What is CNC Machining?
An introduction to CNC Machining CNC Machining is seen by many as a vital element to the core processes of manufacturing. Working alongside Computer-Aided Design, CNC Machining is the process of mass-producing parts and materials of specific designs and dimensions through the use of computer numerical control. That is to say, a computer directs the machine responsible for creating the final product.
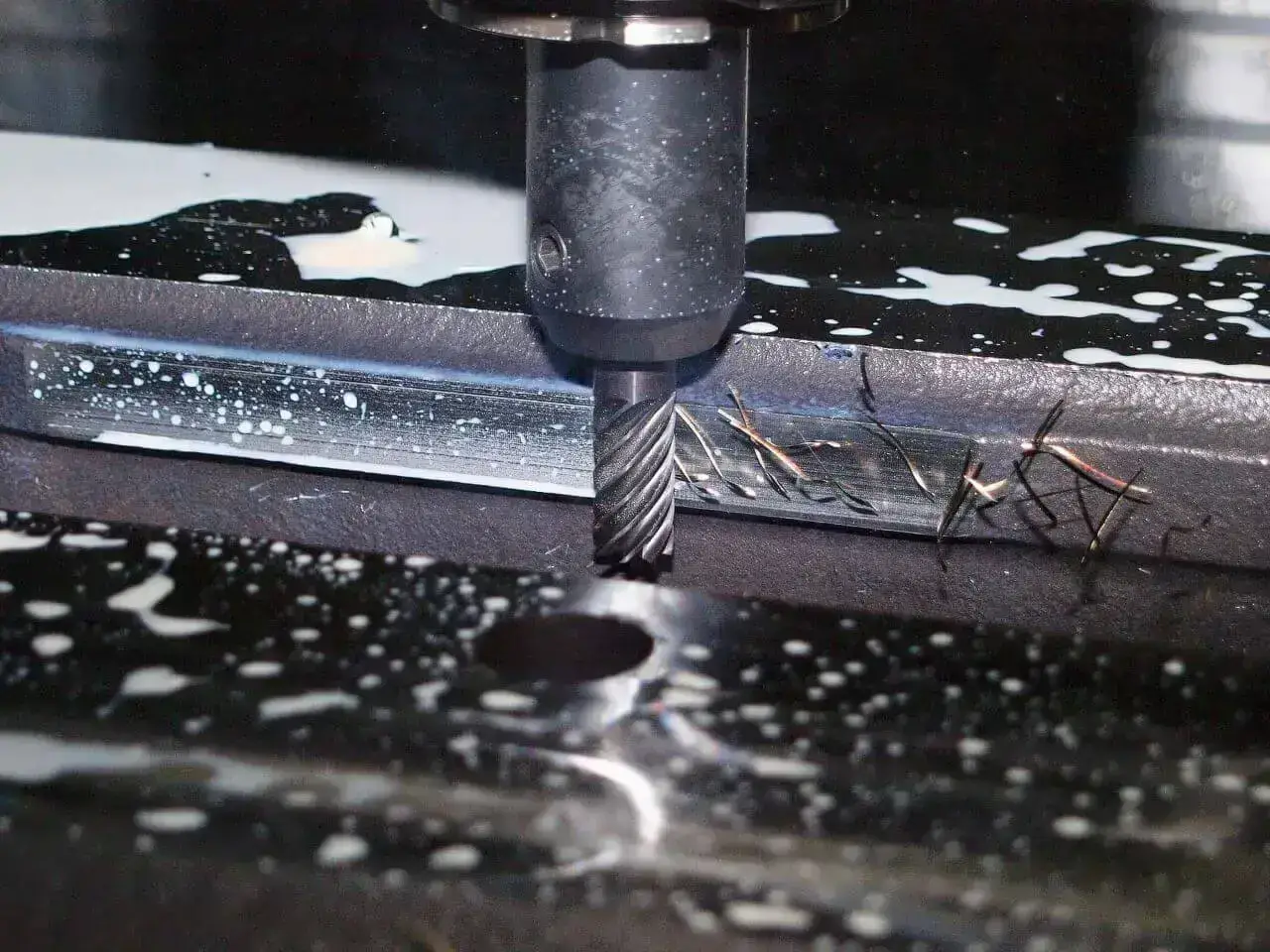
What is CNC Machining and how does it work?
