Cost Reduction Tips for CNC Machining
An overview on the factors that contribute to the cost of CNC machined parts, and how to reduce them.
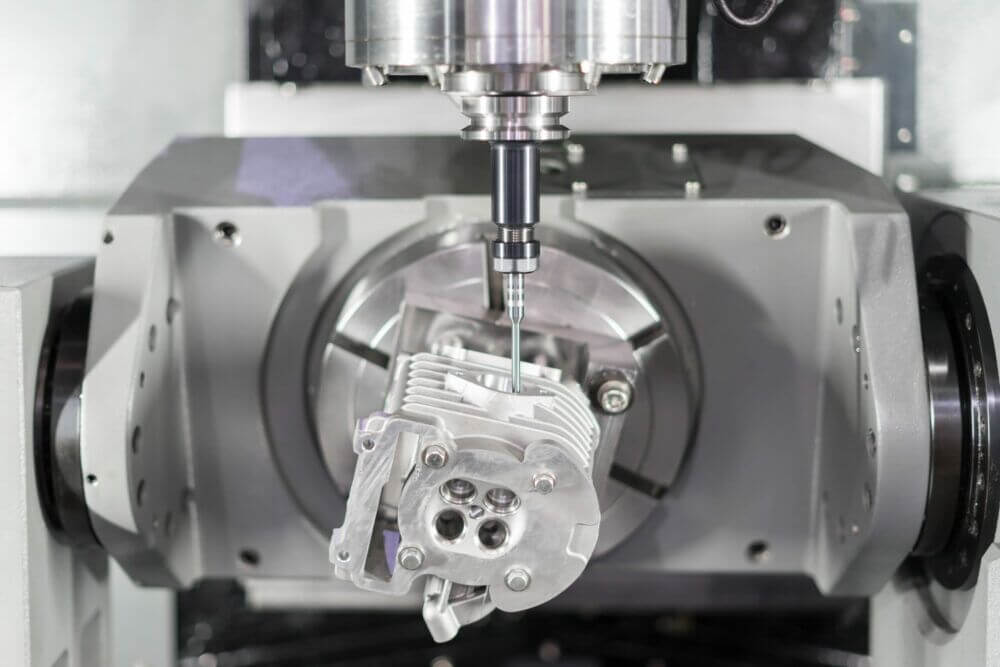
How much does CNC machining cost?
The costs of CNC machining are highly dependent on several factors:
- Machining time
- Cost of bulk material
- Part design and specific requirements, such as finishes, machine set-ups, and specific tools
- Tolerance allowance
Typically, you can expect to pay anywhere between £100 - £2000. Get a quote for your project here.
{{cta-banner}}
Factors affecting the cost of CNC machining
The cost factors include considerations such as which tools are used and how many machine set-ups are needed, and the overall quality and finish of the designed part. Overall machining costs will likely vary between industries requiring greater accuracy and precision. Due to tighter tolerances, the aerospace and medical industries will likely incur higher charges for CNC machined parts. Take a closer look below at ways to reduce the costs of CNC machined parts.
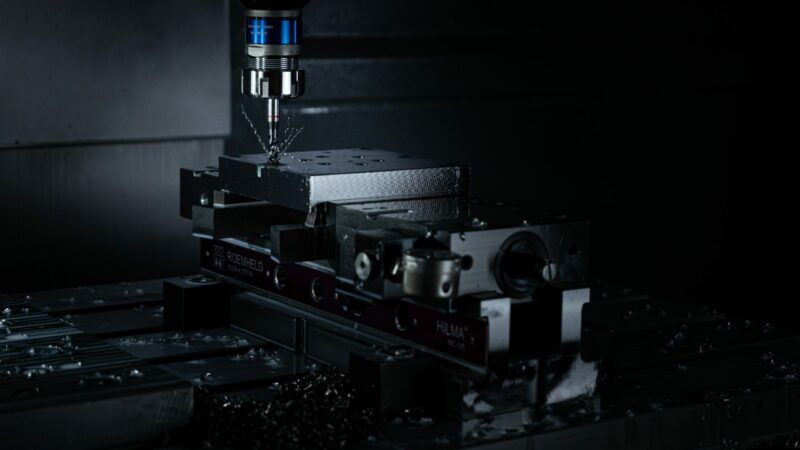
How to reduce CNC machine costs
💰 Volume of production
Due to its ability to manufacture small and large quantities of parts over a sustained period with minimal supervision when automated, CNC machining represents a cost-effective manufacturing method. However, if only one prototype is required, or a small volume of production, the cost of CNC machining can be increased due to the high initial set-up time.
