What is CNC Milling?
CNC milling is a specific type of CNC machining; if you would like to find out more about CNC machining process, check out our in-depth guide. Computerised controls produce a custom-designed part or product of high quality and precise finish. It is favoured in many industries due to its accuracy, consistency, and ability to increase production and uniformity. The CNC milling process begins with a CAD drawing (computer-aided design), and it is used to control the outputs of the CNC milling machine.
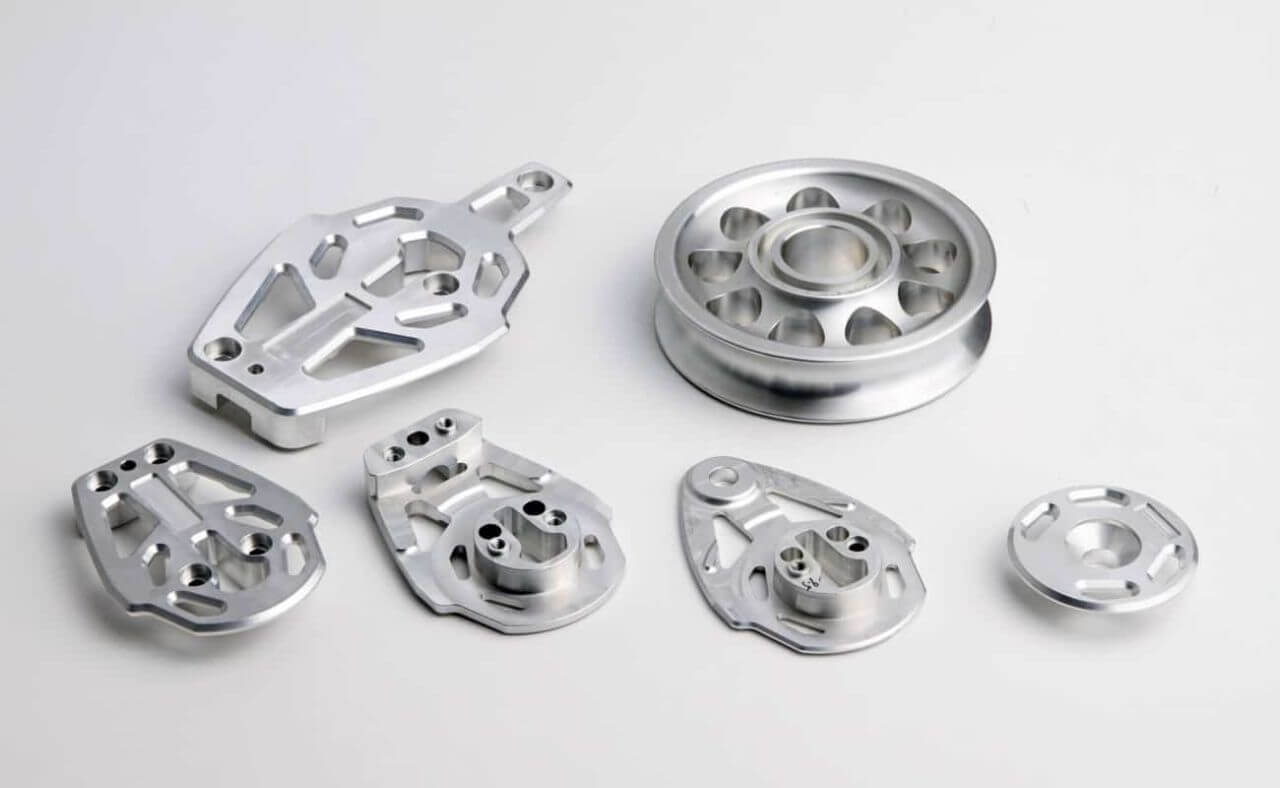
What is CNC Milling?
CNC stands for Computer Numerical Control, which means that a computer controls the milling machine. If you would like to find out more about CNC machining, check out our in-depth CNC machining guide.
Read on for a detailed look into the CNC Milling process, the anatomy of a CNC machine, and the different types of CNC milling available.
How Does a CNC Machine Work?
