How to Machine Square Corners with CNC Milling
Designing parts with square corners is a common CNC machining pitfall. Check out some great design solutions below.
.jpg)
CNC Machining is a crucial manufacturing method for the production of a wide variety of high precision parts. All manufacturing methods have certain limitations regarding what features can and can’t be produced. This guide looks at the limitations of machining inside square corners and the different options available to engineers and product designers.
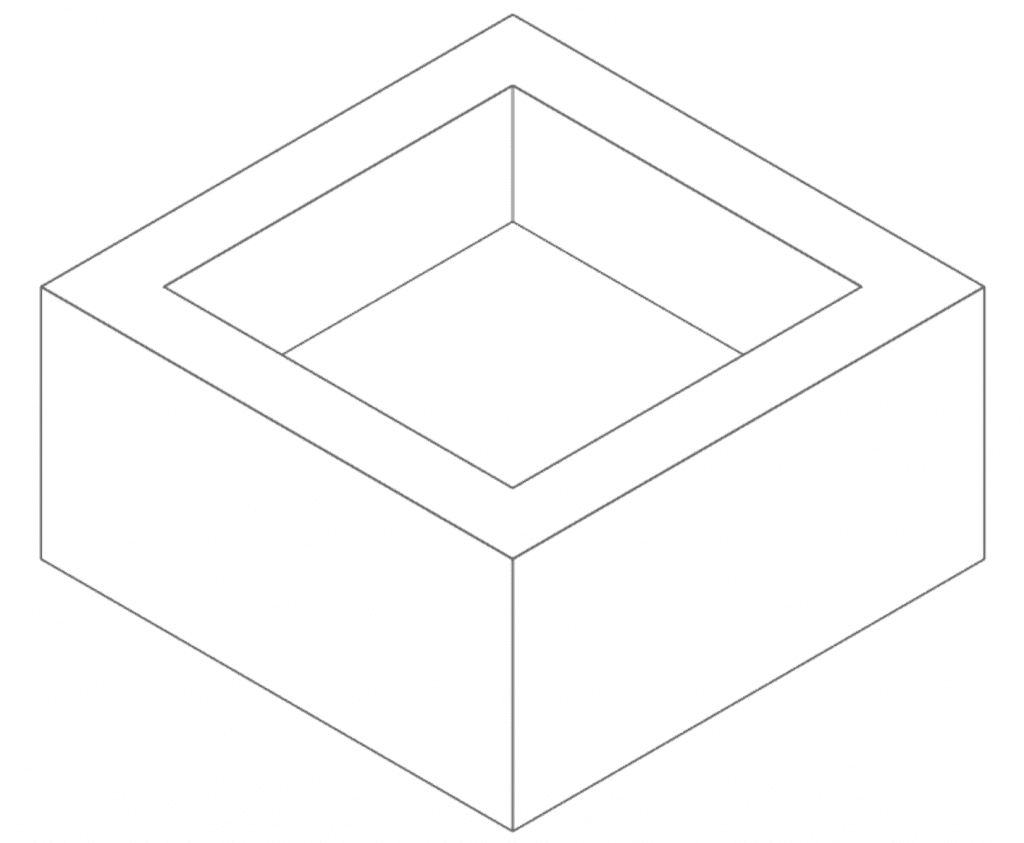
What is CNC Machining?
CNC (Computer Numerical Control) Machining involves a rotating circular cutter removing material from a workpiece in a subtractive process. The cutter’s path is determined by a CNC program that uses CAD data from a 2D or 3D file.
Top Tip: You can read up on Get It Made’s processes of CNC Milling & Machining here.
{{cta-banner}}
Can rectangular shapes be cut by a milling machine?
The short answer is no; a conventional CNC machining process cannot cut rectangular cavities. However, there are ways to redesign your part to resolve this problem. First, we need to fully understand the ‘Inside Corner’ problem before looking at ways to machine square corners.
Understanding the ‘Inside Corner’ problem
As previously mentioned, cutters used in CNC Machining have a circular cross-section. The cutting tool must also rotate to provide the cutting mechanism. These combined make it impossible for a circular cutter to create a perfectly square inside corner.
