What is 5 Axis CNC Machining?
Find out what 5 Axis CNC Machining is, and the benefits using 5 Axis CNC Machining for your project.
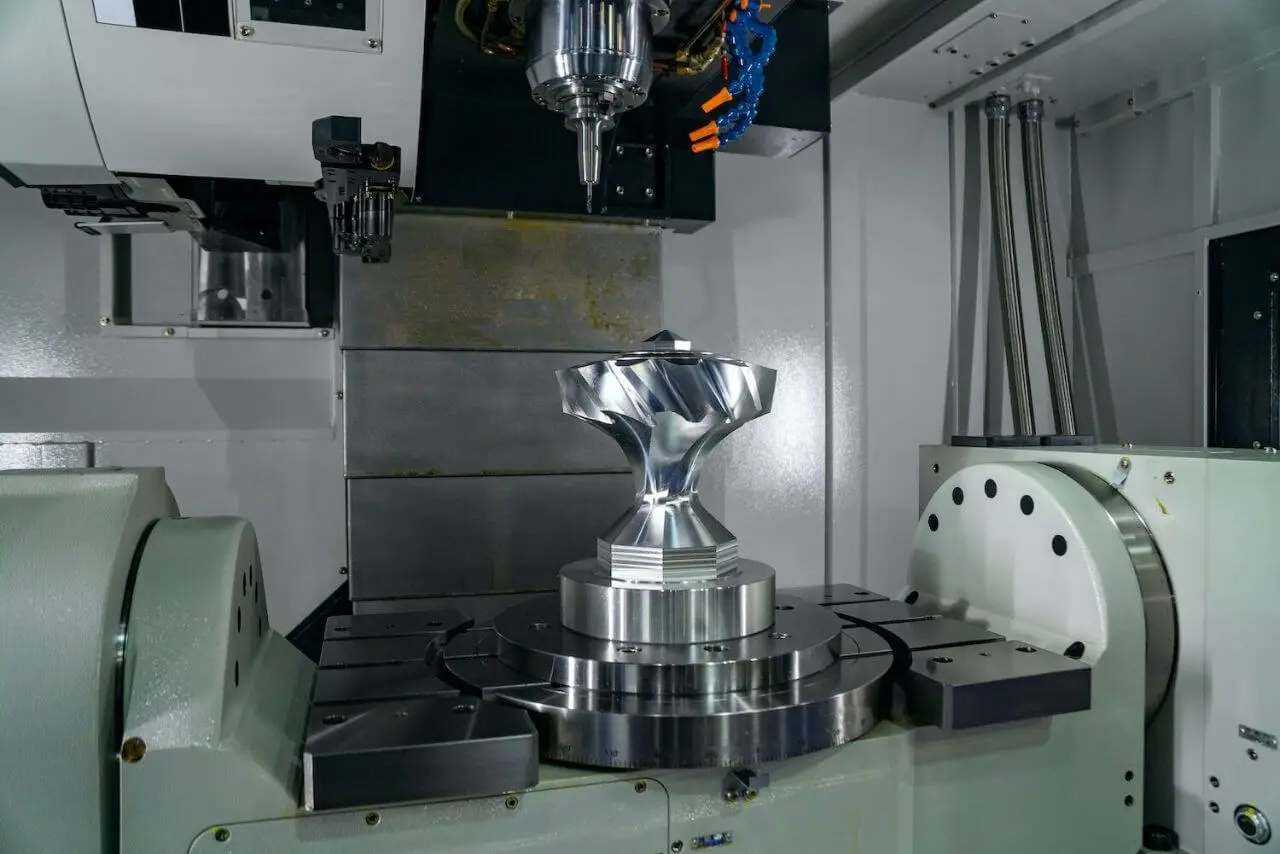
5 Axis CNC Machining is an incredibly versatile machining process that implements subtractive machining technology. Through this process, a workpiece is cut into shape using cutting tools working on five axes to deliver a final part. CNC machining is incredibly popular due to its high accuracy, efficiency and repeatability. The process starts by utilising the original Computer-Aided Design (CAD) file to help program cutting tool paths, all managed via Computer Numerical Control (CNC). Once these tool parts have been programmed into a language that CNC machines understand, the process can be entirely automated, meaning there are minimal manual processes.