At its core, CNC Machining involves the processes of subtractive machining technology. Simply speaking, its technology works through material removal mechanisms, which, following input from computer-aided software, creates the product. This is achieved through cutting tools, which shape and ‘cut’ the final product from a solid block, also known as a blank, or a workpiece.
Top Tip: You can read up on Get It Made’s CNC Milling & Machining processes here.
CNC Machine Process
The CNC machining process begins with a digital 3D design of the part, which is created using Computer Aided Design (CAD) software. This design is then converted into a series of commands, which are sent to the CNC machine. The machine interprets these commands and uses its tools to cut, shape, and form the material into the desired part. The process is highly precise and can produce complex shapes that would be difficult to achieve with manual machining.
{{cta-banner}}
Why is CNC Machining popular?
The growth in popularity of CNC Machining stems from the high accuracy and quality finish that can be achieved. Why? Because the final piece has been crafted from a CAD file. With Computer-Aided Design and, therefore, high automation comes a reduced chance for error.
For this reason, CNC prices are competitive for both one-off custom parts and medium volume productions. However, you can find companies who will work with you to keep costs down while still delivering a high-quality product. If you are in need of a CNC Machining quote, contact Get It Made to get started.
CNC Machining is used in multiple industries due to the reduced risk of human error and high accuracy, precision-made products. For sectors where mass production, cost efficiency and accuracy are essential, CNC Machining techniques are considered integral to the production process.
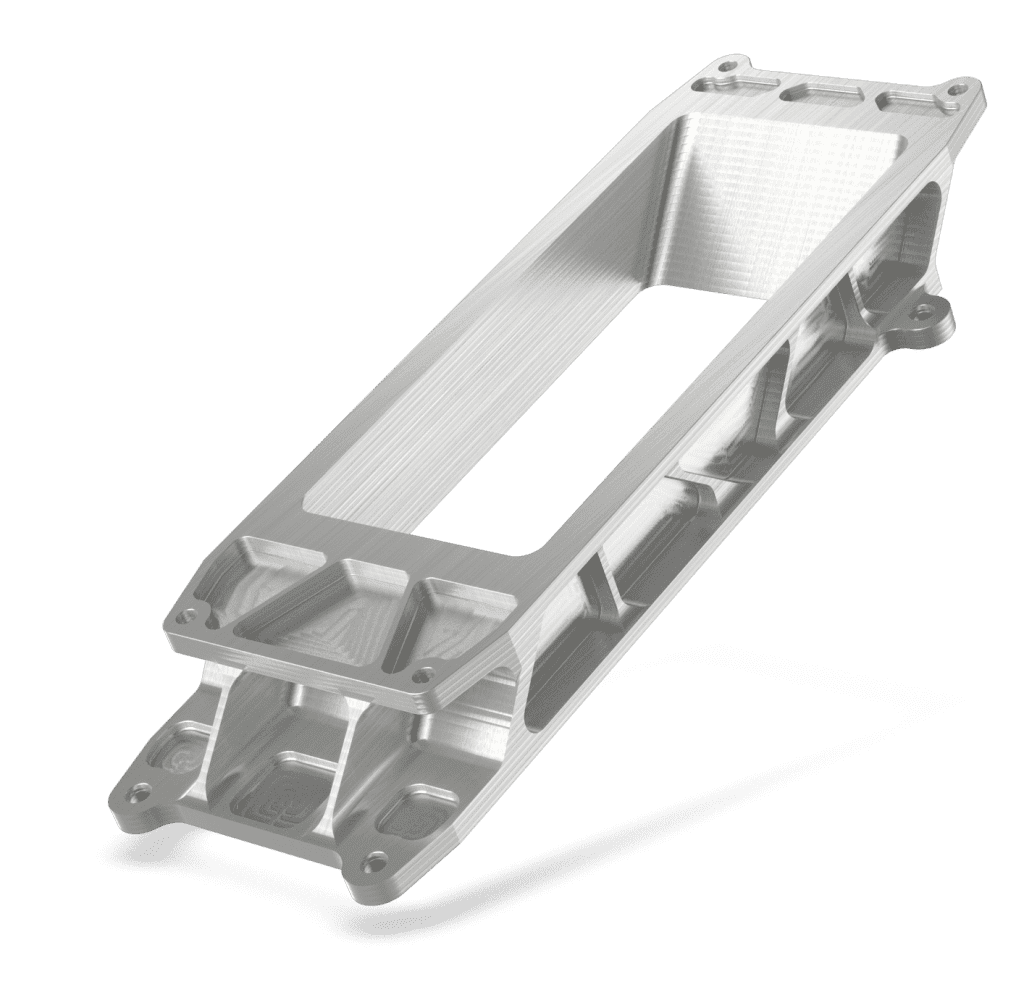
Benefits of CNC Machining
- Convenience
- Accuracy
- Simplifies processes
- Cost-efficient
The complexity and intricacy of high performance engineered parts require a complex and intricate system that is up to the task. CNC Machining capabilities such as those Get It Made can provide are widespread, and have been specifically designed to cope with the demand for high precision products.