It is essential to distinguish between internal and external corners. Square corners can easily be created on external corners. This is because the cutting tool can access all aspects of the corner, as illustrated below.
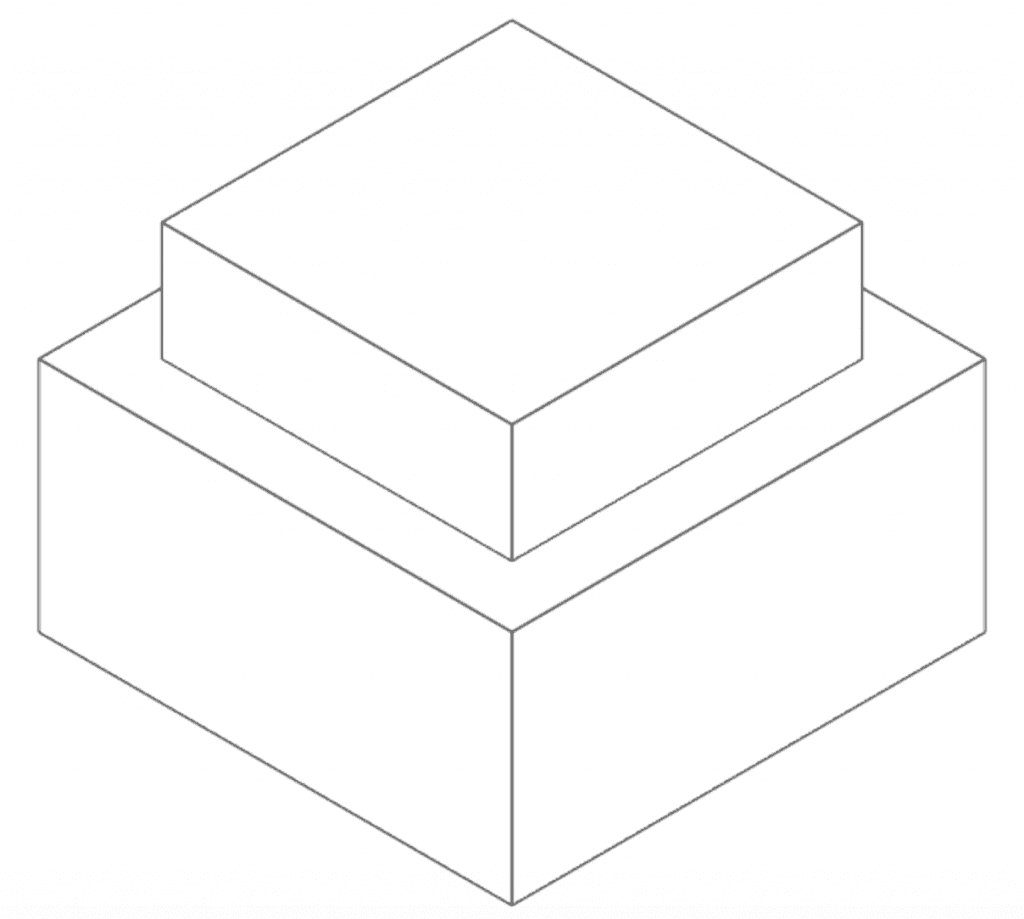
However, square internal corners are impossible to create, as the path taken by the cutter will leave a certain amount of the corner inaccessible. The radius of the cutting tool determines this amount.
