Common Items Made Using Plastic Injection Moulding
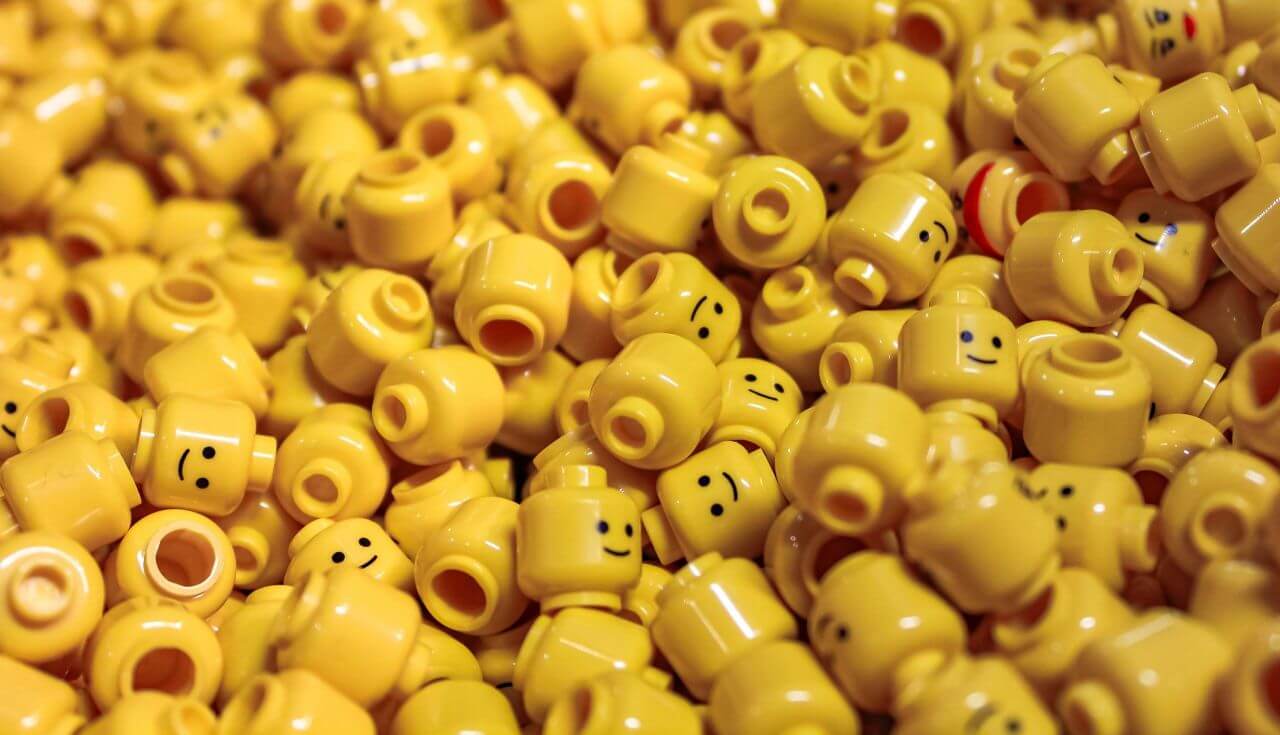
What is plastic injection moulding?
Plastic injection moulding is a popular manufacturing process whereby plastic products can be mass-produced quickly and cost-efficiently. The process works by injecting molten plastic into a pre-designed mould at high pressure and heat. The molten plastic then fills the hollow mould before cooling rapidly and setting in the desired shape.
You can discover Get It Made’s range of Injection Moulding guides below:
Plastic Injection Moulding Design Guide
Tips to Reduce Injection Moulding Costs
Gas Assisted Injection Moulding
Why use injection moulding?
Injection moulding is an incredibly popular method for mass-producing products because it involves minimal labour cost and can consistently produce high-quality, uniform results. For companies looking to mass-produce plastic parts, injection moulding is often the answer. With high production rates, reliability of high tolerances, minimal scrap loss and need for finishing, it is no wonder that injection moulding has grown in popularity.