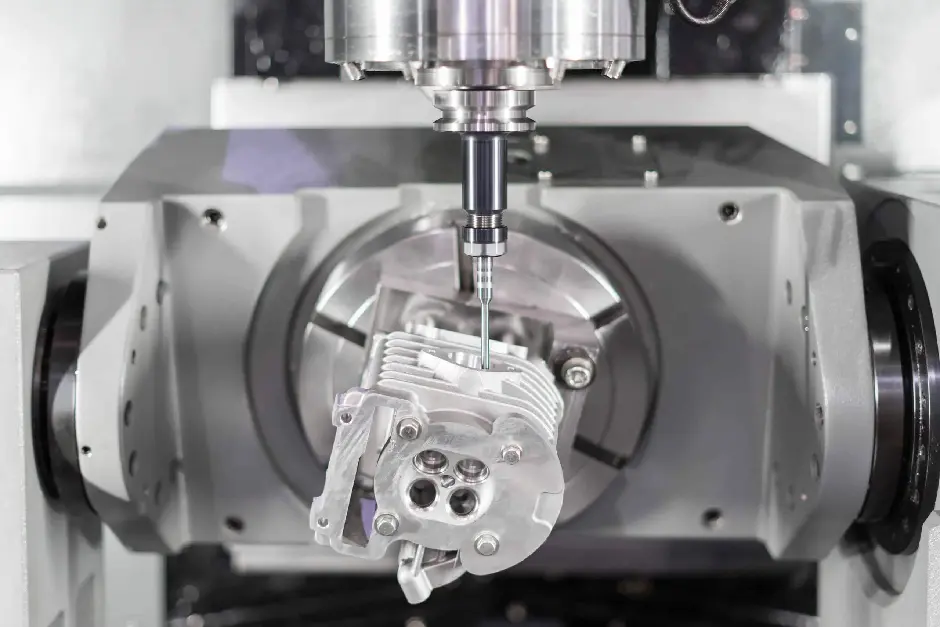
This article highlights the features of 5 axis CNC Machining and why it differs from 3-axis or 2-axis machining and notes the benefits of using a 5 axis CNC machine.
Due to the increased number of axes, five-axis milling machines have greater capabilities than their three and two axes counterparts. The machines can be configured in such a way as to reduce the need for constant supervision. Efficiency and single set-up for manufactured parts are the main reasons why industries choose to implement 5 Axis CNC machining.
{{cta-banner}}
How does 5 axis CNC machining work?
In CNC machining, a part is formed using cutting tools and subtractive machining technology, which cuts away at the workpiece to create the desired shape. The shape is predetermined by the original CAD (Computer-Aided Design) file. A program is then produced in G-Code format, which feeds instructions directly to the CNC machine.
Currently, it is most common for CNC Milling machines to have three axes to work from, X, Y and Z. However, 5 axis CNC machines use further axes, to implement into the cutting process from additional angles, giving greater scope for more complicated and intricate designs. So, axes A, B, and C can be introduced.
These axes work alongside X, Y and Z in rotational angles to deliver a 5 axis cutting machine capable of intricate designs while remaining a very high quality to the finished piece. The A, B and C axes move independently to the X, Y and Z in a rotating fashion. The specific configuration of the machine or CAD design determines which two of the three additional rotational axes are used. This 5-axis configuration comes at a higher cost due to the higher levels of calibration and automation technology needed to run the CNC machine and input the commands.
In terms of precision engineering technology, 5 axis machining can offer the best precision engineering solutions, and it is an industry-leading engineering process within the automotive, aerospace and medical industries, to name a few.
5 Axis machining configurations
The three axes X, Y and Z work in the same fashion and calibration as a 3-axis CNC machine. The movement of the additional two axes working within five-axis machining is always controlled by the CNC program inputting the instructions to the machine.
There are fundamentally two styles of CNC machining that operate with 5 axis:
Trunnion style
A Trunnion style 5 Axis machine operates with an A-axis rotating about the X-axis, and a C-axis rotating around the Z-axis. The rotary axes are expressed via the movement of the table. This type is more suited to larger work volumes, as there is no need to compensate for the space taken up by the swivelling handle.
