Insert Moulding Guide
This guide will discuss what insert moulding is, how it works, what plastic is involved in the process, and its many benefits.
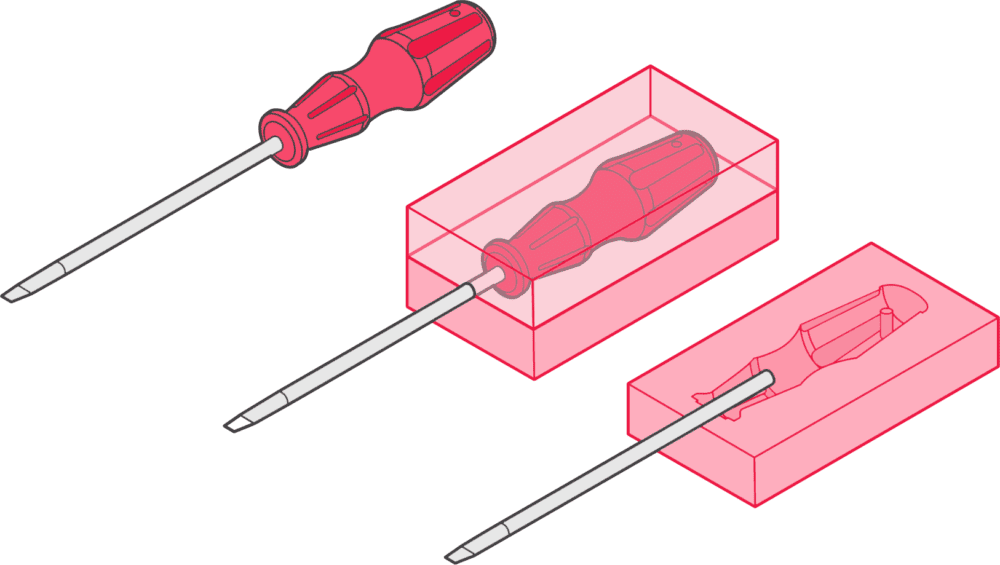
What is insert moulding?
Insert moulding is an injection moulding method where a part is moulded around or over another part, combining them to create a finished product. Insert moulding can combine metal and plastic, or more than one type of plastic or metal, depending on the application. This is usually to strengthen the plastic used or to add a solid, robust finish, more reliable than those using adhesives.
{{cta-banner}}
A typical household example of this process can be seen in the average screwdriver, in which a plastic mould of a handle houses the metal instrument of the screwdriver itself.
This simple, one-step process can save costs and time, making production on a larger scale more efficient and allowing for more creativity in design.
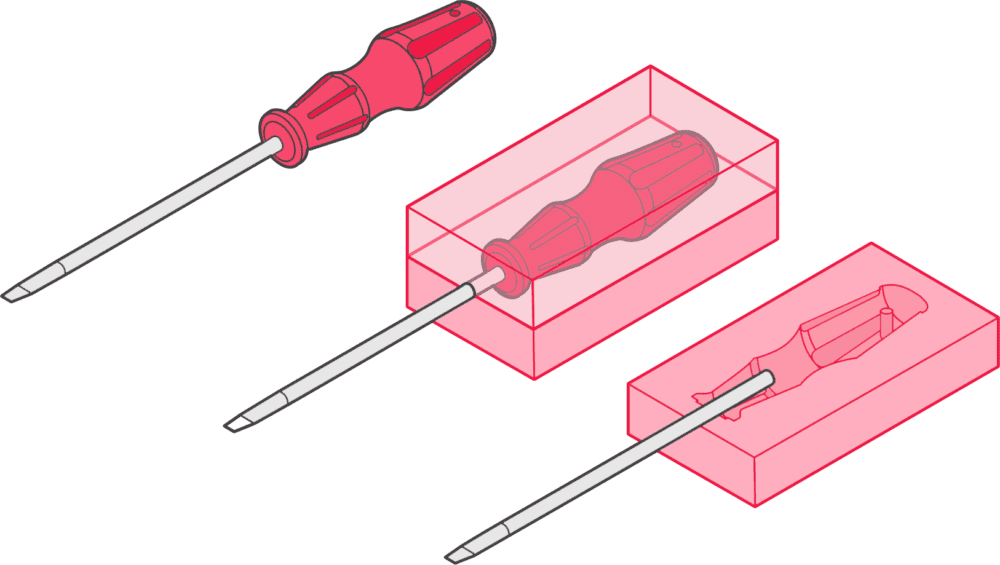
How does insert moulding work?
For example, the metal shaft on a screwdriver is inserted into a mould, and then hot plastic resin is added. The thermoplastic used is then allowed to cool, creating a solid, one-piece finished product.
Removing additional steps and materials needed to bond these different materials makes the end result stronger, more reliable, and tends to cost less to make.
Although insert moulding and over moulding are terms that are often used interchangeably, the processes used are quite different. In over moulding, the part is moulded once and then in the same machine a second time. This process is very technical and requires specialist know-how, tight tolerances and excellent toolmaking. Insert moulding is, by comparison, relatively simple, an already manufactured part made from metal or plastic is inserted into the injection moulding tool and then has plastic moulded around it. An example of this can once again be demonstrated in the example of a screwdriver, in which a pre-existing metal insert is overlaid with a thin, pliable overmold, creating one single product.
What applications can benefit from insert moulding?
Commonly used in various industries, insert moulding can be found in medical, automotive and electrical components.
An excellent example of the benefit of insert moulding can be seen in a good, strong pair of scissors. While they can be made using adhesives or connectors, by inserting the metal blades into a mould and using thermoplastics to create the handle, the overall effect is a solid single piece that is more reliable and easier to use.