CNC Milling is a subtractive manufacturing process that uses computer-controlled machines to remove material from a block (known as a blank or workpiece) and shape it into a finished part. The process begins with a CAD model, which is then converted into a CNC program and set up in the CNC machine.
{{cta-banner}}
CNC Milling Machine Uses
CNC milling machines are versatile and can be used in a variety of applications. They are particularly effective in creating complex 3D shapes and are commonly used in industries such as automotive, aerospace, and medical. CNC milling machines can work with a wide range of materials, including metals like aluminium and steel, as well as plastics and composites.
What is a CNC milling machine?
A milling machine manufactures high-quality parts to a high level of detail and finish. CNC milling machines use rotary tools to cut away at the material, with instructions originating from the CAD file, to create the part design.
The function and coordinates of the cutter are controlled by the milling machine's computer, with minimum human input needed to complete manufacturing.
CNC milling machines are engineered to mass-produce many components from various materials and plastics. The core function of a milling machine involves mechanically cutting away at a workpiece into the desired shape.
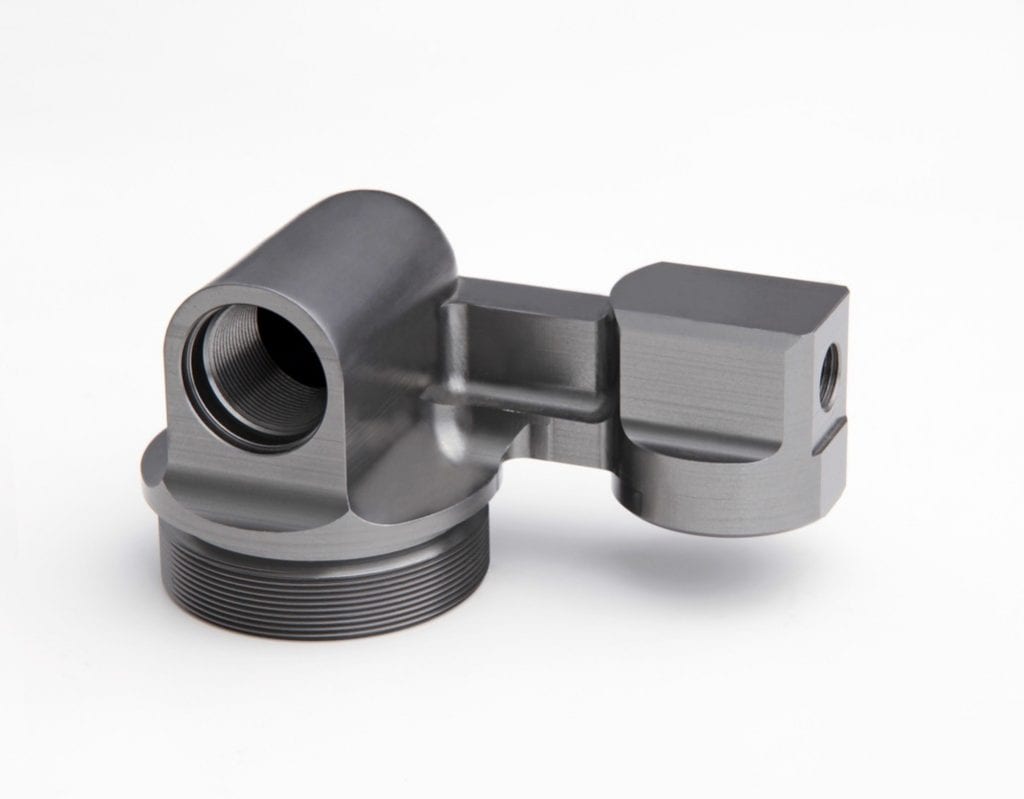
How does CNC Milling work?
The CNC milling process works by the machine reading coded instructions and then putting them into operation. It all starts with developing a 3D CAD file representing the final part. Once completed, the design is converted into a machine-readable format.
CAM (Computer-Aided Manufacturing) software then exports this to a CNC machine program, usually in G-code format, which acts as the instructions, directing every move that the machine makes. This replicates the CAD design in the chosen material with high accuracy and efficiency.
