CNC Machining for the Robotics Industry
Get It Made produce many CNC parts for robotic applications. This month's industry insight focuses on how CNC Machining can be used within the Robotics Industry.
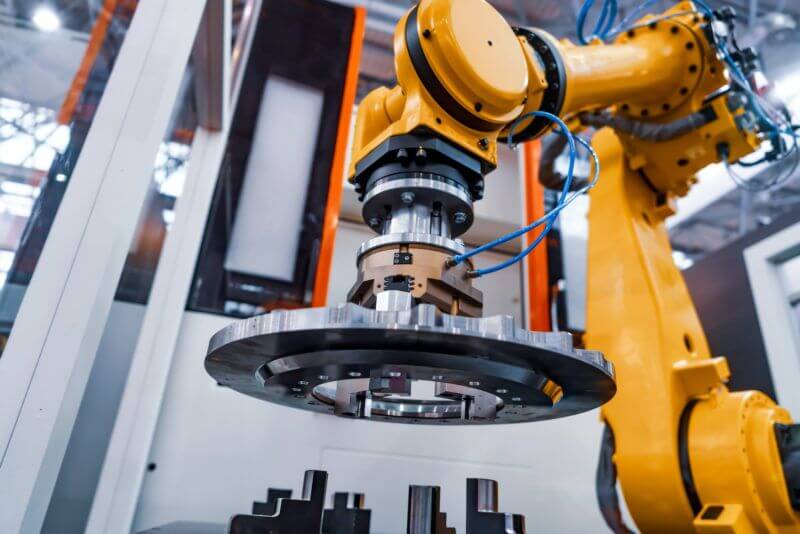
The role that CNC Machining plays alongside robotics is vital. Robotic machining and CNC machining often overlap, however, the lines are increasingly blurred; CNC Machining benefits from the implementation of robotics. Furthermore, both CNC Machining and Robotics are seen as leaders in providing industrial automation solutions.
What is CNC Robotics?
CNC robotics can refer to any additional robotic processes that aid the process of CNC (Computer Numerical Control) Machining.
A leading process in the automation of manufacturing, CNC Machining is extremely popular when it comes to mass-producing and delivering high-quality parts and products for various industries. This includes the medical industry and aerospace industry, and the robotics sector.
Not only can CNC machines benefit from the implementation of robotics, but robotic parts themselves can also be manufactured through CNC machining. This article focuses on how robots can be used to improve CNC machines, as well as commenting on how CNC Machines can assist in the manufacturing of robotic components.
{{cta-banner}}
Producing CNC Parts for the Robotics Industry
CNC Machining is regularly used to produce bespoke parts for the robotic industry. Often robotic applications are highly tailored to their use case. This makes CNC Machining the ideal manufacturing option due to economically unique parts at low volumes. Examples of where CNC Machining can be used to produce robotics parts include:
- Robotic End Effectors
- Custom Jigs and Fixtures
- Material/Part handling and storage
Why is CNC Machining the best process for producing Robotic parts?
In addition to the economic benefits of using CNC Machining to produce custom parts over other moulding or additive processes, there are several important reasons why CNC machining is the process of choice.
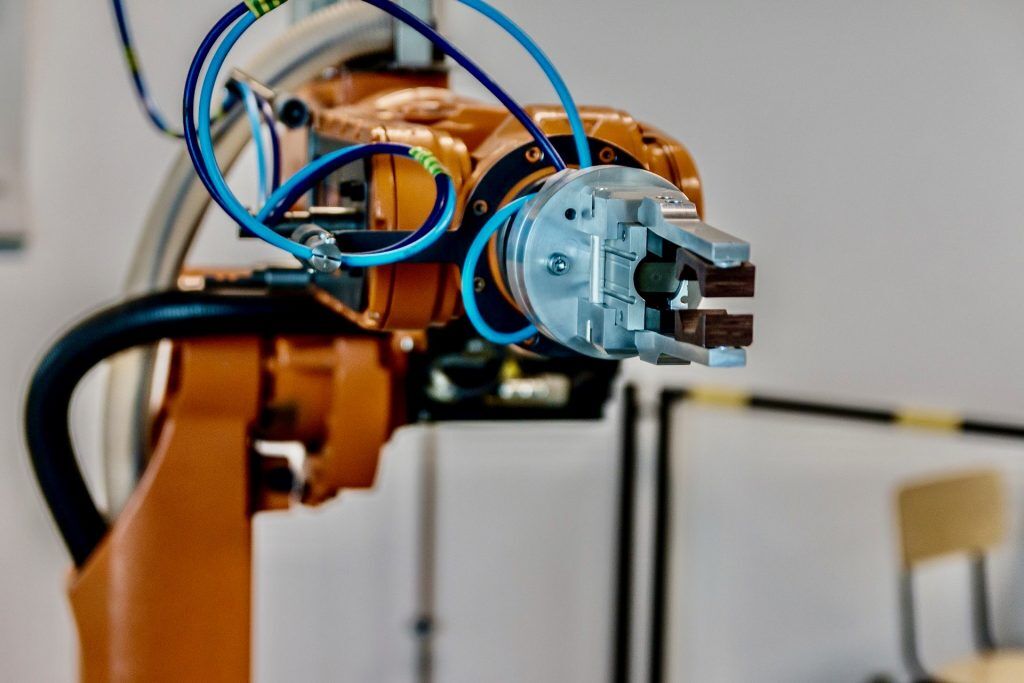
Firstly, lead times for CNC machined parts are comparatively lower than many other processes. Design to the final part can take as little as a few hours. This allows for the rapid iteration and refinement required by many custom robotic applications.
