Get It Made

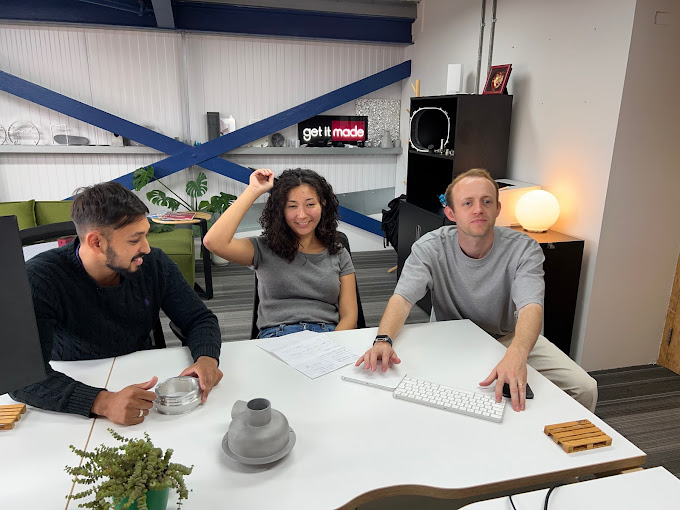
Get It Made is a manufacturer in London, England, known for its expertise in CNC Machining and a comprehensive suite of manufacturing processes. With a commitment to quality and precision, the company offers a range of services including CNC Machining, 3D Printing, Subtractive CNC, Metal Forming, Moulding, Casting, and Additive Manufacturing.
Unit 1 Southbrook Mews
London
SE12 8LG
UK
+44 20 3286 6002
team@get-it-made.co.uk
Luke Smoothy
2011
GB212932629
$$
2024-03-016T14:30:00+00:00
Worked with the Get it Made team for a Formula Student project. We had great customer service with frequent and easy communication. The parts arrived quickly and in perfect condition. High quality finish on the machined parts.
2024-01-31T08:30:00+00:00
Fantastic service and team, very responsive and cordial. Pleasure to work with and parts are top notch.
Tawon Uthaicharoenpong (Pipe)
2023-12-06T13:50:00+00:00
I order CNC machined part from them, come out really nice. The staff check my drawings and make extra effort to make sure they will get it right first time.
2023-12-06T10:20:00+00:00
Fantastic service from Get It Made, they couldn't have been more communicative helping me make a new part for my wing foil hydrofoil to help me go faster in next years races. Thanks!!!!
Tawon Uthaicharoenpong (Pipe)
2023-12-022T14:30:00+00:00
I order CNC machined part from them, comeout really nice. the staff check my drawings and make extra effirt to make sure they will get it right first time
2023-06-06T12:00:00+00:00
Get it made has consistently delivered high quality parts to tight tolerances for me. They're easy to deal with and have an impressive turn around time.
2023-06-020T14:30:00+00:00
Ambassadors in their field of engineering. CNC Machining project works completed by Get It Made was an excellent experience. From the quote to the customer service, right up to the order being delivered was seamless. Lead times were honest, and best of all, the order arrived earlier than expected.
2023-05-06T14:30:00+00:00
We have been working with Get It Made since 2019. Over the years, we have manufactured parts using their UK 3D printing service and CNC services to produce prototypes of our revolutionary vaccine cold-chain system.
2023-03-02T14:30:00+00:00
After spending a lot of time trying to identify a firm that could machine my miniature parts in medical grade stainless steel, with most turning down my requests due to the parts being too small, I finally found the Get It Made team. Communication was quick and efficient, delivery was super fast, and the parts not only look great, but also passed all my endurance and friction tests. Very highly recommend.
2023-03-016T14:30:00+00:00
We modified the models Christmas Eve . We didn’t realise it was the 24th but they still returned our call . Placed an order on 29th Dec Inquired on the 9th jan 2023 Shipping notice on the 10th Delivered to our door Monday 16th. How would they improve, I have no Idea
2023-02-06T15:45:00+00:00
Get It Made were very generous and flexible with their Aerospace Manufacturing Grant, producing a variety of supersonic wind tunnel models and bespoke propeller blades for us (University of Hertfordshire).
2023-02-06T09:30:00+00:00
It was a great experience working with the Get It Made team! They produced suspension components for our team (University of Leicester Racing) to compete in Formula Student 2022.
2022-09-23T14:30:00+00:00
Very satisfied with the overall service. Part arrived perfectly as anticipated. Correct tolerances and beautiful finish. Highly recommend.
2022-09-17T14:30:00+00:00
Very quick turnaround, product is exactly as requested and the price was exceptional. Will return with all machining work from now on.
2022-08-23T14:30:00+00:00
Great to work with! Get It Made has manufactured turbine rotors for me in a couple of occassions and the result is always amazing and ahead of schedule. Their team responds in less than 24h to quotations and to any other questions you have.
2022-08-19T14:30:00+00:00
Excellent service. Friendly, efficient and competitive pricing. I was turned away from a number of companies as I only required a single piece for a prototype. Get It Made
2022-05-19T14:30:00+00:00
Easy to deal with, fast turnaround and the metal finish on my CNCd components is very clean, with no machining marks. Will use again.
