Choosing the Right Injection Moulding Material
How do you choose the right material for your injection moulding project? Learn more in our latest blog post!
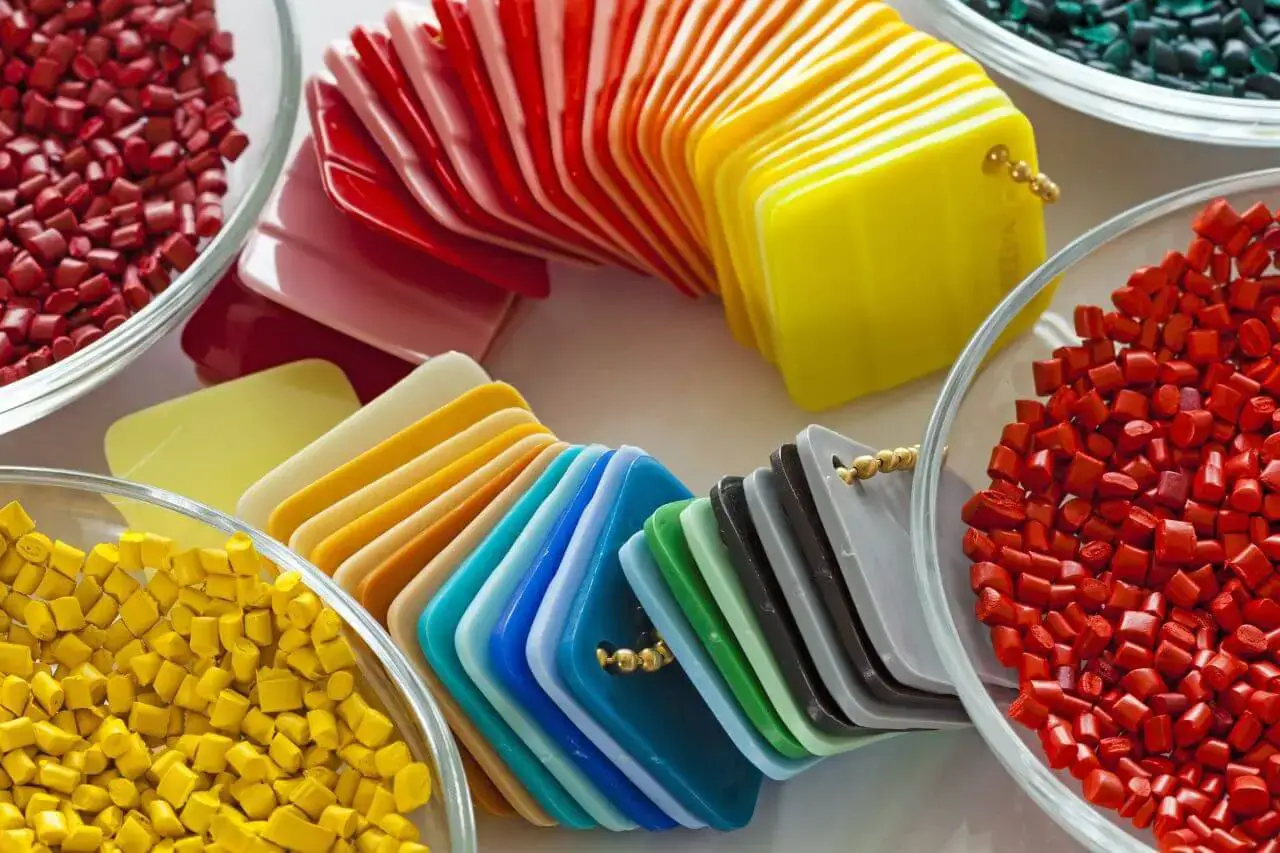
Injection Moulding is an extremely popular manufacturing process whereby primarily plastic products are mass-produced. Injection Moulding is used to mass-produce parts due to its high levels of accuracy, affordable unit costs and short lead times. The process of injection moulding involves molten polymer being injected into a mould with speed and precision, cooling quickly forming into the shape of the mould.
Many everyday objects are created using injection moulding or CNC machining – from handheld consumer objects to aerospace and medical equipment and machinery parts. Understanding the best type of material to use for your injection moulding project is essential.
Plastic injection moulding products are used every day by society in various industries. With up to 85,000 different polymers and finishes to select from, there are many options to consider, such as budget, design, product application, chemical composition and mechanical properties, to name a few.
Get It Made has comprised a list of the main factors to consider when considering which material to use for your plastic injection moulding project. By considering the whole composition of the plastic, design engineers and businesses can ensure the suitable material is used for their project.
Generally speaking, deciding on the suitable material to use for your injection moulding project can be determined by considering the following material properties:
- Hardness
- Flexibility
- Weight
- Cost
Other considerations to bear in mind when deciding which material to injection mould include environmental conditions of the final product (including temperature, UV and flame resistance), aesthetic requirements and ergonomic requirements. All of these factors will need to be considered when selecting a plastic to injection mould, to ensure it is of the correct weight, flexibility and hardness to deal with the requirements of the end-user/end product.