Secondly, dimensional accuracy is vital in robotics. Robots often work between fixed points in space and can’t accept large deviations in dimensional accuracy. At Get It Made, we offer CNC Machining to a standard tolerance of ±0.05mm, and higher tolerances on request. This is crucial for applications that demand precise and highly repeatable movements.
Finally, CNC Machining allows for the surface finish to be controlled precisely. In many robotic cases where gripping or suction is required, part flatness and surface roughness are critical properties. CNC Machining can produce parts to a surface roughness of Ra 0.8μm and even lower with additional finishing processes.
What materials are used for Robotic parts?
Firstly, parts for robotic applications often have a requirement to be strong, tough and lightweight. Materials such as aluminium have ideal characteristics and can easily be machined using CNC Machining.
Similarly, POM (also known as Delrin and Acetal) is commonly used for robotic parts. Easy to machine, it is known for its low friction, high stiffness and superior dimensional stability. As a low-cost plastic, it is also a very economical option.
Can Robots be used for CNC Machining?
CNC machines and robots differ slightly in terms of their core functions. Both are similar in that they can be coded to perform a specific task, but the complexity and variation of the particular task are where the key differences come in. CNC machines are highly specialised to manufacture a specific type of part, a set finished product. Robots are generally very versatile and are easily adapted to perform different functions.
Nowadays, it is widely acknowledged that, although growing in popularity, CNC Robots will never fully replace CNC Machines. A significant factor that will prevent robots from advancing or becoming more prominent than CNC machines is that robots tend to be less robust. There are technical challenges when it comes to the hardness of machined materials, with CNC machines and their various types (Cutting, drilling, turning) aided with the ability to withstand large amounts of pressure, speed and heavy materials.
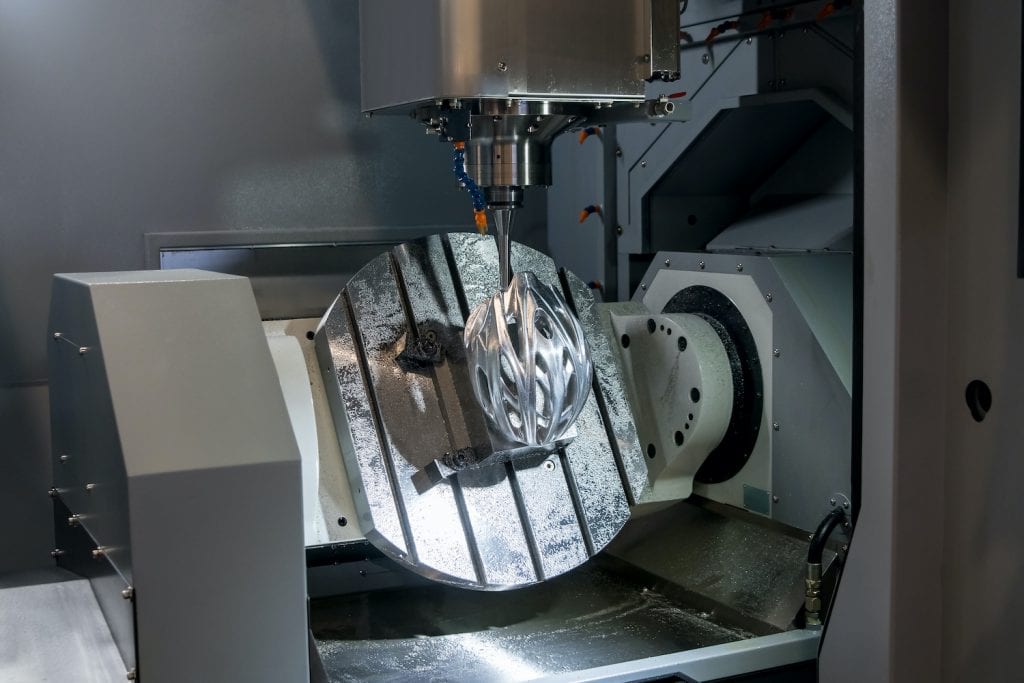
Depending on the complexity of the final part and surface finish required, robotic machining can be seen as a viable alternative. However, it will not replace CNC Machining for 3-4 axis applications. Instead, an addition such as a robotic arm, for example, can help to simplify processes.
It would achieve this by:
- Performing pick and place operations
- Move parts from one machine to another
- Being able to use additional 5th and 6th axes
Essentially, robots can be utilised to replace operator-led processes that increase lead time and costs. The human factor is always a consideration in automated machining & manufacturing, as the more human intervention, the increased chance for error and safety concerns.
