CNC Machining Design Guidelines
Learn everything there is to know about CNC machining in our CNC Machining Guide.
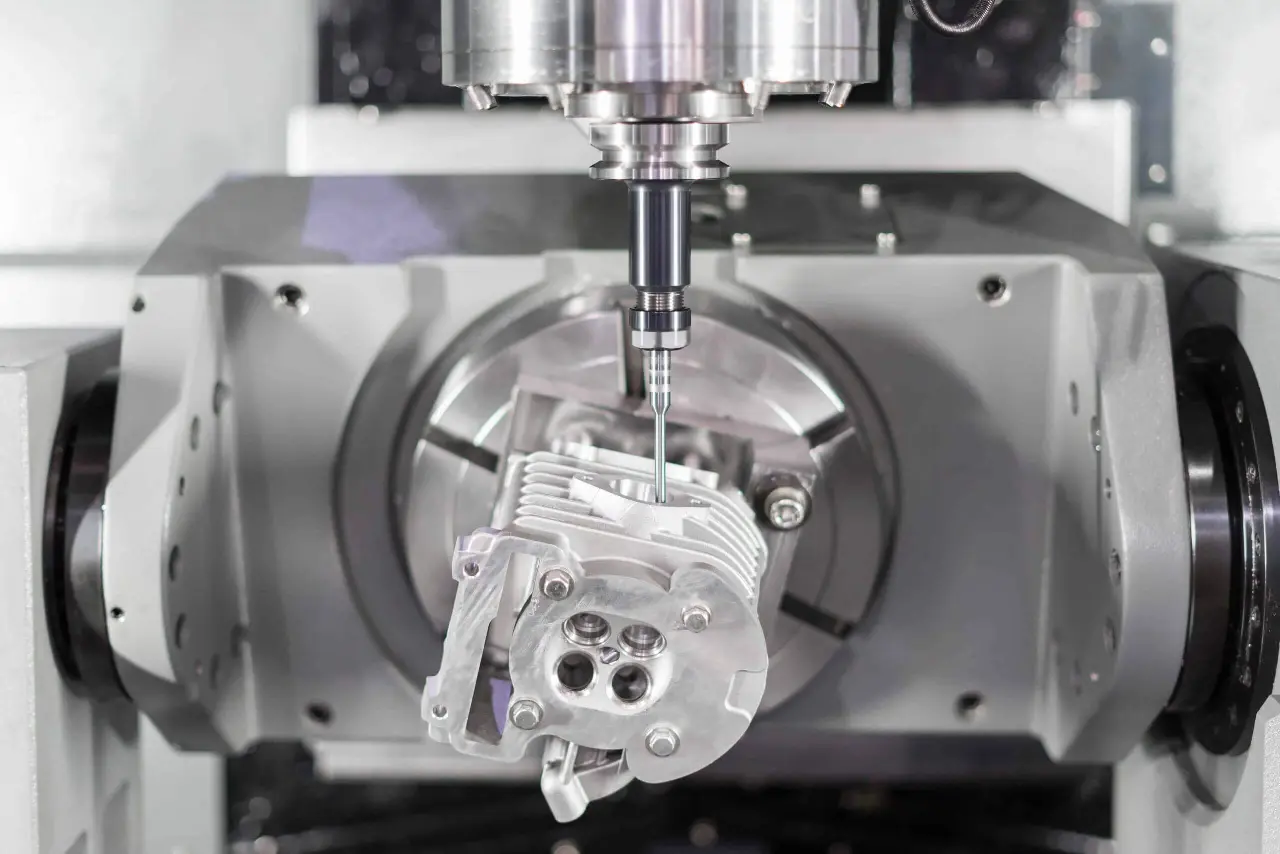
Learn everything there is to know about CNC machining in our CNC Machining Guide.
Deciding the various manufacturing operations required with CNC machining will largely depend on the product's final design; the design will determine the raw material size, weight, material, dimensions, and complexity.
These various factors and the end-use of the product will determine the all-important cost of the part and, therefore, overall production cost. Often, CNC machined parts require the utmost precision and a high-quality finish. This is due primarily to CNC machined parts being used in mission-critical situations. One of the main reasons CNC Machining is so popular is the high-quality results; however, quality needn’t come at a high cost. Considerations need to be made early on to ensure every possible element of the design and CNC process has considered not only longevity and quality but cost efficiency, too.
These CNC Machining design guidelines advise engineers and designers on how to design cost-efficient parts that can be successfully CNC machined with the least effort.