2022-05-011T14:30:00+00:00
Great communication and exceptionally short lead times and delivery. Parts were to spec and function as expected. Get It Made were always easy and friendly to contact, and were happy to provide updates on the machining or answer any questions. Without Get It Made, we wouldn't have been able to keep our project on track and meet deadlines. Would definitely use them again in time-critical situations.
2022-04-12T14:30:00+00:00
Working with the Get It Made team has been an absolute pleasure. They are nothing like the past manufacturers that I have worked with – they reply to any queries very quickly and are very helpful in providing any additional information required. They also go the extra mile to make sure everything is perfect by sending video renders of sections highlighted that needs additional polishing. I was working very close to my project deadline, but I had absolute confidence in the them that they will manufacture everything in the quoted lead time, and they did not disappoint! The final product was better than I expected and the Get It Made team is very friendly – nothing to complain about. The overall experience I had was excellent and I would definitely recommend it to everyone who needs bespoke parts machined.
2022-04-12T14:30:00+00:00
Start to finish, very good experience. I wanted some one off parts made for a lockdown project and it was no problem for get it made. Quotation was provided extremely quickly, I had feedback the next day. The team were extremely helpful on re-quoting for small design changes and when I placed the order, the whole process was quick and easy. The team were also helpful when the manufacturer had some small issues with anodising the part, the issue was quickly resolved and the final product was exactly as I wanted. Highly recommended, I will be using them again.
2022-03-15T14:30:00+00:00
The Team over at Get-It-Made are truly exceptional. We would recommend them to anyone looking for a fast, reliable and cost effective solution for any cnc project.
2022-03-13T14:30:00+00:00
From start to finish Fin was always on hand to deliver quotes, assistance, advice and finally deliver a product. Faultless. Thanks very much.
2022-03-11T14:30:00+00:00
Absolutely fantastic experience from start to finish! Bring any of your projects to life. Friendly, genuine people who obviously really care about their work. I had never done anything like this and the website is so professional it was almost intimidating, reserved only for huge industrial projects - Wrong! I filled in the form to request a quote and just as they claim, I received a really friendly reply straight to my email in significantly less time than 24 hours. So far so good, really impressed. I forgot to add a request to the online form and it was quickly resolved and the quote was recalculated. All that was required was some basic information, some renders and.step files of the parts but all information about formats is available on their website. The quote was really clear and straight forward to understand even for someone who isn’t super technical. Price per part (in my case four), finishing options and extras, and an expected date of arrival. My parts arrived sooner than I expected in a really nice compact package (looking at you amazon) double wrapped in first tissue paper and then packing paper. It’s nice to see something other than plastic. The parts are beautiful, with only one minor imperfection which could very well have been my very amateur cad skills. It really is wild to see something I drew on an iPad be a real part in a matter of a few weeks. This isn’t a particularly cheap option, but the machines, maintenance of the machines, technical knowledge etc all come at a cost, and actually when you break it down, it actually isn’t unreasonable at all. Great team, and I will be continuing to work with them for refining this project and any others I have in the future that require their services! Sincerely 11/10
2022-03-021T14:30:00+00:00
I have been using Get it made through work since the end of 2018. They have consistently delivered parts on time, to the design. The team is very friendly, helpful and knowledgeable, offering improvements to designs and drawings to get the parts we need. When (very infrequently) there is an issue they are always quick to resolve (often before we see the part, great QC) without any fuss. Thanks team, we all really appreciate it.
2022-02-06T17:30:00+00:00
Great communication and exceptionally short lead times and delivery. Parts were to spec and function as expected.
2022-02-06T11:00:00+00:00
Fast, Reliable & Great Customer Service! Get it made produced a series of suspension and powertrain parts for Kingston Racing's Formula Student vehicle.
2021-06-15T14:30:00+00:00"
Working with Get It Made for all our prototyping was an absolute pleasure. Next to immediate response, fast lead times, often arriving before the stated date. The attention to detail and customer service was second to none and all at the most competitive price point that couldn’t be beaten here in the U.K. We would and will continue to use them as a supplier for our needs.
2021-06-15T14:30:00+00:00"
I've worked with Get It Made on numerous occasions and it's my experience that they are a company who are at the top of their game when it comes to reliability and quality. When you're working to a tight deadline it really takes the stress out of the whole process knowing you have a manufacturing partner who can be trusted to deliver the parts on time and within tolerance. I also can't speak highly enough of the customer service. They're quick to reply to enquiries and keep you well informed throughout the whole process. In the past I've also found that companies that provide highly technical services can have an air of arrogance when talking to a potential customer who isn't as knowledgeable about the subject matter. This couldn't be less true of Get It Made. It's also very refreshing to work with someone like Luke, who gives such honest appraisals of a design and it's manufacturability. He's always interested to know how the part will be used and is always at hand to offer advice on part geometry as well as material choices and finishes.
2021-06-15T14:30:00+00:00"
Really good service! I emailed get it made for a quote and received it back within a few hours at a very good price and a little over a week turnaround time. The parts arrived in a finished and quality far beyond expectations would 100% recommend.