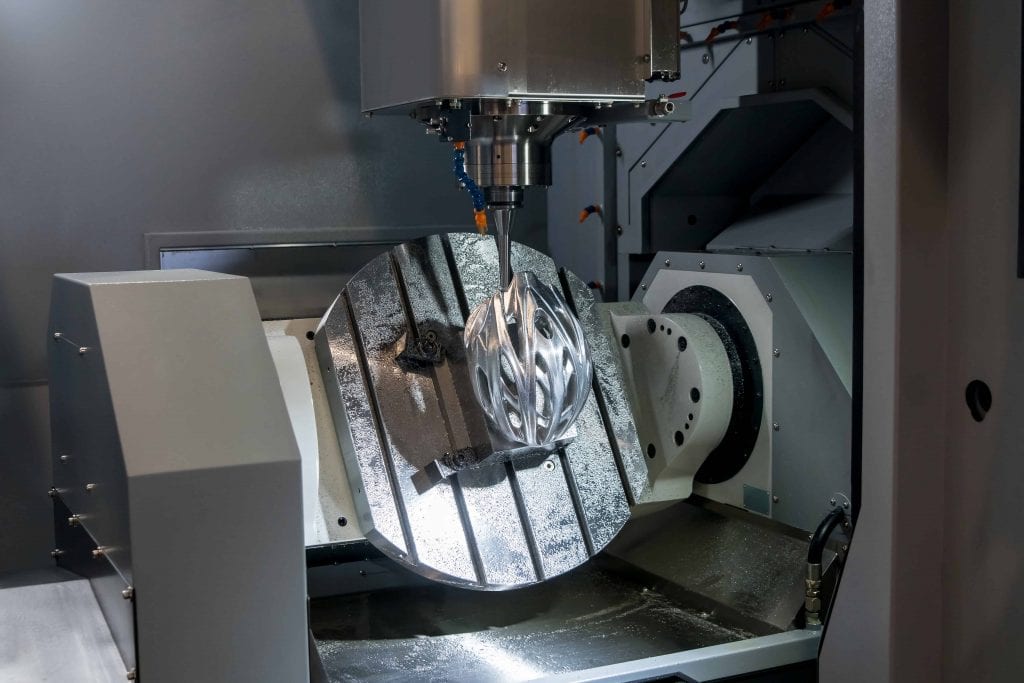
Swivel rotate style
A swivel rotates style 5-Axis machine operates with a B axis rotating around the Y-axis, and a C-axis rotating about the Z-axis. It differs in that the table is always horizontal during the cutting process, meaning it can support heavier parts. The rotary axes are expressed by the swivelling cutting arm.
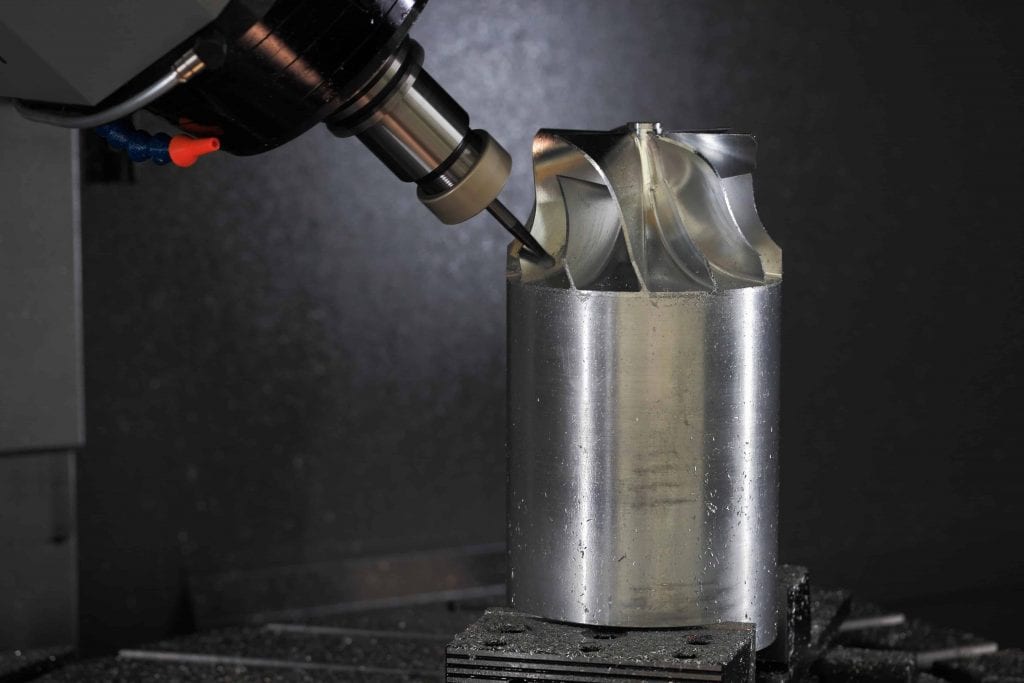
How much does 5 axis CNC machining cost?
The cost depends on the project at hand and the volume of parts being produced. Beyond the higher cost of purchasing a 5 axis machine, 5 axis CNC machining requires more significant set-up levels before the production of a component can begin. This higher initial set-up cost during preproduction can make low volumes or one-off more expensive than equivalent parts produced on a 3-axis machine.