{{cta-banner}}
CNC design considerations
The design of a CNC part should consider various elements during the initial design phase, such as:
- The type of material being machined
- The kind of CNC machine
- The size and shape of the product
- How the final product will be used (e.g. strength requirements)
- How many different processes or operations are needed
- Common tool sizes and whether bespoke tools are needed
All of these elements are important, as they can help determine the final cost of a CNC machined part and therefore impact the final costs. One key rule designers and engineers can use to reduce costs is reducing the required machining time. However, it’s also important to remember that optimising just one part of the process can only go so far in creating time and cost savings – all the elements have to be considered practically when looking to optimise the design.
Tolerances
Tolerances denote the dimensional accuracy of a part and refer to the amount of deviation in a specific dimension of a part compared with the nominal value.
Parts with tight tolerances are typically harder to machine, and it may take more than one attempt to machine the component to the desired tolerance. Naturally, this can impact costs. Therefore when considering tolerances, try to make the tolerances as loose as possible to reduce costs.
Size recommendations
The size of the part impacts CNC Milling and machining costs. Generally speaking, the more significant the part, the larger both the material and machining costs. However, do also consider part complexity; the more complex the design, the more machining time will be required. The smaller and simpler the geometries are better.
3 Axis Machining
Consider the type of machining process being used. Where possible, it is recommended to keep the design to 3 axis machining instead of 4 or 5 axis machining. Three-axis machines are cheaper to run and are currently more prevalent in the CNC machining industry. Additional axes increase set-up time and require different machinist skills. Try to reduce the number of necessary reorientations to machine the part. Reorientations incur additional set-up and programming costs.
Sometimes multiple faces will be needed to be cut. More complex designs can benefit from 5 axis machining. This will require additional set-up but can improve quality, occasionally five-axis CNC machining will be the only suitable solution.
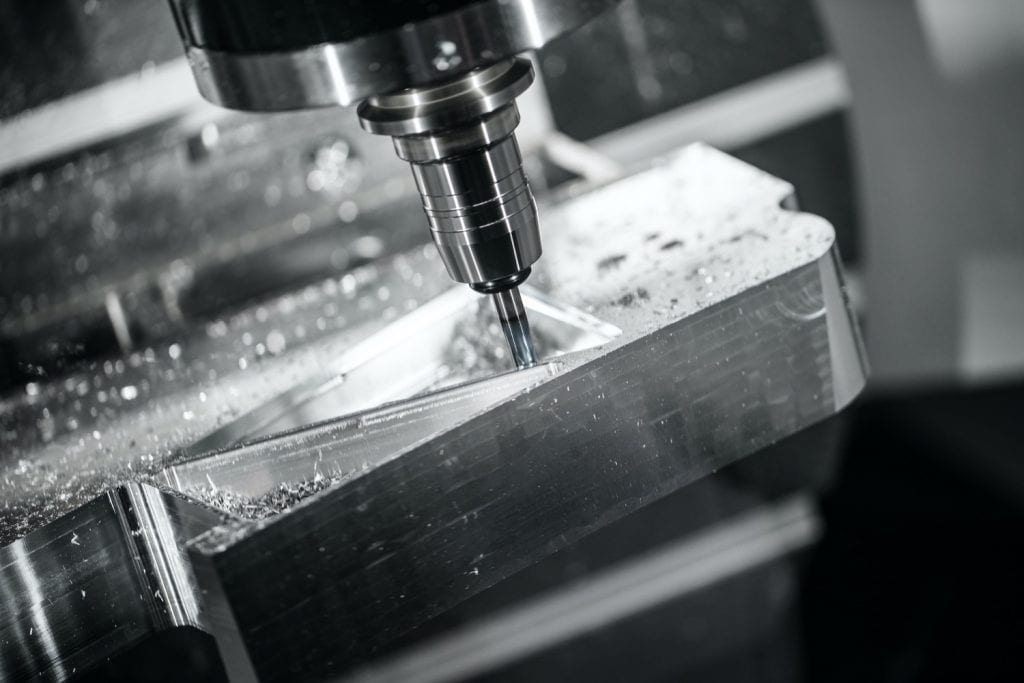
Material selection
Material selection can also significantly impact the cost and time of a CNC machined part. In general, plastic is favoured as a cheaper and time-saving solution as it is relatively easy to machine. There are many polymers with various strengths, uses and characteristics; however, in many cases, metal will be the suitable material. This is largely reliant on how the final part will be used. Aerospace and medical industries can often require demanding and expensive materials. However, for many parts, cheaper and general-purpose polymers can be utilized.