Below, we will take a deeper look into the four properties of popular injection moulding plastics, how these are determined, and examples of suitable plastics.
{{cta-banner}}
Hardness
Material's hardness is categorised by its resistance to pressure and indentation. An indenting device is used to measure ‘Shore’ hardness, of which there are two categories, type A and type D. Shore A refers to softer plastics whilst Shore D refers to harder plastics, with each category having a scale from 0 to 100 to further measure the hardness of the material in question.
Did you know: The Shore hardness is derived from Albert Shore, who developed the durometer scale to measure material hardness.
Flexibility / Stiffness
Material flexibility is another crucial factor to consider. There is a common misconception that all soft materials are flexible and that all hard materials are stiff. However, there is a difference between softness and flexibility when it comes to materials used in mass production. A material’s flexibility refers to its ability to bend under stress without breaking easily.
Cost
Cost is a significant factor in determining which material to use for your injection moulding project. It is a crucial decision to make, as it also requires consideration of the product application. Sometimes cheaper options lead to costly failures further down the line, whereas choosing a more expensive material upfront can prove worthwhile in the long run.
Weight
Weight is the fourth and final consideration when choosing an injection moulding material. This is because the density of the polymer will determine not only the weight of the moulded part, but also the weight of the end product. Often injected moulded parts are used in lightweight consumer products, and weight can be a determining factor.
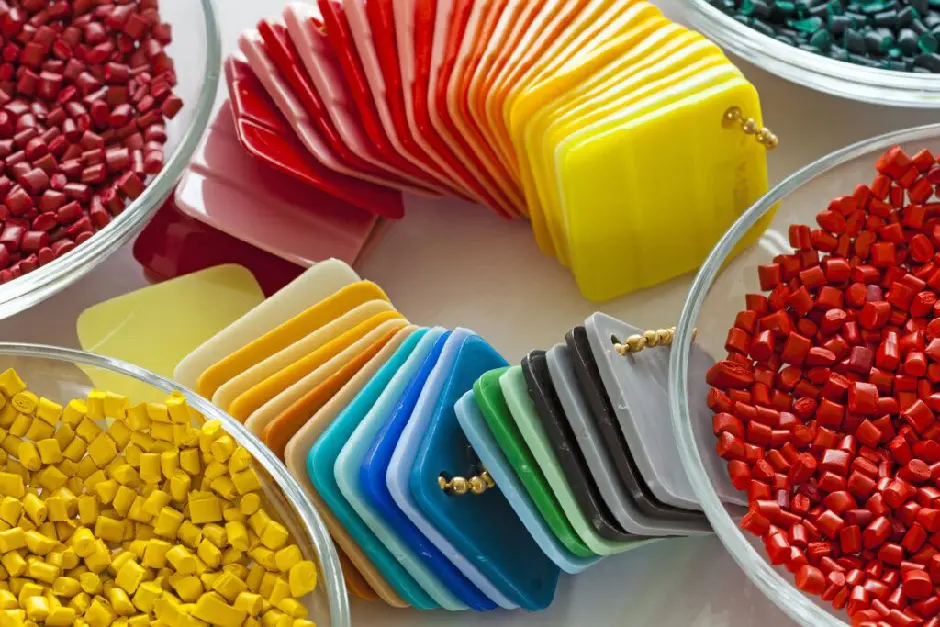
What materials can be Injection Moulded?
Below, we look at some of the more popular plastics commonly used in injection moulding.
ABS - Acrylonitrile Butadiene Styrene
ABS is tough and impact-resistant plastic. Because of this, it is widely used across several industries. It is suitable for handheld consumer devices with good resistance to acids and high dimensional stability, such as remote controls, phones, computers, and cosmetic parts. ABS also offers low shrinkage qualities, making it a popular choice for everyday products.
When it comes to finishing quality, ABS products can occasionally have sink marks, which can be eradicated if the material is blended with PC.
PC - Polycarbonate
PC is a strong polymer that is impact resistant with a low shrink rate and good heat resistance. This makes it a popular choice for indoor and outdoor lighting, automotive components, plastic eyewear, medical devices and protective gear.
PA - Polyamide
There are many different types of PA or nylons; their properties include high strength and high-temperature resistance. When reinforced, these properties are enhanced further. PAs are resistant to a range of chemicals, with some grades offering greater hardness and stiffness than others. PA has a low coefficient of friction, meaning PA is a good material for products such as screws, gears and parts in mechanical assemblies.
POM - Polyoxymethylene
POM has properties of high toughness, stiffness, hardness and strength. It also has lubricity, making it resistant to hydrocarbons and organic solvents. POM is favoured for some products due to its good elasticity, meaning it works well for bearings, gears, buttons, knobs, switches and electrical components. POM also offers abrasion resistance and good electrical installation.