Industries that regularly utilise CNC Machining on a daily basis:
- Medical industry
- Aerospace industry
- Transportation industry
- Oil and gas industry
- Military and defence industry
- Electronics industry
- Marine industry
- Subsea industry
What materials can you use?
CNC machining can use plenty of materials – as long as the materials themselves are of a certain strength to withstand the process.
Selecting the correct material is crucial.
Almost all materials can be CNC machined; the most common examples include:
- Metals such as aluminium, steel alloys, stainless steel and brass
- Plastics such as ABS, polycarbonate, nylon, POM and PEEK.
There are some restrictions, including a minimum wall thickness and maximum aspect ratio for some designs, as the material must be able to withstand the pressure and, at times, vibrations of the cutting tools during the crafting process.
What is the process of CNC Machining?
In general, CNC machining can be split into three core steps:
- Engineers designing a CAD model of a part
- The machinist turning this CAD file into a CNC program, setting up the machine
- CNC program then relays the various steps to the CNC machine, which, with little supervision, creates the part.
This system of delivery is part of the reason why CNC machining is so popular, as there is little room for human error, as we touched on earlier. Relying on computer-aided design can ensure maximum accuracy – digital manufacturing, however, can have its limitations (which we will discuss below).
Types of CNC machining
CNC Machining can be broken into various types, including:
- CNC Milling
- CNC Turning
- CNC 5 Axis machining (multi-axis)
CNC Milling
With CNC Milling, the workpiece is held stationary on the machine bed and held in place via a vice. The process of subtractive machining technology then works by the material being removed from the blank workpiece by cutting tools and drills.
These drills and tools rotate at high speed. Their purpose is to remove material from the workpiece using instructions originating from the CAD design in the early stages of development.
These tools are attached to a spindle and, in the case of CNC Milling, move along a three linear axis.
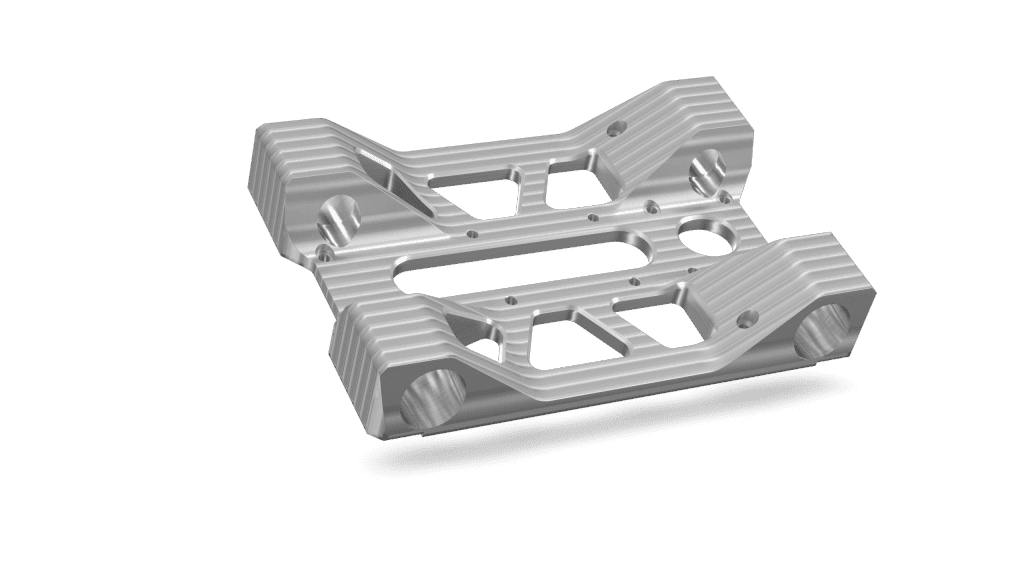
Our beginner's guide on CNC Milling can help you with any specific questions you may have about the process. In a nutshell, however, it is a popular choice for producing industrial products and parts.