For more guidance on choosing the suitable material for your CNC machining needs, read Get It Made’s guide: Choosing the Right Metal for CNC Machining.
Considerations that should be taken into account:
- Is a specific chemical resistance needed?
- Will the product need to be thermally stable?
- Does the product’s density need to be considered?
- What are the aesthetic requirements?
The form, fit, and function are all essential elements to think about.
Undercuts
Designers should be aware of the costly implications of undercut features. Undercuts are difficult to machine and may require expensive custom tools to create the exact geometry – this will, of course, increase the final cost. If an undercut is necessary, designers should ensure the depth of the undercut is not too deep. The shallower, the better, which creates undercuts the tool can reach. Often undercuts would need to be produced using Electro Discharge Machining (EDM), a process commonly used in the production of injection moulding tools.
Wall thickness
The wall thickness is also an essential consideration at the design stage. If wall thicknesses are too thin, this may require slower, more careful machining, which increases costs. Having larger wall thicknesses there can also mean less material to remove, further reducing machining costs. The wall thickness should be greater than 0.75mm; if walls are too thin, this will, of course, impact the quality and durability of the final part.
CAD system
One final cost to consider is the time and cost spent designing the parts themselves. Using an efficient, easy to use CAD package could save many design headaches! We recommend the following CAD packages:
- SolidWorks
- Autodesk Inventor or Fusion 360
- OnShape
Modern CAD systems can be beneficial for designers who need to design complex 3D surfaces and features and perform detailed analysis.
For more CNC Machining guidelines, check out our Injection Moulding Design guidelines here, or get in touch today for a 24 hour CNC Machining quote.
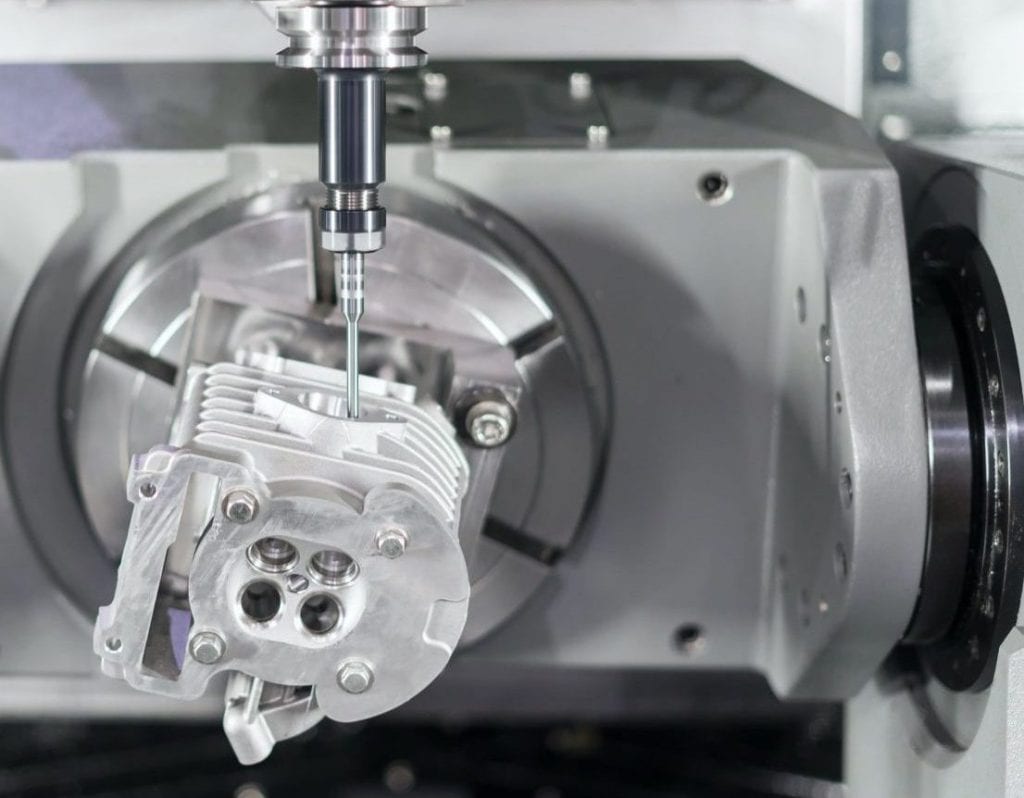