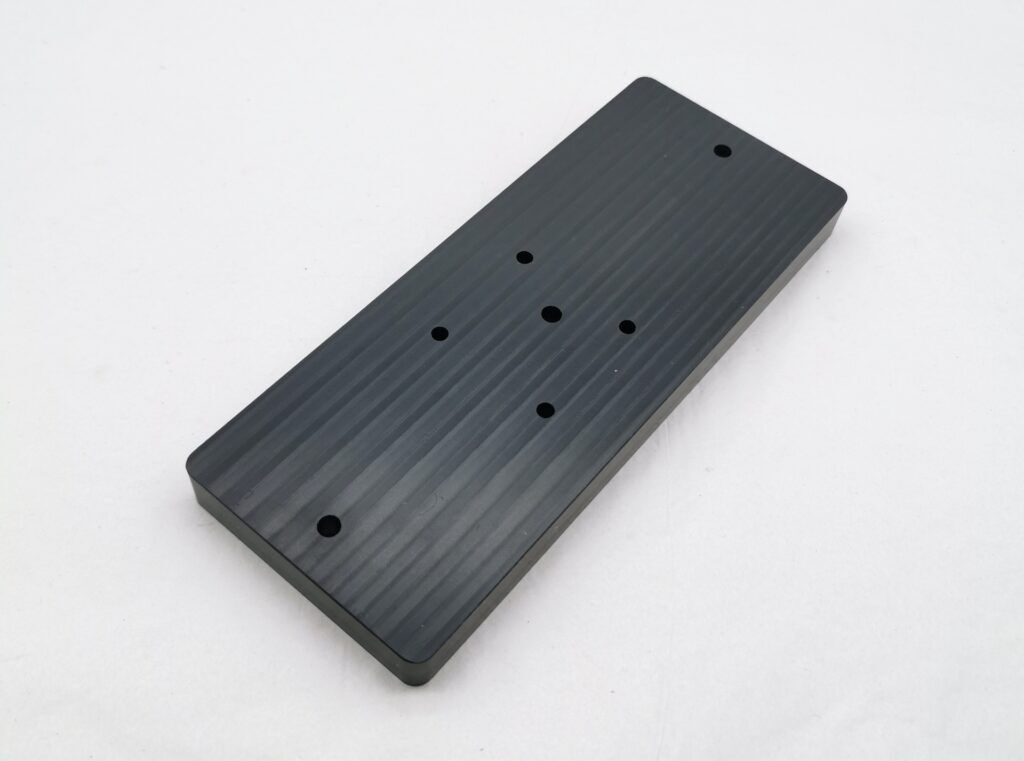
PMMA - Polymethyl Methacrylate
This polymer has good optical properties, with a high gloss, scratch-resistant finish, meaning it is favoured for lenses, optical fibres, car light housings and reflectors. It also possesses low shrinkage properties. However, it is brittle, meaning it is more susceptible to stress cracking. PC is a good alternative for some designs that delivers a similar finish. PMMA is transparent in its final form.
PP - Polypropylene
Polypropylene is an inexpensive resin option with high impact resistance. However, it can be brittle in colder temperatures. Despite this, it is water-resistant, flexible, and resistant to acids. Another unique characteristic of PP is its ability to be bent frequently without breaking, meaning it is widely used for living hinges – these are thin pieces of plastic used commonly for the lids of popular consumer items such as bottles of shampoo or sauce bottles. This uniquely adept polymer is also a suitable replacement for POM for low friction applications due to its relatively slippery surface. Additionally, its low density means there are weight savings for the manufacturer, making it a cost-efficient choice. Aside from consumer items mentioned previously, this thermoplastic is also used for dishwasher safe plates, Tupperware containers, cling film, sandwich bags and yoghurt pots.
PBT - Polybutylene Terephthalate
PBT has good insulating properties, which is ideal for electrical components. It is also a good polymer to use for automotive applications. PBT offers good resistance to fuels, oils, and solvents with moderate to high strength. Furthermore, it does not absorb flavours, meaning it is a good choice for coffee makers and toasters. Its high resistance to heat also makes it a popular choice for hairdryers, electric cookers and vacuum cleaners.
PPSU - Polyphenylsulfone
This rigid and tough thermoplastic is often used for high-end products due to its excellent mechanical qualities. PPSU possesses dielectric (insulative) characteristics, and with a high operating temperature, PPSU is a dimensionally stable material. It also offers resistance to radiation and acids. This makes PPSU a popular choice for medical components, sterilisation trays, automotive fuses, aircraft interiors, automotive parts, hot water fittings and electrical sockets. However, PPSU is sensitive to voids and bubbles caused by thicker sections in part geometries. Hydrocarbons can also weaken PPSU.
PEEK - Polyether Ether Ketone
This expensive high-end polymer thermoplastic offers high-temperature resistance and is a high-performance resin. It is widely used for medical parts aerospace fixtures and is popular with the automotive industry. PEEK is a flame retardant with excellent strength, chemical resistance and dimensional stability. It has the highest heat resistance of any polymer at 260 degrees C and has a melting point of 341 degrees Celsius. It is shock-resistant, resistant to bending and chemicals and has proven challenging to discolour or break. It is also radiation resistant and complies with various industry standards, including food, medical and the aerospace industry.
For more information about injection moulding, head to Get It Made’s technical toolbox. Enquire about our injection moulding services or request a quote, and one of our team will get back to you as soon as possible.