Process of Injection Moulding
Learn more about Injection Moulding in our guide to the process. Discover the anatomy of an Injection Moulding machine and the different types of moulding available.
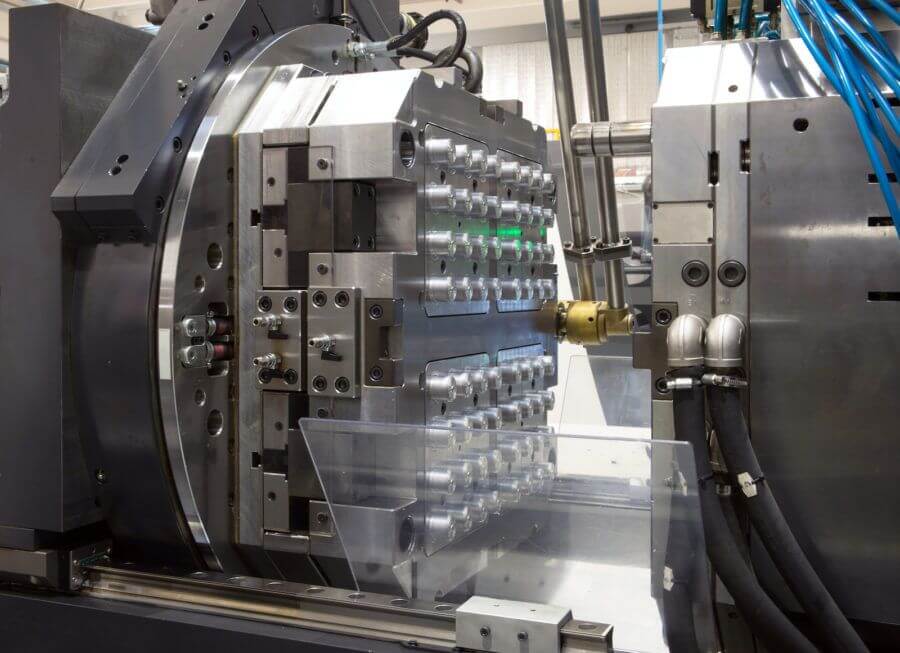
Injection moulding is a popular manufacturing process and is the go-to choice for many industries to mass-produce everyday products.
This article defines the process of injection moulding, providing details on how it works and why it is such a popular choice for so many businesses and industries.
At Get It Made, Injection Moulding is just one of the services we offer. You can find out more about our range of CNC Machining services here.
What is Injection Moulding?
Injection moulding is a prominent manufacturing process used predominately to manufacture high volume plastic parts. Injection moulding can produce parts and products of various materials, however, most commonly, it’s used to produce thermoplastic polymers and thermosetting polymers.
{{cta-banner}}
What is injection moulding used for?
Injection moulded parts can be found in most industries and consumer plastic products. Common uses for injection moulding include:
- Packaging
- Toys
- Medical equipment
- Electrical appliances
- Agricultural items
- Automotive parts
- Lighting components
- Telecoms equipment
Injection moulding is used for industries where high volume and low customisation is required.
How does injection moulding work?
Once a part is designed, a metal mould is precision machined to create the desired part shape. This can have a single cavity for the molten plastic to fill, or multiple cavities. This decision is primarily based on the economics of the mould and the volume of parts required. Increased cavities mean more parts can be produced per cycle, but the mould is more expensive.
- The chosen material is fed through a heated chamber. This melts the material before it enters the hollow mould.
- After the cavity is filled, the machine exerts additional pressure to account for any plastic expansion upon cooling.
- The part often cools incredibly quickly and solidifies into the moulded shape.
- Once the part solidifies, it’s ejected from the mould through the use of ejector pins or via a manual process.
The process of injection moulding itself is a relatively simple one. However, several complex steps ensure that the final product is precise and of the required quality, finish, and design.
The exact type of machine used is dependent on the type of part being moulded and the material being used. Larger parts, for example, will need machines that can exert a higher clamping force and more powerful injection pressure.
Thermoplastics are usually the preferred material because of their desirable qualities:
- Recyclability - they can be melted and moulded into a new product.
- Versatile properties with Polyethylene, Polypropylene and Polyvinyl Chloride.