For more information on CAD file formats and the software needed for CNC Machining. See these guides:
CAD software for CNC Machining
CAD file formats
Using subtractive machining technology, CNC milling can produce high and low volumes of highly complex and intricate parts.
Material is removed from a blank workpiece, and the milling machine uses a rotating cylindrical tool called a milling cutter. Depending on the milling machine being used, the machine can cut in different angles and move along different axes.
The final part will have first been designed via CAD, or Computer-Aided Design, before being inputted into the milling machine for final production.
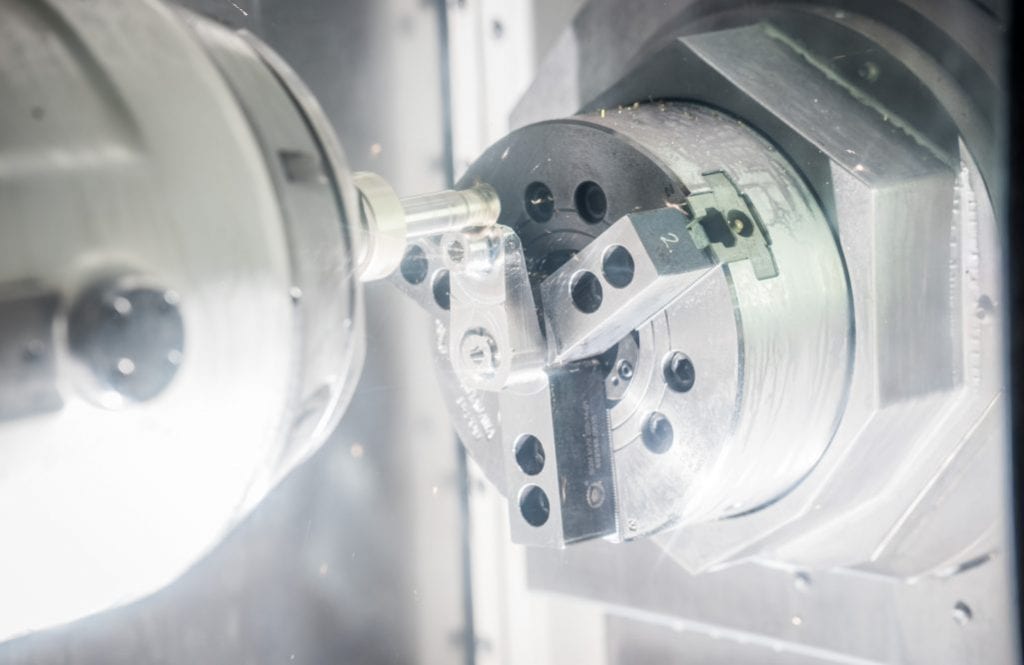
What does a CNC Milling Machine do?
A CNC milling machine makes intricate parts for several industries using subtractive machining technology. The milling machine cuts away at the workpiece and crafts the final piece via the 3, 4 or 5 axes.
Depending on the number of axes the CNC milling machine has, the more complicated and intricate the final piece can be. A CNC milling machine is used by various industries - including aerospace and medical industries - to manufacture complex parts.
CNC Milling Process
Some milling machines will be more appropriate than others, depending on various factors. The complexity of the CNC milling operations will be dependent on the design of the final part. The more structurally important and high-end the part or product is, the more complex the design may need to be.
For example, a more complex machine may need to be used for intricate designs requiring high precision, such as medical or aerospace components. This is to achieve the final design, finish, and aesthetic.
Basic parts that are machined for more general use may not require such high precision or high-quality finish. Complex and intricate designs will typically require additional milling.
Often milling machines utilise either 3, 4 or 5 axes.
For simpler parts, fewer axes are needed to achieve the final design. Simple geometries can generally utilise a 3-axis milling machine. They are easy to program and operate, achieving excellent accuracy at a low cost.
The cutting tools are attached to a spindle that works on three linear axes. They can spin at thousands of RPM, meaning even the sturdiest of materials can be cut through with ease and accuracy.
3-axis machines are the most common variety of a CNC mill and can cut vertically (Z-axis) and in an X and Y direction.
However, it’s usually not possible to machine undercuts with 3-axis CNC mills. These are features that cannot be accessed with a standard end mill. This means that more complex designs may require a more complex milling machine.