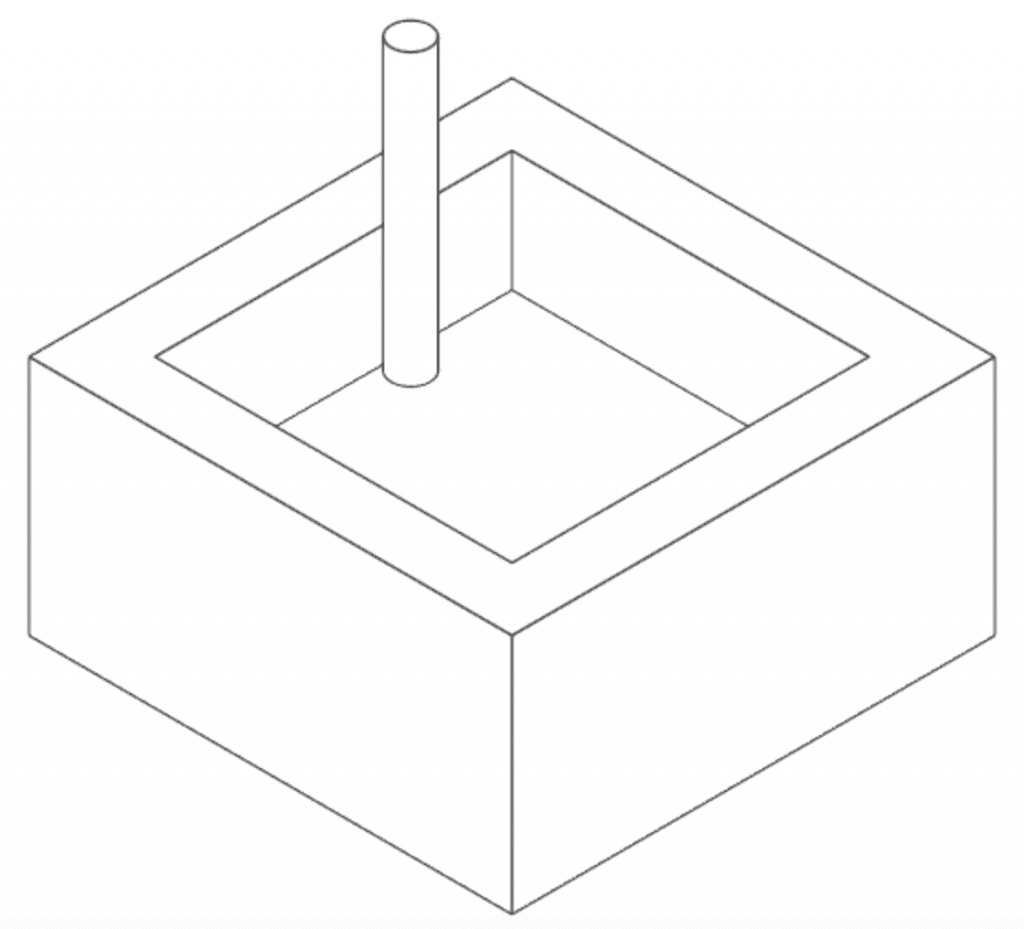
There are several reasons why a rounded corner might be a problem for a part. Let’s imagine this corner is part of a larger assembly; if another part mates or interfaces with this corner, it may be vital that the corner is perfectly square.
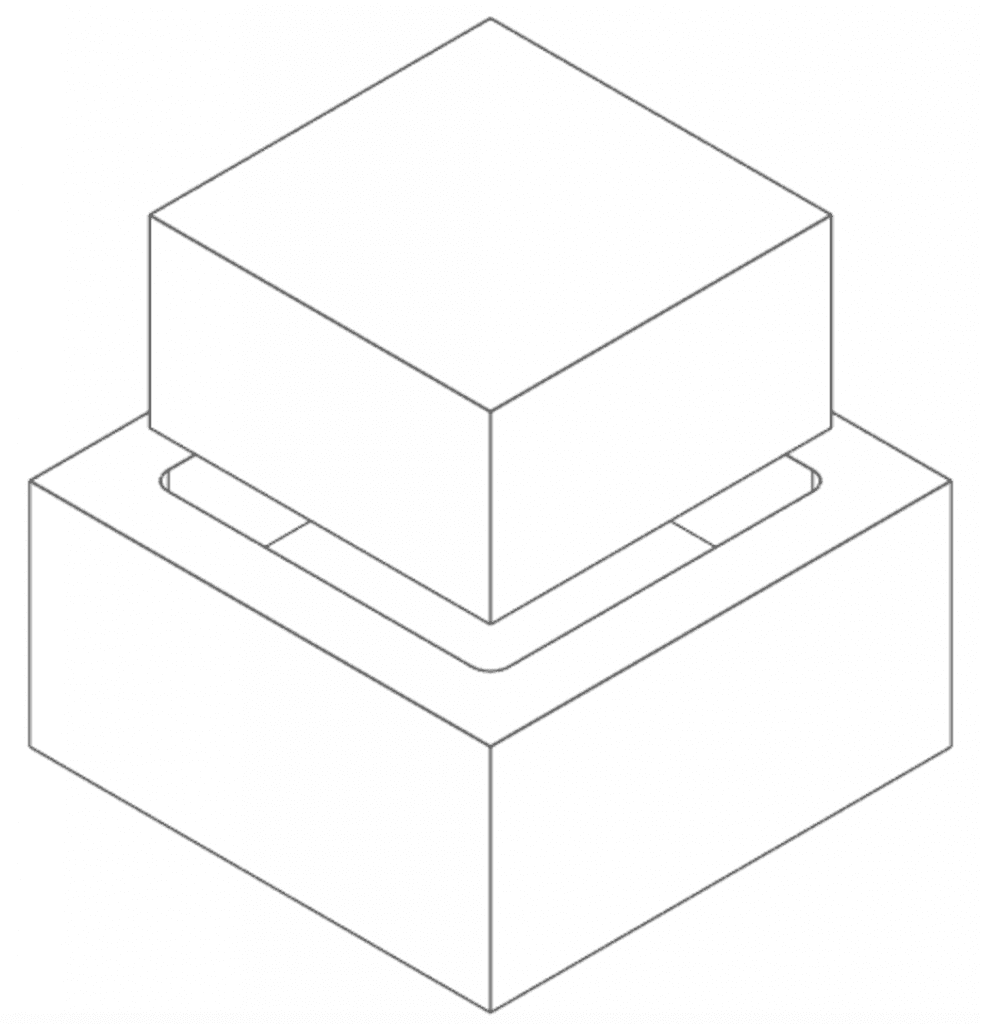
All inside square corners should be removed before starting production. Fortunately, there