CNC Machining for the Aerospace Industry
In general, CNC Machining is trusted to mass-produce various products and parts for a wide variety of industries. Thanks to the advent of CAD/CAM (Computer-Aided Design & Manufacture), the cost of human error is vastly reduced. CNC machines follow instructions, known as G-Code, generated by CNC programs. This allows parts to be manufactured precisely to the 3D CAD file design.
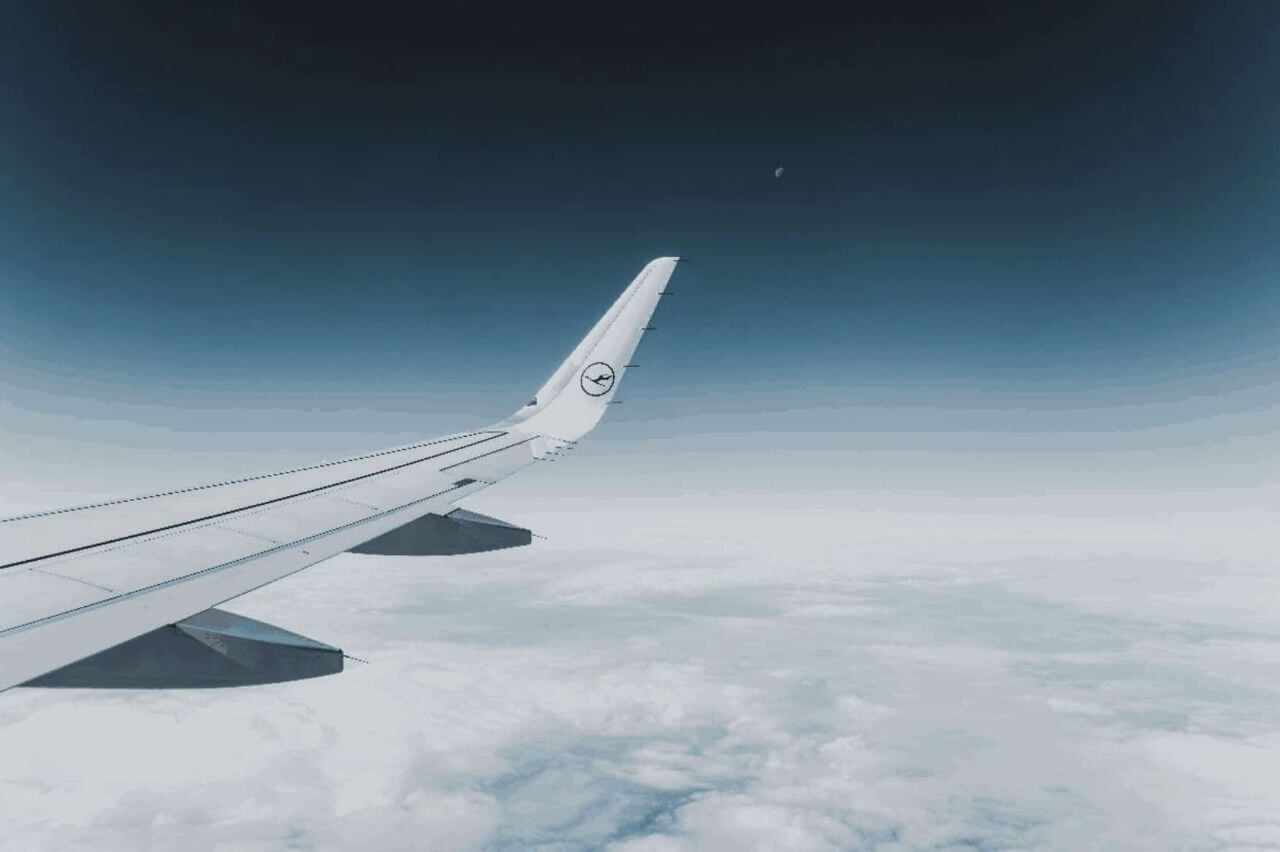
Aerospace Engineering is a type of engineering with little room for error – the very nature of aerospace engineering requires utmost accuracy, accountability and efficiency. Many aerospace parts are tested, configured and produced using CNC Machining.
What is CNC Machining?
CNC Machining is the process whereby machine-driven cutting tools create products through subtractive machining technology. By cutting away at the workpiece, or blank, complex designs can be produced on a mass scale with high precision. What’s more, there is little room for human error as all input, and machine-led processes are controlled by a computer-aided design system.