{{cta-banner}}
History of injection moulding
Injection moulding as a manufacturing process has been around for longer than you may think! The first examples of injection moulding machines were invented in the 1940s, and the industry subsequently expanded rapidly. World War Two (WWII) created a demand for inexpensive mass-produced products, meaning resources were ploughed into the plastic moulding industry.
Injection moulding by industry
There are various industrial sectors that commonly use injection moulding. These include:
- Medical
- Electronics
- Food
- Household Goods
- Aerospace
- Automotive
- Green Energy
- Life Sciences
- Sports Industry
Plastic Mould Manufacture
Plastic injection moulding is a highly efficient manufacturing process, widely used to create a variety of plastic parts to precise specifications. At Get It Made, we utilise advanced machinery and a team of experienced engineers to melt plastic pellets and inject them into a mould under high pressure. This process ensures the production of high-quality plastic parts and products.
Common items made using injection moulding
Automotive interiors
Due to the high-quality finish of products when injection moulded, many car manufacturers benefit from the injection moulding process. It is a process that can guarantee a high-quality finish, compared with CNC machining processes that, although accurate, does not allow for a range of moulded textures frequently found in car interiors.
Children’s toys
Children’s toys are another product category that often use injection moulding to mass-produce products. The boom in popularity of plastic children’s toys emerged after WWII when plastic dolls became available across the market. In the 1940s, Fisher-Price came to the forefront of producing plastic toys. In the late 1950s, the barbie doll hit the market with incredible success. The ‘playability’ factor of plastic material became a primary factor in leading the action figure and doll toy lines.
When manufactured to high quality, plastic was far more robust and safer for children to play with, and soon plastic toys would lead the market for decades to come. The 70s saw more creative toys hit the market that utilised the literal flexibility of plastic to create more innovative products such as playdough. In 1974, arguably the most longstanding popular children’s toy, LEGO, was invented by Danish inventor Ole Kirk Christiansen.
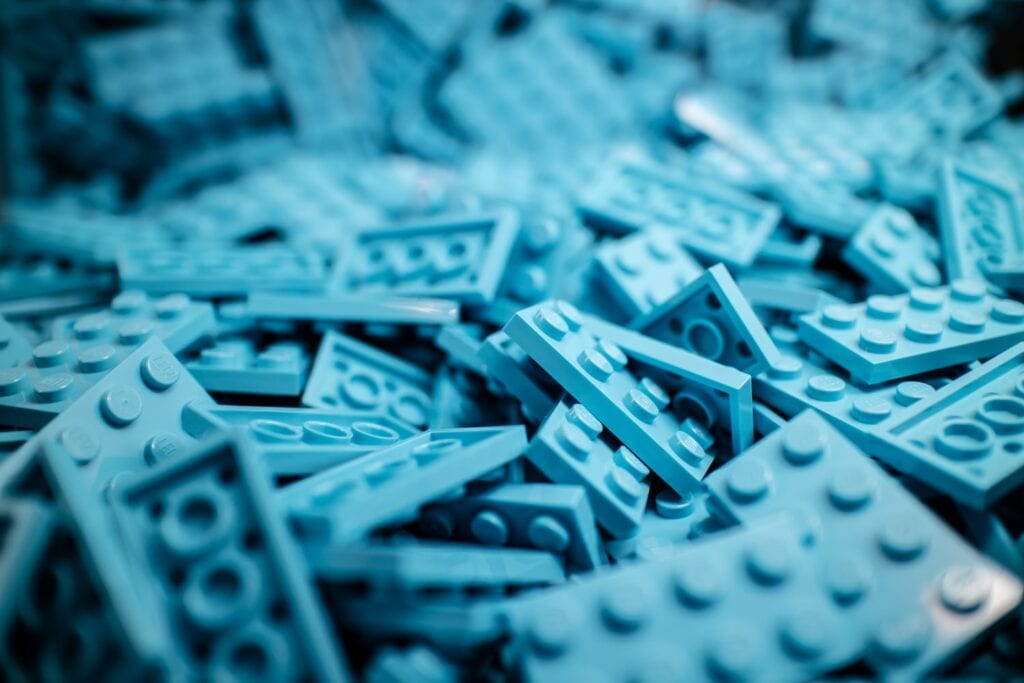
Smartphones
Smartphones may not be made entirely out of plastic, however, it is common for tiny fundamental parts of a smartphone to be made using injection moulding due to the accuracy needed for the part. This includes main bodies, buttons and cases.