There are occasionally limitations to CNC Milling – as there are commonly three axes to work with, there may be areas the cutting tools might not be able to reach. Multiple rotations, extra labour and machining costs will need to be considered at this point.
Parts that require CNC milling will usually be produced if they have simple geometries, which a three-axis machine can comfortably work with. It is easy to program and operate a three-axis milling machine, ensuring excellent accuracy and low cost.
CNC Turning / Lathes
The workpiece is kept in position on the spindle while rotating at high speed. CNC Turning techniques are the lowest cost per unit and are only suitable for part geometrics with rotational symmetry. For example - washers and screws can be mass-produced using CNC lathes.
The works by the bar or workpiece being held on the spindle while rotating at high speed, while the cutting tool or central drill traces the inner/outer perimeter of the part, forming the geometry. The tool does not rotate with CNC Turning and instead moves along polar directions radially and lengthwise.
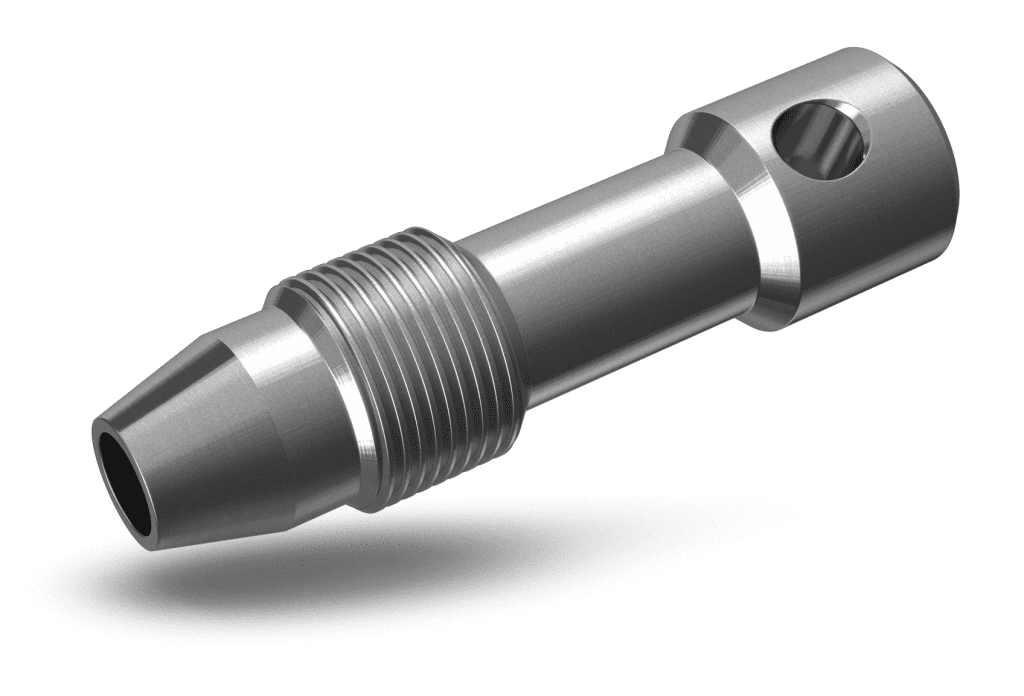
CNC turning is a cost-friendly option if you are mass producing symmetrical parts. CNC lathes are extensively used to produce parts at a much higher rate and lower cost per unit.
Find out about Get It Made’s CNC Turning services here.