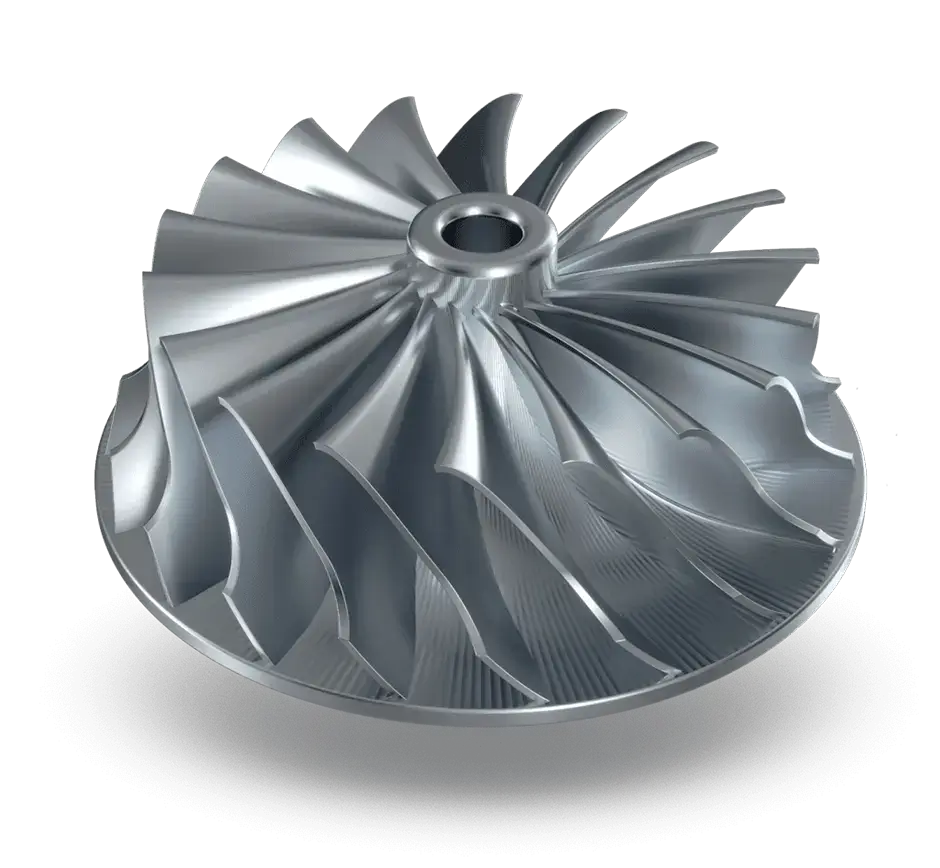
Ways CNC Machine Can be Used in the Aerospace Industry Sector
Utmost precision is ideally met with every engineering project, and component or part created. This is a particularly pressing concern regarding aerospace components – when dealing with flight. Accuracy is everything – every single component of a plane will require precision and accuracy to ensure safety and assurance in flight.
You can find out more about Get It Made’s CNC Machining services for aerospace here.
{{cta-banner}}
AS9100 standard
Those in the aerospace industry will be aware of the importance of conforming to a certain standard, namely, AS9100. This refers to the internationally recognised aerospace standard for quality management systems.
It is modified explicitly for aerospace companies and is a set of guidelines for managing, controlling and auditing processes. You can read up on AS9100 to gain more understanding of why it’s so important. If you require AS9100 Rev D compliance, Get It Made can support you through our Aerospace manufacturing partners in the UK, Czech Republic and China.
What are the main features of CNC Milling for aerospace?
- High precision manufacturing
- Variety of parts and complexity
- Lightweight materials of high strength
Advantages of CNC Machining?
Considerations need to be made for aerospace parts and structures, be that for everyday air travel, space aviation or the defence industry. When considering spacecraft in particular, longevity and precision will need to be considered – often, the aircraft is in flight for long periods of time, sometimes years.
- High accuracy, precision engineering
- No room for human error due to automation processes
- Ability to manufacture complex geometries
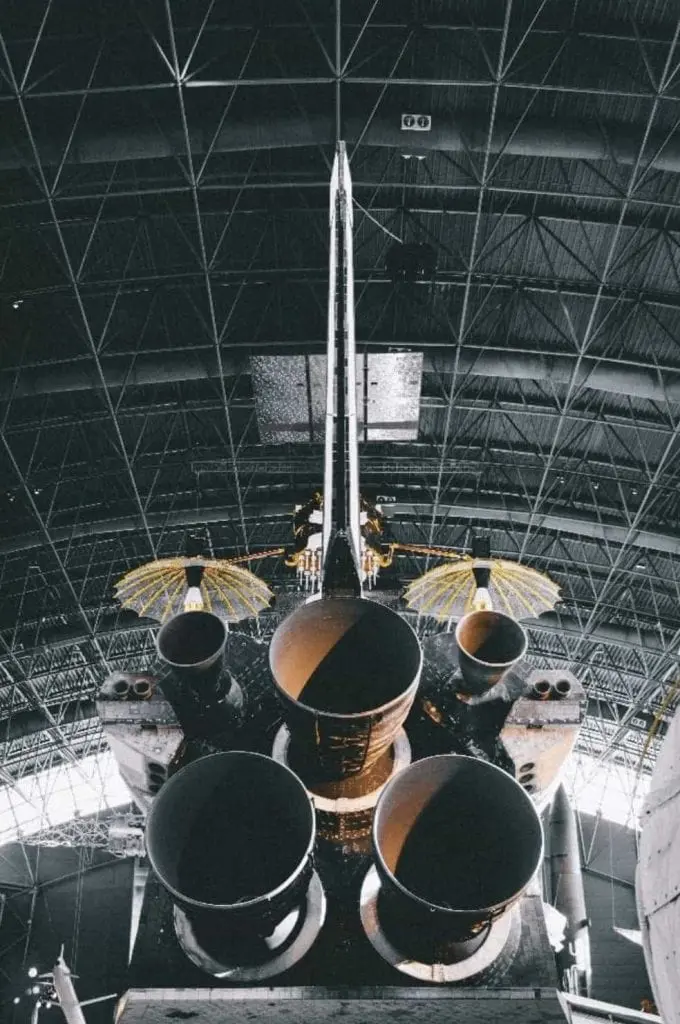
This means that every component needs utmost precision and no room for error. This is where CNC Machining comes into play. CNC machining for aerospace parts has paved the way for more accurate and cost-efficient results than ever before. With such an array of parts, components, structures that all require varying levels of machining, moulding, and additive manufacturing, automated manufacturing has become increasingly popular. The Boeing 747, for example, is made up of 6 million separate parts.