are several ways to redesign your CNC Machined parts to improve machinability. Your chosen method will depend on the use case for the part.
Adding radiused corners (fillets)
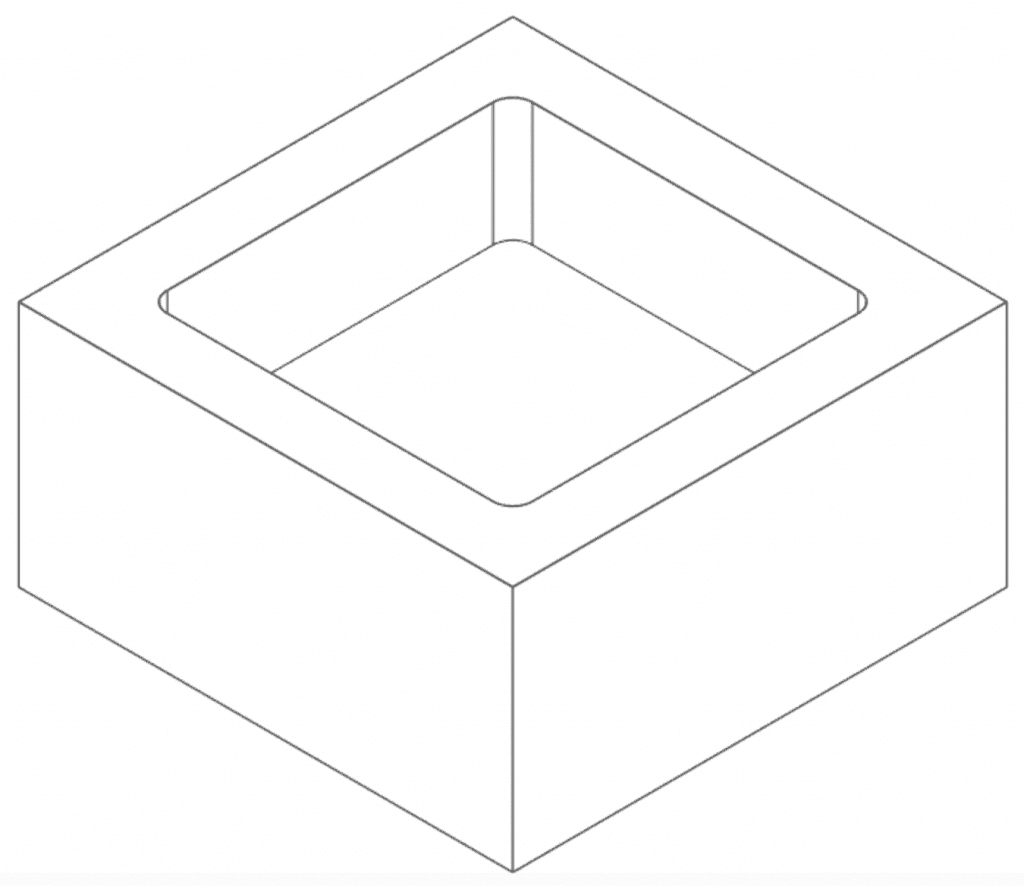
The simplest way to resolve the ‘Inside Corner’ problem is to add a radiused corner (also known as a fillet). If the corner does not interface with other parts, this is the best option.