CNC 5 Axis machining (multi-axis)
More complicated, intricate designs that may not follow the simple designs of a three-axis CNC milling machine may need a five-axis CNC milling machine. As the name suggests, this machine operates through the use of 5 axes, as opposed to 3. Due to a higher number of axes, more complex design models can be configured.
This does, however, come at a higher cost!
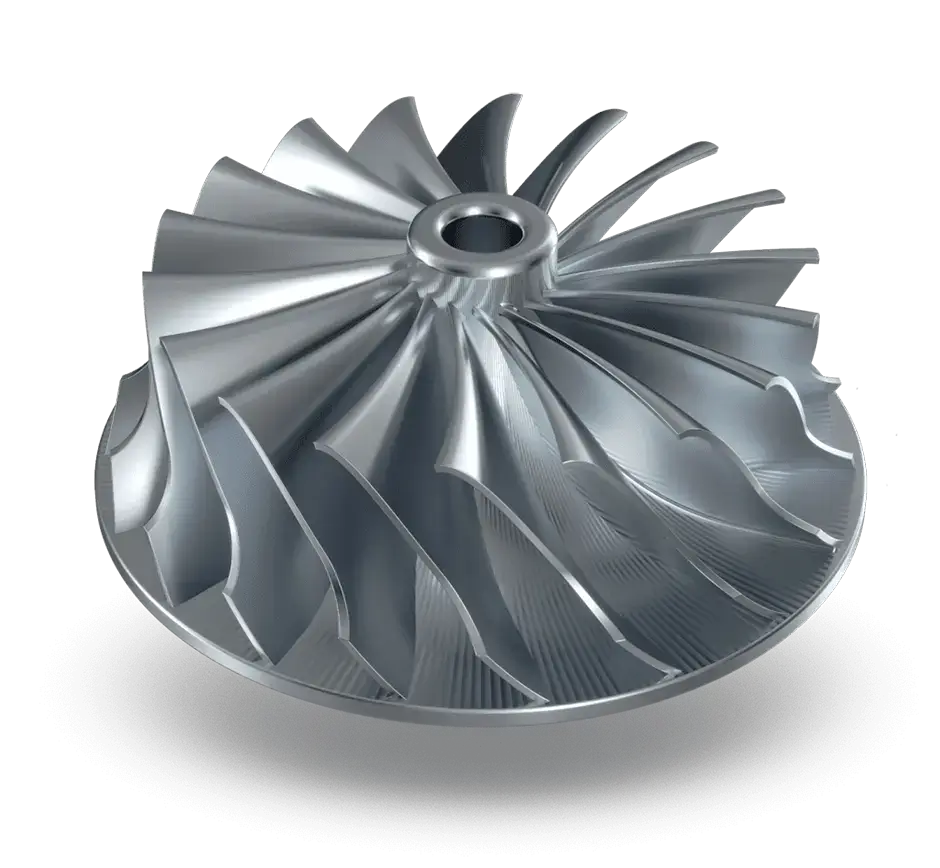
With more freedom and more rotation flexibilities, advanced capabilities can be met. However, specialised machinery and operators may cost you more, so when you are in the CAD stage of your product, aim for your designers to make the vectors as simple as possible. The workpiece can be accessed from a different angle with the 5 Axis model, meaning the machine bed and tool head can also move along with the three access points. Use five Axis Machining for: complex features, organic design and smooth contours.
Check out our CNC machining guide for a deep dive into all types of CNC machining.
What are the limitations of CNC Machining?
Internal hidden geometrics can be problematic, with a limit to the maximum depth of the undercut. Workpieces, too, can deform and vibrate – during production, the cutting forces a temperature change that can result in deformations, meaning that, in some cases, a design may be too intricate for the standard five-axis CNC processes.
Deep cavities, similarly, cannot be easily CNC machined – tools can deflect and vibrate during machining (known as chatter), and with looser tolerances, tool breakage can occur. Additionally, manual repositioning may be needed.
In essence, the geometry of a part determines the way it will be held on the CNC machine, reflecting the number of setups required. Although automation is nowadays considered far more efficient than human processes, the fact that it is automated doesn’t leave a clear path for trickier designs.