One of the most common ways to incorporate insert moulding into production is using brass-threaded inserts for durability. The threads in the brass are more resistant to wear, so they are great for moving components. You can see these in dials and knobs around the home – allowing the consumer to screw and unscrew the part multiple times without affecting its usefulness.
As the thermoplastics used in the insert moulding process usually have insulating properties, they are often used in the production of electronics – and with no assembly required, the parts created can be very small. With water resistance and functional strain relief, the suitable thermoplastic in the insert mould can add all the protection that is needed.
Another application of insert moulding is for aesthetic purposes. For example, a premium car badge could be created by inserting metallic-looking plastic or even metal and then moulding over it in polycarbonate to give a rugged, aesthetically exciting design.
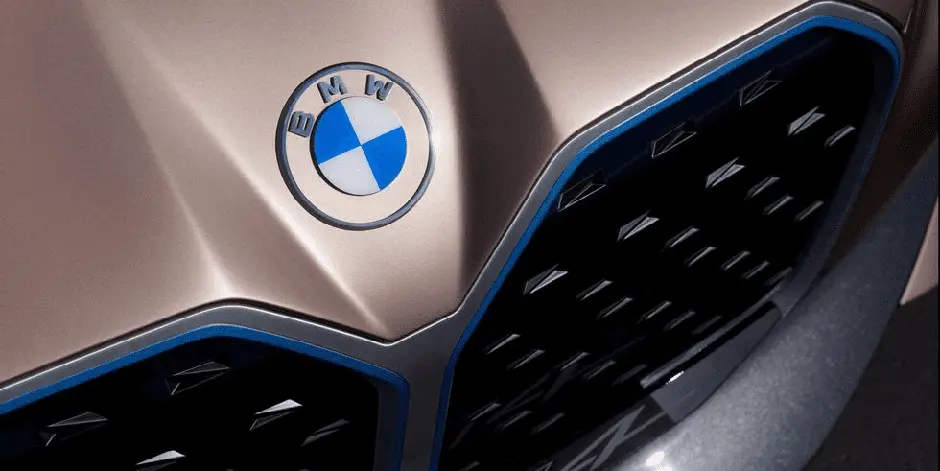
Insert moulding vs over moulding
Although distinctly different processes, there are occasions in which both insert moulding and over moulding can be employed to achieve first-class results. Once again, the manufacturing process undertaken to create a screwdriver can be used as an example.
Within the process of manufacturing this tool, a finished metal insert is moulded over with hard, strong plastic. Following this, the tool is then over moulded with a thin, pliable rubber over-mould, giving the product some grip and the screwdriver a handle. This demonstrates how, despite the different processes of each method moulding, they can be employed in tandem with one another to achieve manufacturing aims.
Using vertical injection moulding machining for insert moulding
Typically, the insert moulding process can use any injection moulding technology, but it is often most successful when a vertical injection machine is used.
Working in much the same way as a horizontal injection system, the vertical option makes use of gravity to ensure that the mould is filled, and the thermoplastics are held in place before the cooling process begins. This ensures that the plastic wall is of equal thickness, without air bubbles or gaps.
Horizontal injection machines often require tight tolerances to ensure a quality finish, whereas the vertical machine produces better results without worrying about misalignment.
The process itself is relatively simple. The metal or preformed part is inserted into the mould before the vertical injector adds the molten plastic. The mould is closed, and the contents are allowed to cool before it is ejected, ready for the next stage in the production process.
What plastics can be used in the insert moulding process?
The insert moulding process can use a range of plastics, and even more than one type, in each mould. The thermoplastic used will depend entirely on the required finish and the function of the part for the end-user.
- Acrylonitrile Butadiene Styrene (ABS) – lightweight, flexible, and opaque, ABS is commonly found in drain pipes, kitchen appliances and LEGOS.
- Polycarbonate – transparent and lightweight, used in creating mobile phones, DVDs and larger products like greenhouse panels.
- Polyethylene (HDPE/LDPE) – available in a range of densities, easily recyclable, and usually found in plastic bags and plastic bottles.
- Polyamide (Nylon) – One of the most well-used thermoplastics, nylon can be found in medical and automotive applications and is often used in sports equipment, clothing and shoe production.
Benefits of insert moulding
Insert moulding has several simple and practical benefits that make it a good choice for both complex design ideas and high-volume production, including:
Reduced production costs
As the insert moulding process creates a single, solid, finished piece, there is no need for additional labour or parts.
There are significant time savings to be made with an efficient insert moulding process. Multiple parts can be created and cooled in a production line without much need for monitoring, thanks to easier quality control.
Flexible design
The simple method of bonding metal and plastic to create a single finished piece leads to more flexibility in design ideas. This process is suitable for creating lightweight and small pieces so that they can be used in any number of delicate applications – and thanks to the wide range of thermoplastics that are suitable for use with an insert moulding process, the end product can have many different finishes.
Wear-resistant
The insert moulding process is commonly used to reinforce certain materials, create handles or grip areas, or ensure long-lasting use.
The use of metal in screw assemblies is much more reliable than threads moulded into the plastic, especially in high use applications like knobs or dials – and this is also true for threaded shafts, which are usually inserted into a mould at the head for a protected finish.
Range of applications
The flexibility of the finish that can be created using insert moulding means that this production method can have a massive range of applications in several industries.
The inherent properties of the metal used (stainless steel or brass, usually) can be improved thanks to the properties of the plastics by adding chemical and water resistance, electrical insulation, and even vibration and shock protection.
Explore our services here and learn how we can help you with your next project.