Aerospace Milling with 5 Axis CNC
Considering the complexity and variation of aerospace parts, it makes sense that many aerospace parts are configured using 5 Axis CNC machines.
The machine set-up allows for complex geometries. As space travel and aerospace are ever-evolving industries, the machine set-up allows for continuous adaptation and reconfiguration of parts.
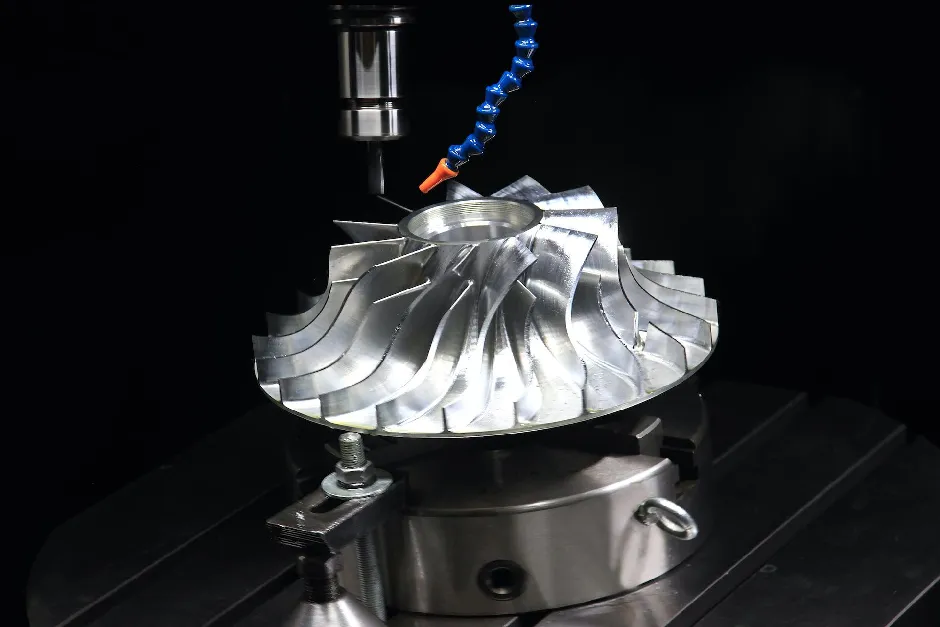
In a nutshell, five-axis CNC machining copes better with the scope and technicality of aerospace components so they can be milled, drilled or manufactured to the specifications of the individual aircraft. Additionally, 5 Axis CNC Machining can easily suit the rigorous, high-performance demands of the aerospace industry. This is in comparison to its three-axis and four-axis counterparts, which would meet limitations when it comes to design and geometry.
You can read up on CNC Milling here as we touch on it in our Get It Made blog.
Materials used in aerospace CNC Machining
In general, the preferred metals for aerospace are either titanium or aluminium and, increasingly, carbon fibre.
One of the critical considerations for any aircraft? Weight. The lighter the aircraft, the more fuel-efficient the aircraft is, therefore, more cost-efficient. Of course, as well as being lightweight, aircraft also need to be safe to fly. Therefore, metals of high strength but low weight are best.
Titanium boasts excellent resistance to high temperatures and corrosion, making it a good choice for longevity and consistency of performance. A popular titanium grade is Ti6Al4V, sometimes known as Grade 5 or TC4. Meanwhile, aluminium is again a lightweight metal that is highly machinable and adaptable for more complex intricate parts.
Aluminium is suited for a range of parts and components, in this case, too. A common grade of aluminium for aerospace is Al7075-T6. A metal generally not preferred is steel- even though incredibly strong, it is also heavy, meaning the aircraft would be less fuel-efficient and harder to support in flight.
Our aerospace partner factory in the Czech Republic counts Airbus as one of their key clients, and we can immediately incorporate this supplier into your supply chain. For more information regarding aerospace CNC machining, contact us here.
With years in the industry, and a team of professional, experienced engineers, our projects are meticulously planned and delivered, so you can rely on us every time.