Bearing this in mind, when you’re designing a part, you should likely consider:
- Hole depth
- Wall thickness
- Internal radii
- Cut depth
- Type of corner – square corners are more costly as the cutting tools are rounded in shape
Read more about how you can adjust your design to reduce part cost here.
Factors that affect the CNC Machining process
When developing your 2D CAD model, it’s essential to consider factors such as:
- Minimum part thickness
- Maximum part size
- Complexity of internal cavities/features
CNC Machining finishes
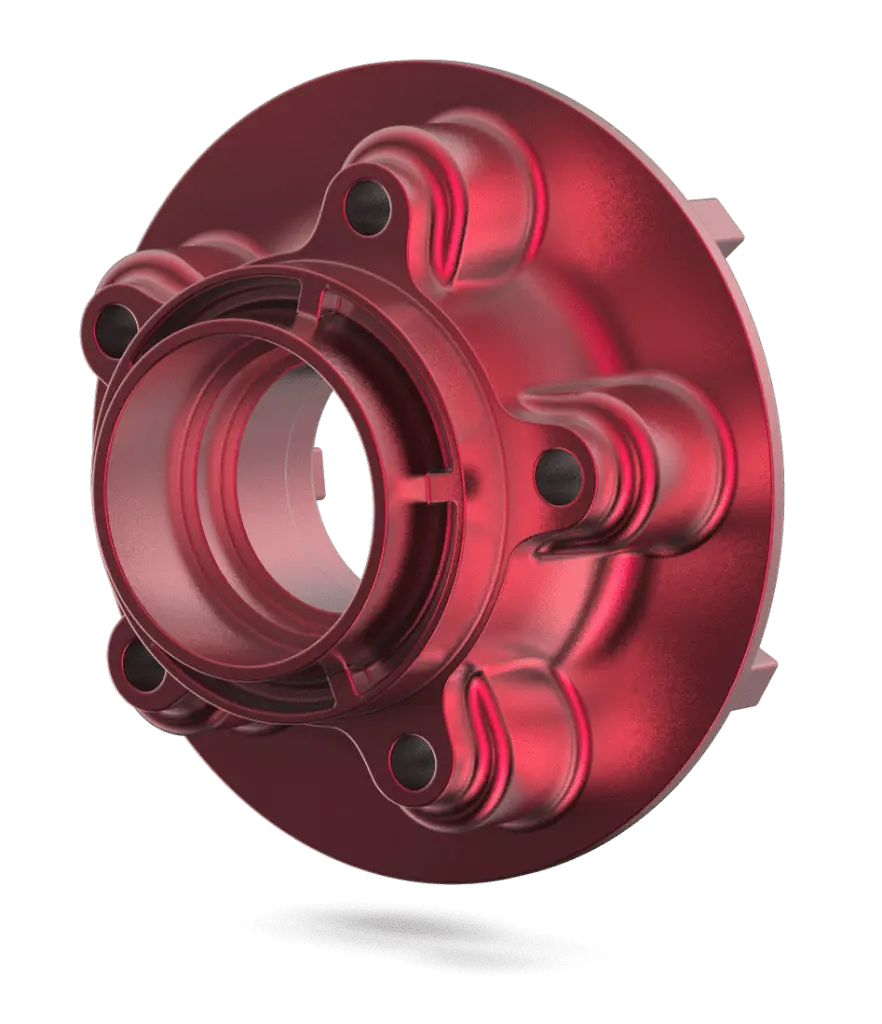
The surface finish is another consideration to make.
Alongside the material itself, there will be different surface finishes, including:
- Grinding
- Polishing
- Bead Blasting
- Electroplating
- Knurling
- Honing
- Anodising
- Chrome Plating
- Powder Coating
Depending on the recipient in the supply chain, be that another supplier, a client, or a customer, the finishing of the part will likely be different. For example, in some cases, factory standard finish will be acceptable. In some cases, a more high-quality finish or coating may be required. This will depend on the industry, as well. Surface finishes will alter factors such as:
- The product’s appearance
- The surface texture
- Roughness/hardness of the finish
- Chemical resistance
Get It Made prototypes and manufactures bespoke parts through CNC Machining, and with every project meticulously planned for efficiency and value. You can contact us today to find out more about who we are, what we do, and how we may be able to help your business.