The 4-axis milling machine is more sophisticated, with the additional ability to rotate on the X-axis (similar to a lathe).
5-axis milling machines include rotation in both the X and Y-axis. They are the most complete milling machines available and are implemented for highly complex designs such as medical devices and implants for the medical industry, impellers and aerospace structures.
Top Tip: Read our guide understanding the CNC Milling process
Top Tip: Read our guide How to Machine Square Corners with CNC Milling
Features of a Milling Machine
The main features of a milling machine can generally be condensed into seven separate parts. These features include:
- Knee - The knee is fixed to the column, but it is adjustable. It supports the saddle and the worktable. It can be lowered or raised on the Z-axis.
- Column - The column is the main support structure for the machine. It works as a reinforcement for the other machine parts.
- The saddle - The saddle is located over the knee and below the worktable and it can be moved parallel to the axis of the spindle. It moves the workpiece horizontally if needed.
- The worktable - The area located on top of the saddle where the workpiece is fastened. The milling machine’s worktable can be adjustable, depending on the type of machine, and be used vertically and horizontally.
- Spindle - This is a rotating component that holds either the machine tool or the arbour, and it is driven by an electric motor.
- Arbour - The arbour is used in horizontal milling machines. It is inserted into the spindle and works as a shaft that can be used to mount different machine tools.
- Ram - The ram is normally found in vertical milling machines, and it is fixed to the top of the column where the spindle is supported.
- Machine tool - The machine tool is the component that performs the milling operation. It is held by the spindle and removes materials from the workpiece. There is a wide range of machine tools.
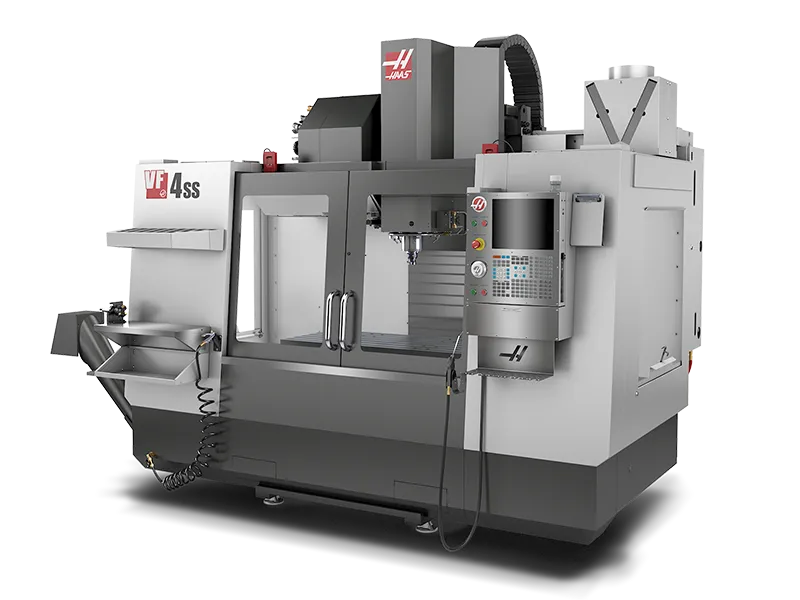
Types of CNC Milling
Vertical milling
With vertical milling, a 3-axis milling table is the work surface, which sits below the arm, to which a spindle is attached.
The spindle can be stationary if a turret vertical mill is used. In this case, the table moved along both X and Y axes.
Meanwhile, the table only moves along the X-axis if a bed vertical mill is used. The spindle travels along the length of the arm in the Y-axis direction.