This is understandable as 5 axis machines are by their very nature more complex and dynamic than other types of CNC machines with fewer axes. 5-axis milling machines are also more time-efficient, as they are calibrated to complete parts without any need for intervention. Usually, only one operation is needed to complete the workpiece, so downtime is dramatically reduced. Fixturing requirements are reduced, which is mainly beneficial to more organic, complex parts.
Why is there less fixturing with 5 axis CNC machining?
The range of motion achievable from the cutting head & extra rotational axes means that these machines can reach five sides of a part. For example, if a geometrically complex part were needed for aerospace, a five-axis CNC machine would be the most capable machine to achieve this. This is due to its ability to reach complex angles and cut areas hard to get, such as a compound curve.
Benefits of 5 Axis CNC machining
High-quality finish
Due to the advanced capabilities of a cutting tool working with five axes, a higher quality finish is achievable, as the cutting tools can be shorter on a 5 axis CNC machine. This reduces the vibration of the tool and as a result, reduces the chance of “chatter” marks and ensures a smoother surface finish on the final part. The time-consuming and costly need for hand finishing can be almost entirely eradicated, as 5 axis machines can closely follow contoured geometry that is traditionally harder to machine.
Faster output
Due to the high speed of 5 axis machining and increased automation, there is little need for intervention or manual processes. This is commonly known as “done in one” and “one-hit machining”. The multiple axes mean the whole workpiece can be cut in one go instead of the need for several operations to complete the final piece. This, in turn, results in faster output capacity.
More complex shapes can be produced
5 axis CNC Machining can produce very complex geometries. For example, machining castings and parts that include many different features would, in the past, require a multitude of set-ups to machine and finish the desired shape. However, with a single set-up, 5 axis machining can complete a piece to its exact requirements with only one fixture in most cases.
For further information about 5 Axis CNC Machining and how it could benefit your business, contact us today. With years of expertise, we will get back to you within 24 hours with a detailed and concise quote regarding your requirements. From the first contact to the safe delivery of components and fast lead times, Get It Made have got you covered.
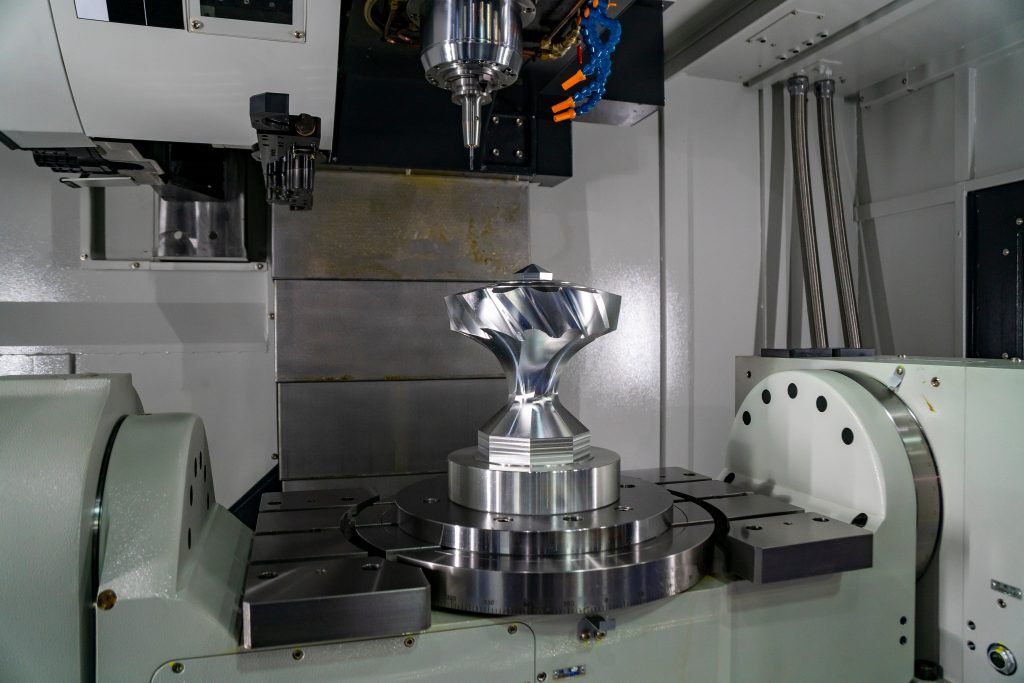