The size of the cutting tool often determines the size of the fillet. However, try to use the largest radius possible to reduce costs where possible. This is because machining time is partly determined by the size of the cutting tool. A smaller cutting tool requires the CNC milling machine to run at a slower speed, therefore taking longer to remove material. Also, if the milled pocket is deep, a larger, more robust cutting tool will need to be used. This means a larger radius would be required. A rule of thumb is to keep the corner radius greater than ⅓ cavity depth.
At Get It Made, our typical minimum fillet radius is 1.5 mm. It is, however, possible to reduce this if necessary for specific materials. We can use a smaller 1 mm diameter cutter to produce a radius of 0.5 mm, but it increases costs and isn’t always possible for every design.
Now consider there is a mating part that is square and needs to fit into a pocket on your part. In this case, dogbones can provide an optimal solution.
What is a “dogbone”?
Simply put, a dogbone is an expanded or ‘overshot’ cut in a part. A dogbone allows for the area occupied by a square corner to be fully machined. It can be thought of as pushing the cutter further into the part than required.
T-bone
A simple dogbone extends the corner in a single direction; this is referred to as a ‘T-bone’ corner. The dogbone should be ‘pushed into the part’ by at least the radius of the circle. There is, however, no requirement to go further than one radius.
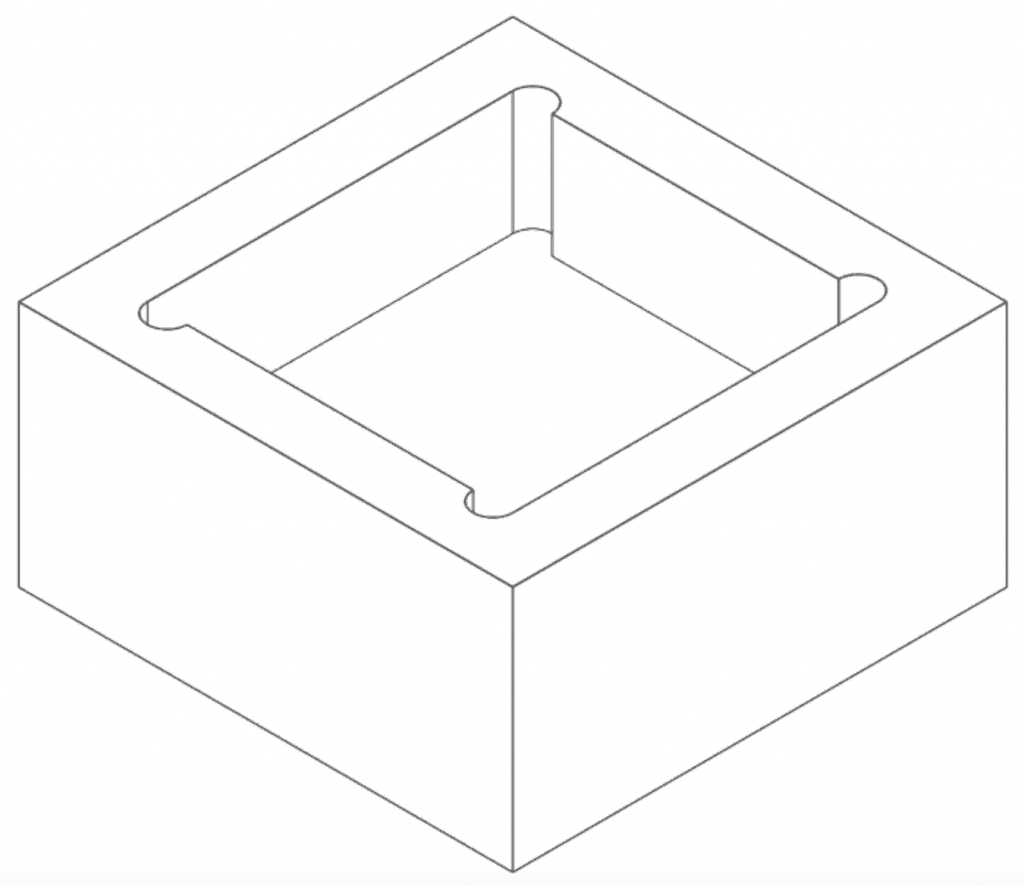
Two directional dogbone
Another option is to extend the corner in two directions. Some designers opt to place the centre of the circle directly on the corner itself. This is a simple and acceptable solution; however, it does remove more material than is necessary.
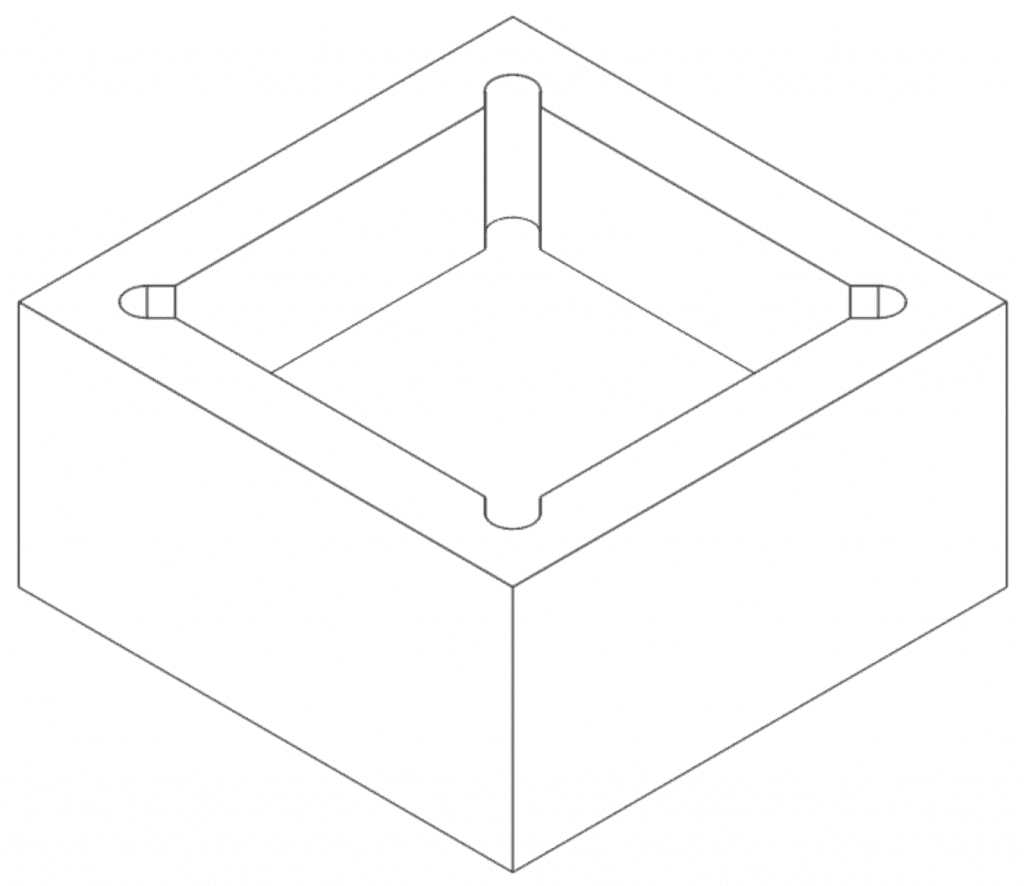
The most elegant (and least noticeable solution) is to centre a two-directional dogbone at a distance √(R² / 2) from the corner itself. This allows the entire area occupied by the corner to be machined whilst not removing any more material from the part than is necessary.