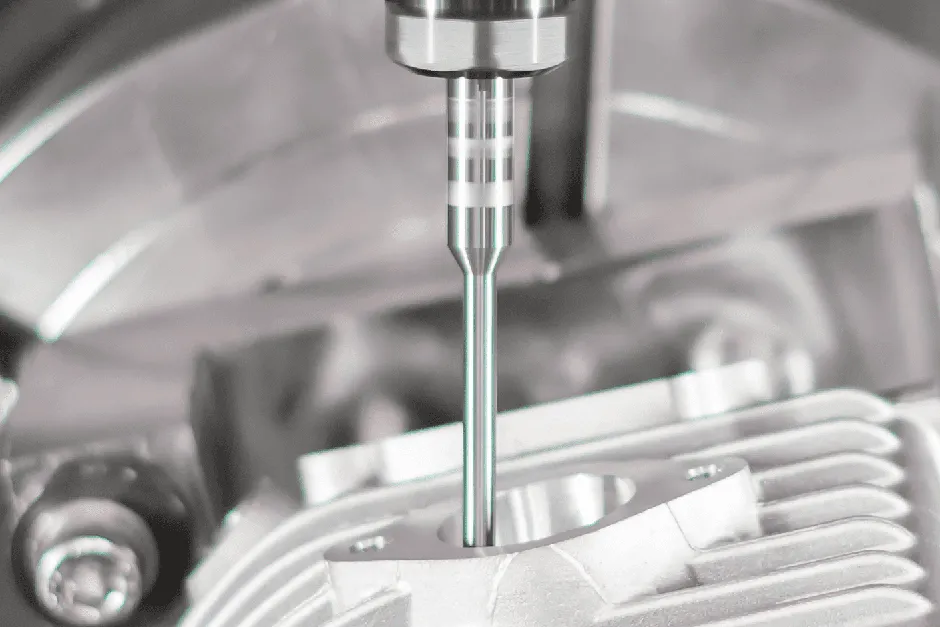
Horizontal milling
With horizontal milling, the spindle operates horizontally instead of vertically, and all other horizontal CNC milling machine components are similar to vertical milling.
Generally speaking, horizontal mills are best suited to heavier projects or longer projects. They are also suited to parts that require a large amount of material to be removed as the swarf falls away from the part and cutter.
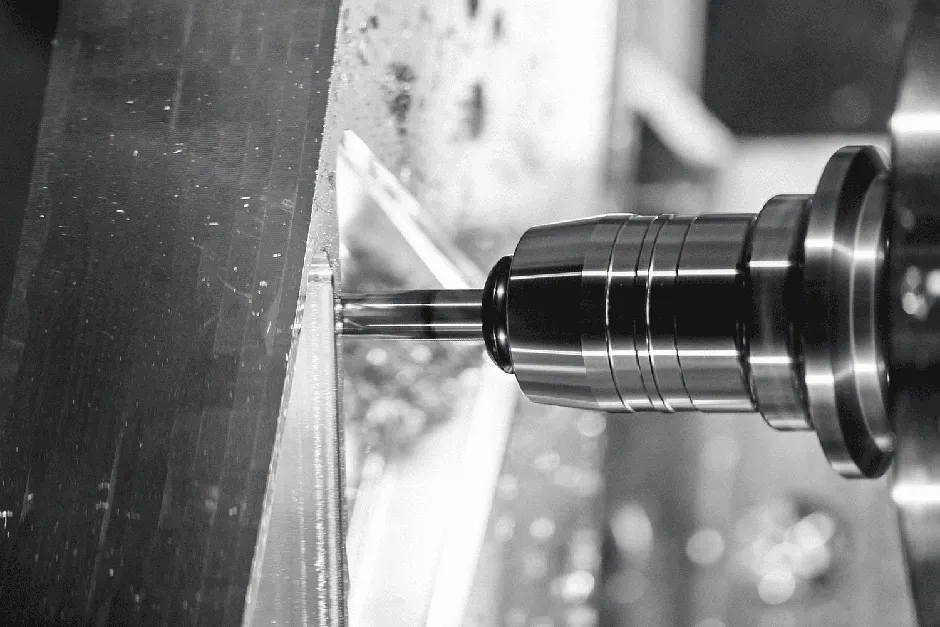
Face milling
The cutting tool’s axis of rotation is perpendicular to the surface of the workpiece.
It employs face milling cutters, with teeth both on the periphery and the tool face, the latter of which is used for finishing applications.
Face milling is also used to create flat surfaces and control a finished piece. Face milling can produce higher-quality finishes than other milling processes and is compatible with vertical and horizontal milling machines.