Household items
Whether it's containers, shampoo bottles, cosmetic packaging, soap dispensers, or plastic kitchenware, there are a lot of everyday household items that are mass-produced using injection moulding. The flexibility of the process, i.e., the fact that most shapes can be manufactured to due the process, means that more complex designs for household items are not a problem.
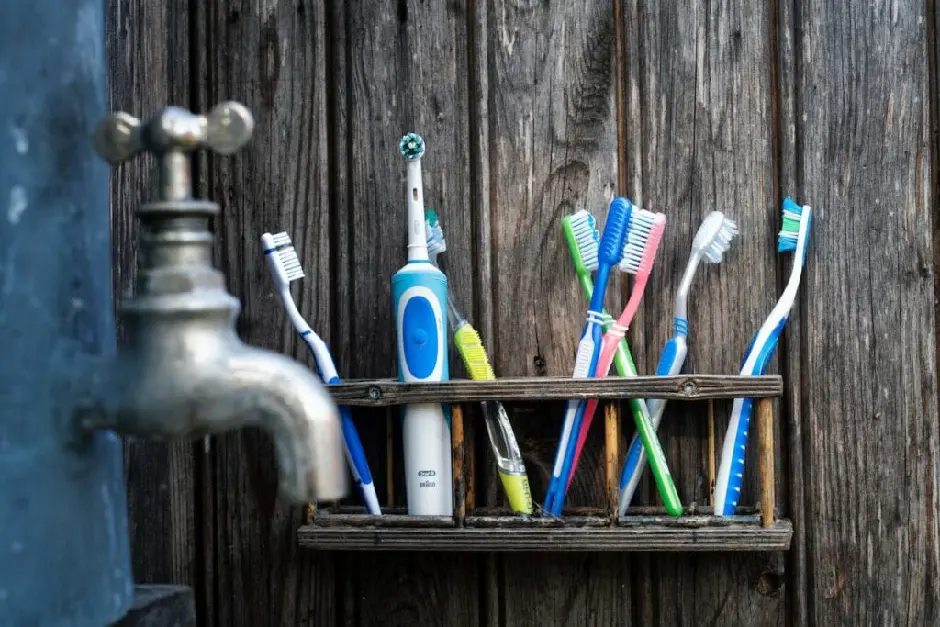
Common types of material used for injection moulding
Common injection moulding plastics include:
- Acrylonitrile Butadiene Styrene (ABS)
- Nylon (PA)
- Polycarbonate (PC)
- Polypropylene (PP)
- Polystyrene (PS)
Other Plastic Injection Moulding Products
- Medical Devices: Items like syringes, surgical instruments, and diagnostic devices are often made using injection moulding for precision and sterility.
- Garden Tools: Tools such as plastic rakes, watering cans, and plant pots benefit from the durability provided by injection moulding.
- Electrical Switches: The switches and casings for electrical components are often made using this method for their precision and insulating properties.
- Bottle Caps: Many bottle caps, especially for beverages, are produced using injection moulding due to the method's ability to produce uniform, tight-sealing caps.
- Disposable Razors: The plastic handles and casings for disposable razors are typically injection moulded.
- Toothbrushes: The plastic handles of toothbrushes are often produced using this method.
- Plastic Cutlery: Disposable forks, knives, and spoons are mass-produced using injection moulding for their uniformity and cost-effectiveness.
- Goggles: The plastic frames of safety and swimming goggles are typically made using injection moulding.
- Remote Controls: The plastic casings for TV and other remote controls are often produced using this method.
- Computer Keyboards: The keys and often the body of computer keyboards are made using injection moulding for precision and durability.
Get It Made can offer all these plastics and more for your injection moulded project in a wide range of colours.
For more information about how Get It Made can help with your project, check out our range of services. Otherwise, head to our technical toolbox for industry insights and more. Get in touch today and give us a call on +44 020 3286 6002 or arrange a 24-hour quote.