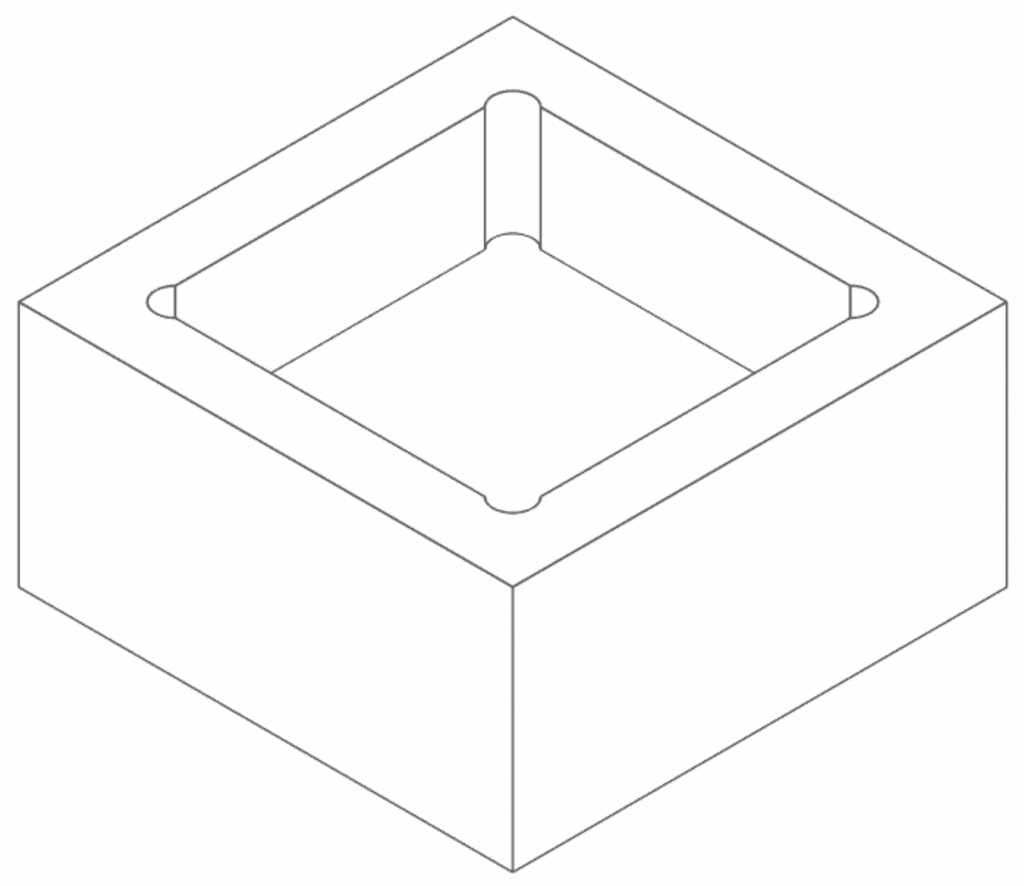
Once again, the radius of the dogbone is determined by the radius of the cutter. To increase cost-effectiveness, select the largest allowable radius for your design.
How to design parts for CNC machining
Proper part design is crucial for engineers looking to produce parts via CNC Milling and Machining. Understanding machining square corners is just one aspect of CNC part design. Careful thought must also be given to wall thickness, cavity sizing and tolerances.
Our beginner's guide to CNC Milling can help you with any preliminary questions you may have about the process. Make sure to keep checking back for more technical resources as we expand the website.
Get It Made manufactures bespoke parts through CNC Machining for a wide range of industries. Each project is meticulously planned for efficiency and value. Contact us today to discover our range of services, and how we may be able to help your business.