💰 Materials used
Selecting an appropriate material from which your desired part can be manufactured is also an avenue in which cost-saving measures can be implemented. Different materials cost different amounts, and as such, it is crucial that you choose a material that will carry out the desired function of your product, meanwhile not overspending on a material with unnecessary properties. The greater the volume of material required to complete your project, the greater your spending will be. Therefore, parts must be designed to make efficient use of material.
💰 Product finish
The smoother the surface finish of a manufactured product, the greater the process required to achieve it, and therefore the greater the cost. As a result, it should be avoided if it is not essential that the manufactured product possesses a high-quality surface finish, such as a low Ra value. Instead, selecting a higher Ra value represents an opportunity to reduce CNC machine costs.
💰 No engraving
Due to the detail required to accurately engrave text onto the surface of a manufactured part, excluding additional features such as engraved and/or embossed text is another way to reduce costs. Similar to the principles of the product finish of manufactured parts, if an engraving process is not of critical importance to the manufactured product, it should be excluded from the CNC machining process to lower costs. Often laser etching can be an economical way of adding part numbers or logos.
💰 Complex geometries are expensive
Parts with geometric complexities come at an increased cost as they often require more expensive multi-axis CNC machinery or manual repositioning of the part.
Optimise material choices
The materials you use influence the cost of CNC machined parts. Factors affecting the material cost will include the machinability of the material and the initial cost of the bulk material in its raw form. This is because a significant factor affecting the price of CNC machining is material run time and labour costs. The reduced machine running time due to more machinable materials results in fewer costs overall. Softer materials are easier to cut and take less time to machine. They can also be cut using less expensive tools. The main cost of using a particular material is the bulk material price.
It is advised to select the lowest cost material with the properties that meet your design requirements. If you are unsure about what material to choose, submit a quote with us for a range of different materials to give you an idea of the price range.
Below is a graphic showing the range of costs for some common materials and plastics used in CNC machining.
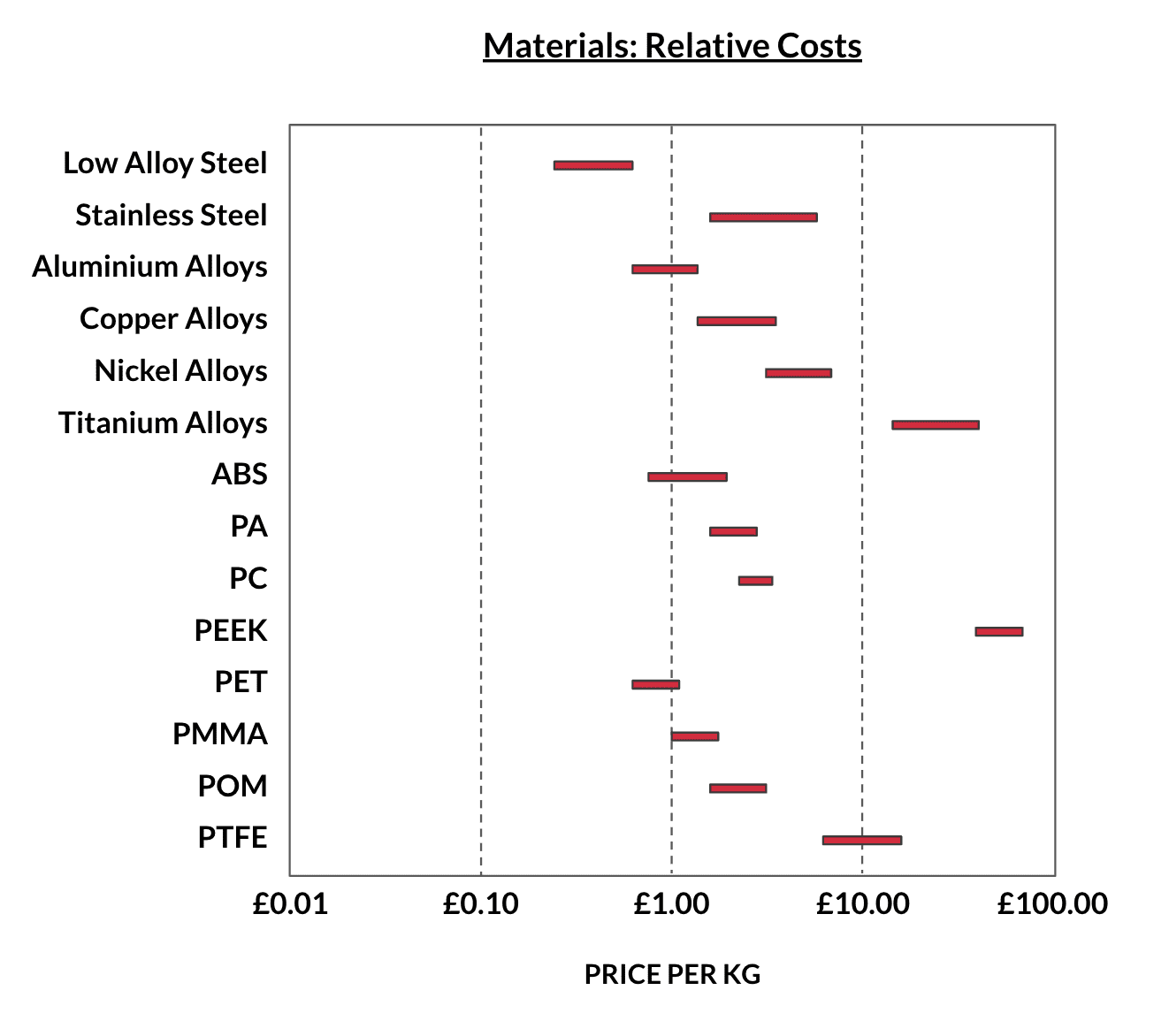
Quantity
Without any design changes, the cost of your part can be reduced significantly by just increasing the order size. Our engineers have to perform the part set-up, programming and tool choice, which is a fixed cost. The fixed price can be shared by manufacturing multiple parts simultaneously, making each part more economical.
Finishes
The finishes you use and have will also impact CNC machine costs. Usually, when a part is machined, traces or scratches can sometimes be left on the part's surface. Specialised finishes such as heat treatments, specialised treatments, and surface types are all part of the processing steps. Multiple surface finishes can add extra costs, so only add these if they are essential. Bead blasting, anodising and powder coating can increase costs, so this is an easy way to reduce prices if they can be avoided.