- Protection from electrostatic discharge.
Thermosets and elastomers can also be used for injection moulding, although these are not as widely used.
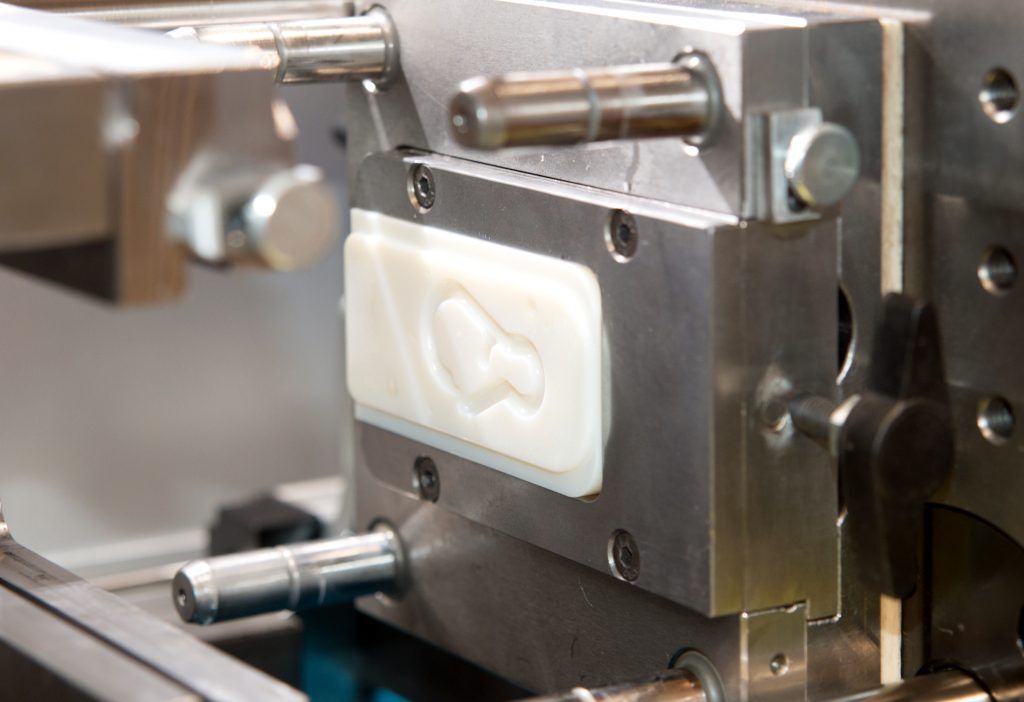
Injection Moulding Machine Moulds
The moulds can be fastened in either horizontal or vertical positions, with requirements depending on the size and type of application.
There are various types of moulding machines, and these are classified by the driving systems they use. These could be:
- Mechanical
- Hydraulic
- Electric
- Hybrid
Cold and hot runner sections can be selected for carrying plastic into the mould cavities. Hot runner systems slow the rate of cooling of the molten plastic when entering the mould. This has the benefit of better mould fill, however, it comes at a higher cost.
Smaller plastic injections offer more accuracy and are better for relatively small components. The size of the injection unit determines the size and physical characteristics of the machine, including the choice of injection screw diameters. The larger the diameter of the screw that is fitted, the larger the maximum shot weight of plastics that can be generated.
Injection moulding process step by step
Clamping
The two moulds must be securely closed by the clamping unit, with sufficient force applied to keep the mould securely closed while the material is injected. Metal plates are used to clamp the mould together.
Injection
Molten thermoplastic material is injected into the mould, with pressure & heat applied to heat the pellets in the barrel until they melt to liquid form.
Dwelling
Once molten plastic is injected into the mould, more pressure is exerted. This is to ensure that every cavity in the mould is filled. This process uses hydraulic and mechanical pressure.
Cooling
The plastic is left to cool & solidify in the mould. This process is rapid, with the molten plastic cooling as soon as it comes into contact with the inner surfaces of the mould.
Opening
Once cooled sufficiently, the mould's moveable metal plates are separated to reveal the final finished product.
Ejection
The final cooled product is ejected from the mould via the ejection system attached to the rear half of the mould. It involves using rods and sometimes an air blast to remove the plastic component from the mould.
What are the advantages of injection moulding?