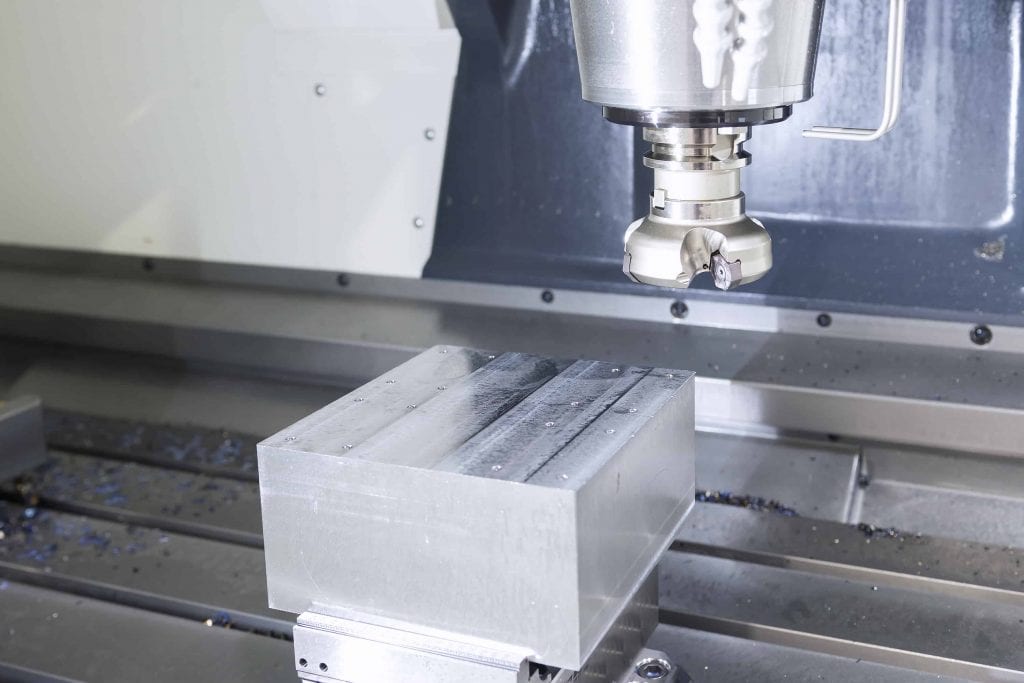
Plain milling
The cutting tool’s axis of rotation is parallel to the surface of the workpiece. Plain milling cutters have teeth on the periphery that perform the cutting operation. Both narrow and wide cutters are used.
This allows for deeper cuts and for larger surface areas to be worked on. A coarse and fine-toothed cutter are both used. Slow cutting speeds and fast feed rates are used for the course cutter and vice versa for the fine-toothed cutter. This enables a more detailed final part.
Angular milling
This is a milling operation where the cutting tools’ axis of rotation is at an angle relative to the surface of the workpiece.
Therefore, single-angled milling cutters can produce more angular features, such as grooves, serrations, or chamfers.
Form milling
Form milling is best used for milling operations where more irregular surfaces are involved. Contours, outlines, edges, or parts with curved, flat surfaces.
It employed milling cutters or fly cutters specialised for particular applications – for example, concave cutters or corner rounding cutters. Hemispherical or semi-circular designs or other similarly intricate designs with complex parts would benefit from the form milling technique.
Types of a Milling Machine
As there are various types of CNC milling, there are also a number of unique milling machines with distinct characteristics and functions. Some different types of milling machines are:
Ram-type
This machine allows the machine tool to manoeuvre on the XY axes through a spindle that is fixed to a movable arm on the column. Horizontal milling machines are often ram-type.
Knee-type
Knee-type machines will vertically adjust the worktable instead of the spindle. The knee will lower and raise the worktable along the column to reach the machine tool. Plain milling is often done on a knee-type machine.
Planner-type
The worktable is fixed along the YZ axes in this milling machine with spindles that are able to move along the XYZ axes. They can also simultaneously support up to four machine tools.
Bed-type
These milling machines have the workpiece fixed below the cutting tool. The machine tool may be able to move along the XYZ axes.
How much does CNC Milling cost?
The cost of CNC milling is dependent on various factors. The expenses of CNC milling largely stem from how long it takes to machine each piece. Longer milling times could be a result of needing to remove large amounts of material or hard materials.