Avoid complex part geometry
Part dimensions, size and complexity, will all have a considerable impact on cost - larger parts consume more material usually, as these highly detailed parts need multiple processes to complete and may also require multiple machines. You can make complex CNC machined parts less expensive by designing them so that fewer tools and fewer machines are needed for the job. For example, specific measurements and features could be adjusted to meet the requirements of a cheaper component, or altered so that fewer machines are needed to finish the job.
Reduce designs with thin walls
Thinner walls are, surprisingly, more cost inducing than thicker walls in CNC Machining. This is because thin walls can distort because the thinner material will naturally be weaker and prone to vibrations. This can cause chatter, which slows down the machine speeds, resulting in additional costs and machine operator time. Multiple passes at low cutting depths for thin walls, machining these more accurately can always be a problem.
By expanding thin walls, to a more manageable minimum width, walls will be sturdier and tolerate faster machine processes.
Top tip: If you need thin walls, consider alternative machining methods, such as sheet metal fabrication.
Minimise tight tolerances
Tighter tolerances naturally give less leeway when it comes to producing a part, meaning that there can often be more excess material wastage and slower machine times to meet the accuracy requirements of the component. Where possible, increase tolerances as this can speed up machining time and result in less material wastage, too. Of course, this won’t be possible in some instances, but if, for example, a part can work with a tolerance of +- 1mm as opposed to 0.1 mm, you will be saving yourself more cost impacts overall.
Use standard hole sizes
By using standardised hole sizes throughout the design, you can significantly reduce costs as you won’t require a specialist tool to cut the part in question. Standard drill hole sizes mean less intervention is needed in the machining process. Non-standard hole sizes to use end mill tools, which can incur higher costs and slow down the process. Standard hole sizes will mean standard drill bits can complete the job, generally speeding things up.
Avoid adding text or logos
Adding additional features such as text or logos can also incur more significant costs. A ball end mill is used to trace numbers, letters and symbols for the CAD model, and the use of an additional tool, plus set up time to machine this piece, will mean increased running time overall.
Keep the number of machine set-ups to a minimum
If possible, mass-produce parts to drive down costs, as smaller quantities mean a large percentage of start-up costs is taken up. Larger quantities will affect the unit price, meaning these overhead costs can be almost eliminated because the cost is spread over many parts.
For more information about CNC machining, or our CNC machining services, please explore our site today or request a free 24-hour quote.