrasonic welding
Close Welding
Ultrasonic welding where the horn is positioned near (<6.35mm) the assembly joint. This approach is particularly suitable for welding materials with a low rigidity modulus, which can dampen vibrations shortly after they move away from the horn.
Distant Welding
Ultrasonic welding where the horn is placed further away from (>6.35mm) the assembly joint. It proves effective for welding materials with a high modulus of elasticity. These materials are capable of transmitting vibrations without significant dampening.
Inserting
Ultrasonic inserting is used to incorporate metal components, such as inserts, into pre-made holes in the moulding. This method offers several advantages, including high strength and speed, prevention of stress accumulation, and shortened moulding cycles.
Spot Welding
The ultrasonic spot welding process is effective for joining parts that don't have pre-existing holes or energy directors - it's beneficial when dealing with larger components.
Staking
Melting and reforming a post on the moulding to mechanically lock dissimilar materials in place - provides short cycles, good appearance & tight assemblies.
Compatible materials
All thermoplastics can be joined using ultrasonic welding. Many amorphous thermoplastics such as ABS, PMMA and PC can be joined to themselves and, in some cases, to one another. Semi-crystalline thermoplastics such as PA, POM and PP can only be joined to themselves. Many factors affect the ability of a material to weld to itself or another plastic. For example, a material has to be sufficiently stiff to transfer vibratory energy to the joint interface.Amorphous materials are more suited to energy-directing joint designs, whereas semi-crystalline materials are best welded with shear joints.
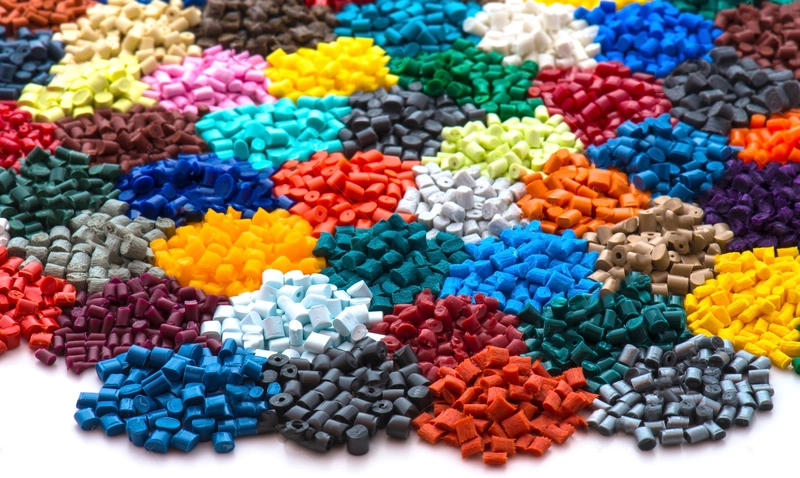
Below is a guide on the performance of some commonly used plastics for ultrasonic welding. Generally, materials with greater stiffness are simpler to weld, and those with higher melting temperatures require more energy. For different materials to be welded together, they must have similar molecular structures. Materials with a crystalline structure can only be welded to other crystalline materials.
Advantages of ultrasonic welding
✅ Speed
Ultrasonic welding is a fast process thanks to the high-frequency vibrations it uses. It takes just seconds to heat, weld, and cool materials.
✅ Safety
It's a much safer alternative to other welding techniques, with highly focused energy and minimal heat generation.
✅ Reliability
Once set up and tested, ultrasonic welding equipment is super dependable. Plus, it can be automated, making it even more reliable.
✅ Quality
It results in clean, precise joints without unwanted plastic flash or deformation.
✅ Cost-Effective
Ultrasonic welding doesn't use extra materials like bolts or adhesives, which cuts costs. Plus, it's highly accurate and automated, reducing waste and labour costs.
Disadvantages of ultrasonic welding
❌ Material Restrictions
While it works great on many thermoplastics, ultrasonic welding is only ideal for some materials, especially those with high moisture or tough plastics.
❌ Joint Limitations
Ultrasonic welding only works with certain types of joints, specifically lap joints. It's ineffective for corner, butt, tee, and edge joints.
❌ Lead Time
Setting up new ultrasonic welding operations takes time and effort. It requires custom tooling and multiple rounds of testing, adding to the lead time.
❌ Custom Tooling
Every new ultrasonic welding project requires custom tooling, which may challenge smaller companies.
❌ Investment Cost
Ultrasonic welding equipment is pricier than traditional welding gear, especially with automation.
Industries that use Ultrasonic Welding
Tech World
Automotive
Aerospace
Healthcare
Packaging
Summary of ultrasonic welding
Ultrasonic welding, a process where two materials are subjected to high-energy vibrations to generate frictional heat, is a popular plastic welding technique due to its speed and cost-effectiveness. Depending on material characteristics and application requirements, it uses methods like close welding, distant welding, inserting, spot welding, and staking. It is compatible with all thermoplastics, but the welding performance varies with different materials. While it offers benefits like speed and reliability. Limitations include restrictions on material types, size and the need for custom tooling. Despite its limitations, ultrasonic welding's versatility and efficiency make it a valuable technique in modern manufacturing.
Ready to see how much your part costs to manufacture? Start with CNC machining or 3D printing to manufacture your parts, and Get It Made will help guide you with how to ultrasonic weld them together.
Feel free to request a free quote today, and one of our engineers will review your project within 24 hours.
We have a dedicated technical toolbox if you want to learn more about the services we offer.