Injection moulding is a preferred process due to the fact it is:
- Cost-effective for high volume
- Part quality is easy to determine
- Reliable
- Efficient
- Quality assured
The actual moulding process is very quick compared to other methods, so plastic moulding is preferred for mass-produced products.
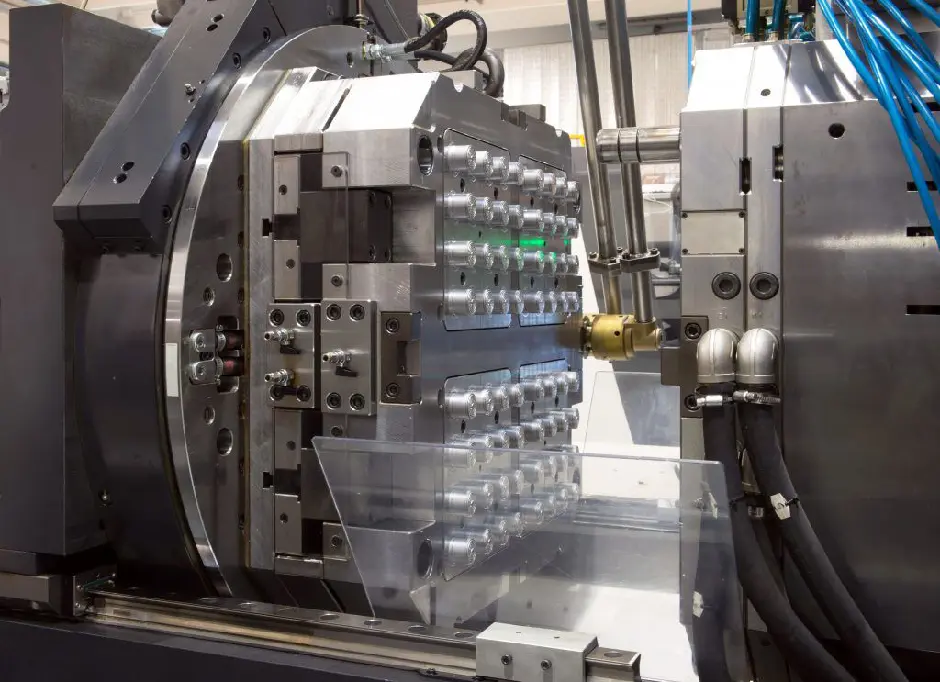
Why is Injection moulding used in mass production?
As plastic injection moulding is an automated process, with most of the actions carried out by machines and robotics, they require a sole operator. They often run unattended for hours at a time. Understandably this results in reduced costs, and there is also little post-production with plastic moulding. With parts having more or less a finished appearance after they are ejected from the mould, the injection moulding process is preferred for mass production due to its reliability.
Although the initial tool can be an investment to design and manufacture, the process is extremely cost-effective once this tool is complete. The errorless mould can be used repeatedly and yield the same consistent results, which is why this manufacturing method is used to make so many products we know and use every day.
The only slight disadvantage to injection moulding is the upfront cost of the mould design. Depending on its intricacy, it may require extensive design, testing, adjustments, and therefore longer lead times.
Types of injection moulding
Thermoplastic Injection Moulding
Thermoplastic Injection Moulding is where a thermoplastic polymer is used in injection moulding. The process involves the plastic material changing to a liquid state, and unlike thermoset plastics, which cool permanently into a solid, thermoplastics can be remelted once they’ve cooled.
Insert Moulding
Insert moulding is an injection moulding process that sees two or more components combined to form a single finished product. Insert moulding involves inserting a component into the mould cavity prior to the injection, with the melted plastic filling the mould around the insert. This technique is used to add strength to a product. It can also come in handy as it can be used as an alternative method to reduce product weight or increase its strength.
Overmoulding
Overmoulding, or two-shot moulding, sees the injection mould covered with another substance such as rubber. This makes the final product more durable, and a popular choice of material for over-moulding is TPE (Thermoplastic Elastomer). In practice, a good example of over-moulding is the flexible rubber parts commonly found on toothbrushes. Additionally, over-moulding can combine products that are comprised of multiple components.
For more information about how we can help with your project, contact us today or click here for a quote.