How Robots Can Aid CNC machining
Generally speaking, the software can help ensure that the industrial robot will operate efficiently and safely, aiding in completing automated tasks. Hand finishing tasks, in particular, can now be completed by CNC robotic systems. Industrial robots with variants of 5 axis milling capabilities can efficiently perform polishing operations, a process that could otherwise require hand finishing.
A CNC machine completes Semi-automated production steps in some instances, however, some steps can only be performed by human or robot operators. Robots can now complete tasks such as:
- Loading raw material into the machine
- Controlling the process
- Unloading finished parts
- Controlling product quality with automated quality inspection
A robotic operator or robotic CNC arm can load any CNC machine. It can control the whole process, unloading the machine after it has finished the task or checking and packing the final product. A robotic operator can even move parts from one machine to another safely, precisely and repeatedly to a time-efficient standard.
Milling
A robotic arm can be used automatically by communicating with the CNC machine when aiding milling. The positioning accuracy of a robot results in a high quality finished product. One of the biggest time consumers in the milling process involves positioning the workpiece and changing the machine tool. An operator must do this manually, whereas a robotic arm can be installed to perform this task automatically by communicating with the CNC machine. The positioning accuracy of utilising a robot results in a high quality finished part.
Welding
An operator can face potential hazards such as gases, fumes, fire and exhaustion from repetitive tasks. Replacing a human operator with a CNC robot welding machine will allow the manufacturer to increase positioning accuracy and reach long-lasting results. With a reduction in labour costs and a decreased chance of accidents or hazards, it's understandable why manufacturers may implement robots to assist in the welding process.
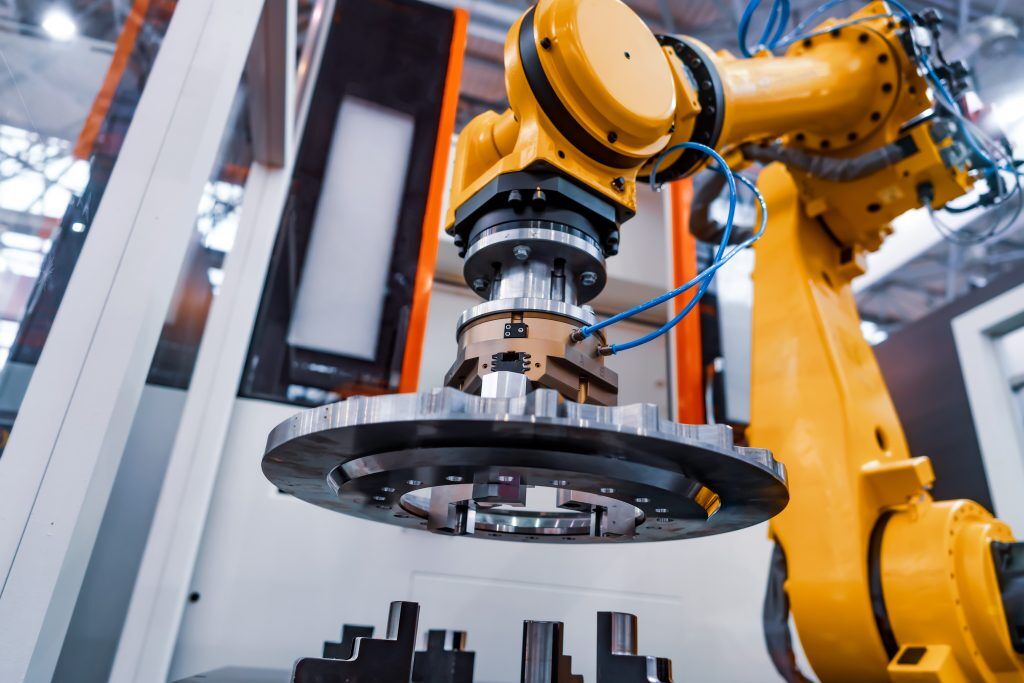
Differences between robots and CNC Machines
CNC machines are widely accepted as producing more accurate results than robots. Robot accuracies can be improved by calibration; however, the accuracies of CNC machining can be fractions of a micron, as opposed to robots, the accuracies of which are acknowledged as 100s of a micron.
The stiffness of axes is another key difference between CNC machines and robots. CNC machines have a higher stiffness in all axes, for more robust manufacturing, as opposed to robots that have a lower stiffness.
Technical advancements in recent years in Computer-Aided Design have led to a new approach to CNC machining, which enables a broader adoption for robots to be implemented in aiding the finishing or machining applications.
Spindle manufacturers, for example, a crucial part of CNC machines, are now providing high speed motorised spindles that are specifically designed for robotic machining, which features:
- Lightweight construction (to minimise payload stress)
- Minimised risk of contamination threats due to advanced sealing
- Ability to operate at multiple orientations and angles
Robots offer the following characteristics, which is why they are seen as aiding the CNC machining process:
- Efficiency
- Speed
- Accuracy
- Safety
- Versatility
For more information on how CNC machining can be used within the robotics industry, or to discover Get It Made’s range of CNC machining services, get a quote today or contact us.