Depending on the part design, some parts may involve more complex tools or cutting. Other factors that define the cost of CNC milling are material and part complexity.
You can click here to arrange a CNC Milling quote with the team at Get It Made, otherwise find out more about our CNC Machining services.
Benefits of CNC Milling process
High quality and precision is guaranteed
The very nature of CNC machining as a process leaves very little room for error and high levels of accuracy and precision. This is because it operates from a computer-led program, inputting 3D designs that have been developed via CAD (Computer-Aided Design). The manufacturing process begins when operations are launched via a machine interface.
The machine executes instructions received from the machining program without the need for manual input. These automated processes allow for ultimate precision to ensure even the most finite and complex geometry can be technically managed.
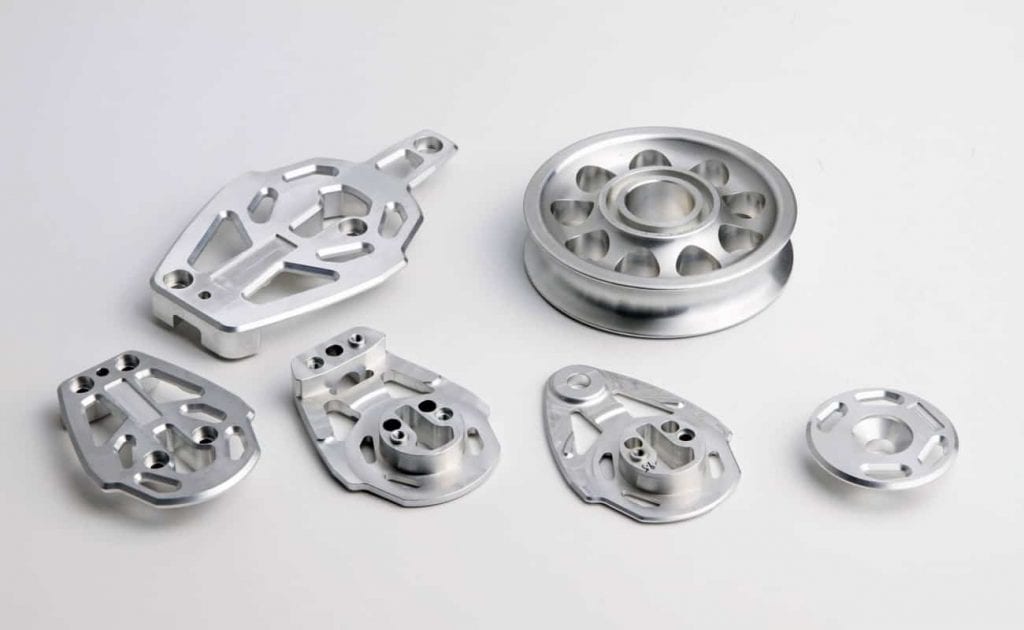
CNC milling allows for high production output
The level at which CNC machines operate means they are capable of high levels of production due to the automated processes involved.
CNC milling is a trusted and popular option if a part needs to be produced in high volume, with every part meeting the same level of consistency in terms of quality and finish. It is particularly easy to program and operate a 3-axis machine, achieving high accuracy at a low cost.
CNC milling is a less labour intensive process
Using a CNC milling machine significantly reduces the labour involved in the production process. At total capacity, CNC milling tools can spin at thousands of RPM (revolutions per minute), resulting in high production output while also being a time-saving expense. No manual processes could achieve a similar output.
It’s worth noting that the simpler the design is, the less human intervention is needed. For example, if a complicated design required the blank to be moved in the process, this would involve machinists to ensure the process was completed safely and securely.
CNC milling machines with uniformity
CNC machining tools are designed and developed to cut away at the workpiece with the highest levels of accuracy. The movement is directed by the computer program, meaning every single part is produced with the same level of accuracy.
On a broader scale, components can be produced in high volume, with the manufacturer safe in the knowledge all completed parts will be of the same standard and finish.
Get It Made is an established bespoke manufacturing partner for high-precision CNC milling and machining. Get in touch to discuss your project’s requirements and kick-start your manufacturing. Arrange a CNC milling quote today, and our team will get back to you in 24 hours.